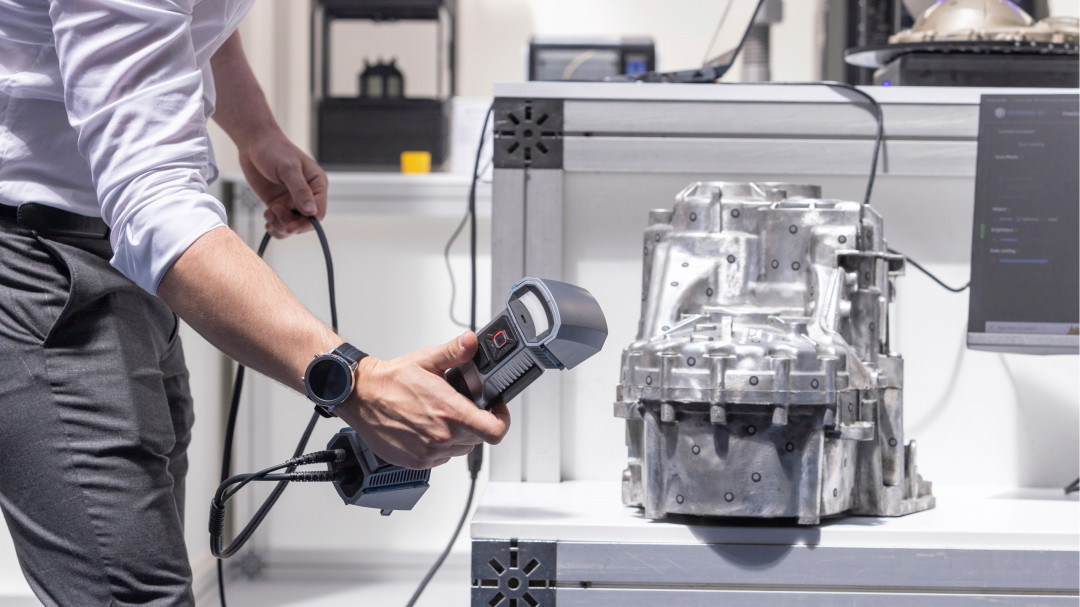
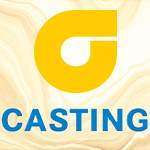
At voestalpine Stahl, Linz, 3D measuring technology has been in use for many years. Increased demands required flexible, hand-held systems with higher accuracy and shorter measuring times. The company therefore opted for 3D measuring technology from Creaform, Leinfelden-Echterdingen, Germany.
By Jérôme-Alexandre Lavoie
voestalpine Stahl GmbH is the lead company of the Steel Division, the largest of voestalpine's four divisions. Divisions and the international steel competence center of the voestalpine Group. Its products are used for the automotive, electrical, domestic and processing industry segments. In Linz, the company operates a fully integrated metallurgical plant with all process stages at a single location: coke plant, blast furnace, steelworks, hot and cold rolling mill, as well as galvanizing and strip coating.
3D measurement technology has been in use at voestalpine for many years. Terrestrial 3D laser scanners are used to monitor the condition of plant components and to log damage. Component measurements were also carried out partly with these systems, but also with an older optometric method.
"Over time, the existing laser technology could no longer keep up with the increased demands in the area of digitization. In particular, the areas of reverse engineering and quality control demanded flexible, hand-held systems with a higher degree of accuracy that would also shorten the measurement time," explains Christian Haider, process manager at TSE – Electrotechnical Center of voestalpine in Linz. The new systems should also be able to scan surfaces of various textures – including glossy surfaces – without any problems. The measuring systems should still be able to be used directly in production and should therefore be insensitive to oscillations and vibrations. Simple and fast further processing of the data obtained was essential for integration into the existing processes.
The effectiveness and efficiency of Creaform's 3D measurement technology in handling the systems were convincing, and voestalpine Stahl GmbH decided to purchase the HandySCAN Black and MetraSCAN Black 3D scanners and the HandyPROBE tactile measurement system.
"Integration into the workflow went without a hitch," comments Maximilian Burger, measurement technician at TSE – voestalpine's Electrotechnical Center in Linz. "The mobility of the measuring systems allows them to be used in the plant, in the workshop or at the measuring station. We export the acquired data from the VXelements acquisition software and prepare it with common third-party software solutions for reverse engineering as well as for quality control. This means that after data acquisition, the measurement results can be seamlessly integrated into the workflow."
What are the measuring systems used for?
voestalpine Stahl GmbH produces steel strip and heavy plate as well as foundry products. Among other things, heavy plates for boiler heads, special pressed parts and offshore platforms are produced, structural steels for steel, bridge and vehicle construction as well as for wind towers. For shipbuilding, the company produces steel and plate in various designs, which are used for offshore applications, deck structures of platforms, and for special ships in the oil and gas industry. voestalpine is also a leader in the manufacture of foundry products for the energy sector, mechanical engineering, and the automotive industry.
Creaform systems are used in all of the above areas, because the combination of HandySCAN 3D and MetraSCAN 3D with HandyPROBE covers a very wide range of measurement tasks. This starts with the measurement of small components, for example the recording of gear profiles in the millimeter range and ends with the logging of entire plant parts. These parts have sizes of more than 10 meters and can weigh several tons.
Quality control
In quality control, castings are completely measured with the combination of MetraSCAN Black and HandyPROBE so that complete technical documentation can be created. The scan data is then compared with the nominal data so that deviations of the actual components from the technical drawings can be detected. Data acquisition is performed using VXelements software, and subsequent analysis of the components is performed in Geomagic Control X. The data is then used for further technical documentation. The data is then released for further processing or for use in the plant area.
Thanks to the portability of the measurement systems, measurements can be performed anywhere and regardless of the size and weight of the components.
Reverse Engineering & 3D print
Another use case is reverse engineering. Some components have to be recreated because no original data or drawings are available. For this purpose, the parts are scanned with the Creaform systems. Based on the scan data, a CAD model is created with Geomagic Design X and then technical drawings are derived for production. In some cases, these spare parts are 3D printed in-house or conventionally manufactured with CNC machining centers.
What are the tangible improvements and future plans?
"Using the Creaform measuring systems led to significant improvements in the areas of accuracy of the measurement results and reduction of the measurement time. The response behavior on different surfaces is also a positive surprise," explains Maximilian Burger. In the future, the range of applications for the systems in the company is to be extended to other areas. It is planned to use the scanners as well as the HandyPROBE tactile measuring system in the inventory and retrofitting of plant components, reverse engineering of special machine construction components, quality control for externally and in-house manufactured components, in production planning as well as in the support of projects.
"The Creaform systems offer many new possibilities along the value chain of plant engineering. With this technology, we are contributing another step to the sustainability and technological diversity of voestalpine, as a globally active steel and technology group," adds Christian Haider.