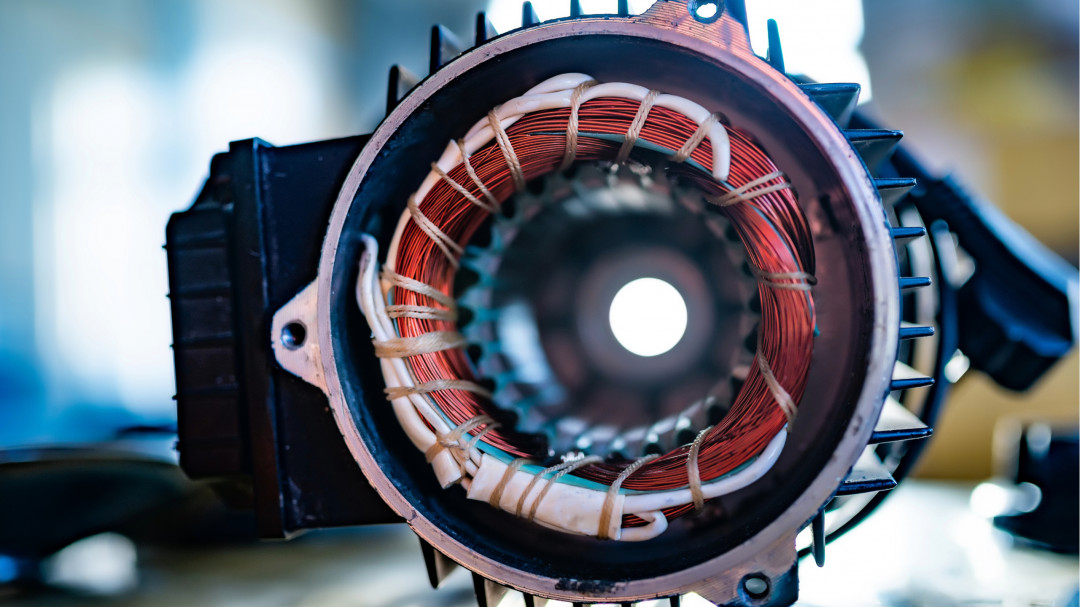
The electrification of the drivetrain is progressing steadily. The electric motors used contain valuable raw materials such as copper, but also rare earth metals such as neodymium, for which China has a virtual monopoly and which cannot be recovered using current recycling methods. In addition, the raw materials used are associated with a poor CO2 balance compared to combustion engines. This makes it all the more important to extend the useful life of the engines. "Innovative value retention strategies offer great potential for reducing emissions in terms of sustainability," says Julian Große Erdmann, a scientist at the Fraunhofer Institute for Manufacturing Engineering and Automation IPA in Bayreuth. In the REASSERT project, the researchers are working with Schaeffler (consortium leader), the Karlsruhe Institute of Technology KIT, BRIGHT Testing GmbH, iFAKT GmbH and Riebesam GmbH & Co. KG are developing innovative methods for reconditioning electric motors and reusing them in vehicles. They are focusing on the value retention strategies of reuse, repair, remanufacturing and material recycling. These are key elements for a circular economy that makes it possible to reduce the consumption of natural resources and minimize the amount of waste. The project is funded by the Federal Ministry for Economic Affairs and Climate Protection.
Raw material recycling is currently the established strategy for preserving value. Manual or automated recycling is used to recover copper and aluminum in particular. To do this, the electric traction motors are removed, shredded, sorted into the individual material fractions and melted down. However, the material recycled in this way, which is contaminated, can no longer be used in motors and individual components and assemblies are destroyed. Raw material recycling should therefore only be chosen as the last option for recycling and replaced by the high-quality value retention strategies of reuse, repair, remanufacturing and mechanical recycling. "We want to design a closed-loop system in which valuable resources are reused in order to become less dependent on raw material imports and minimize the extraction of raw materials," explains Große Erdmann. By reuse, the project partners mean the reuse of the complete engine in a second use, while repair means the replacement of defective components and assemblies. In remanufacturing, all components are removed, cleaned, refurbished and reused. "With these strategies, you need fewer raw materials such as rare earths, copper, etc. At best, you still need them for spare parts," explains the researcher. With material recycling, the project partners are planning to dismantle the engine according to type before shredding. The project partners are using reference engines for the passenger car sector to analyze which value retention strategies should be used in each case.
A complete process chain is being created as part of the project, with each station having its own demonstrator or test stand - from the incoming inspection for the classification of the engine to disassembly, demagnetization, cleaning, diagnosis of the components, reconditioning through to reassembly and end-of-line testing, where the functionality of the engine is examined. "For example, during this process, a motor housing with minor signs of wear would be classified for reuse and, if necessary, refurbished using machining processes to ensure functionality. Depending on the chosen value retention strategy, different process steps and process chains are required, so the refurbishment effort can vary," explains the engineer. One challenge, for example, is dismantling and reusing the magnetic materials used in the motors. "A rotor with permanent magnets is difficult to dismantle into its components using mechanical methods, even in the manual dismantling process, due to the coating of the magnets and their adhesion. The aim here is to establish low-destructive disassembly processes."
An AI decision-making tool developed in the project, which has access to the product and process data of an electric motor stored in a digital twin, also helps to select the best value retention strategy.
The knowledge gathered in the project is to be used for the design of new electric motors. The aim is to develop a prototype of a motor for the circular economy that can be easily dismantled and to which the four value retention strategies mentioned above can be easily applied.