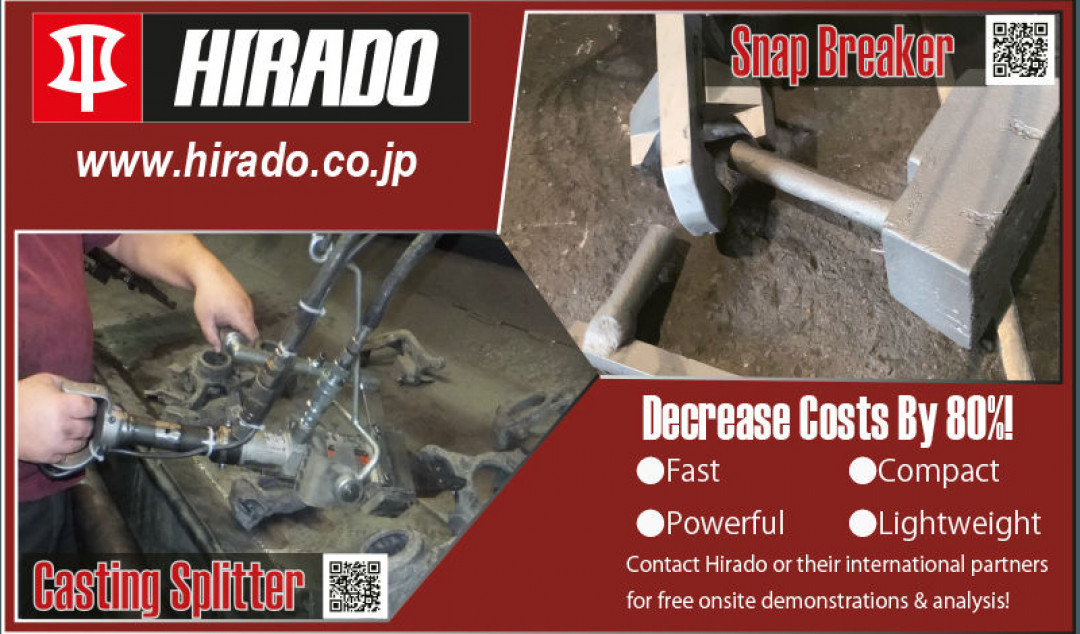
-Anzeige-
Während Gießereien auf dem Weg sind, sich von der COVID-Pandemie zu erholen, wird ein verstärkter Schwerpunkt auf Kostensenkungsmethoden, eine effektive Nutzung der Produktion und die Steigerung der Wettbewerbsfähigkeit der Gießerei auf dem Markt in einer sich ständig ändernden Branche gelegt. Über die Analyse von Prozessen und die Implementierung neuer innovativer (digitaler) Technologien in mehreren Teilen des Produktionsprozesses ist viel geschrieben worden. Ein Bereich, der jedoch oft übersehen wird, ist der Putzprozess. Hier können große Kosteneinsparungen und Verbesserungen erzielt werden.
Hirado Kinzoku Kogyo co.,ltd., ein japanischer Hersteller innovativer Hydraulikwerkzeuge für die Gießerei-Industrie, präsentiert zum ersten Mal zwei separate Testfälle, die erhebliche Verbesserungen und drastische Einsparungen von bis zu 80 % ermöglichen.
Hirado stellt seinen innovativen, leichten und schnelllaufenden hydraulischen Keil, den EP Casting Splitter, seit 1980 her, der aktuell in über 20 Ländern weltweit eingesetzt wird (Bild 1).
Die einzigartige Hydrauliktechnologie von Hirado ermöglicht durch einen leichten Trennkeil Leistungsstärke und Schnelligkeit. Darüber hinaus sorgt die patentierte Dual-Switching-Technologie dafür, dass nur die benötigte Leistung geliefert wird, wodurch Verschleiß,- und Ausfallzeiten reduziert und gleichzeitig die Lebensdauer der Geräte verlängert wird. Die Bedienung erfolgt beidhändig wodurch die Sicherheit erhöht, Ermüdung reduziert und ein schnelleres Handling ermöglicht wird.
Hirado stellt mit dem SBH Snap Breaker (Bild 2) auch einzigartige Werkzeuge für das Brechen von Gießläufen her.
Wenn der Snap Breaker über die Läufe gelegt wird, bricht er sie mit Hilfe der Hydraulikpumpe innerhalb von Sekunden in zwei Hälften. Das Ergebnis ist eine sicherere, schnellere und einfachere Bedienung. Da der Snap Breaker keine Verbrauchsmaterialien benötigt, können die jährlichen Verbrauchsmaterialkosten drastisch gesenkt werden. Die Bruchzeit eines einzelnen Läufers wird ebenfalls drastisch reduziert, wodurch Arbeitszeit und Kosten gesenkt werden. Die stark verbesserten Ergonomie- und Sicherheitsbedingungen für den Mitarbeiter sind nur schwer in Geld umzuwandeln. Nachfolgend finden Sie Zusammenfassungen der einzelnen Testfälle. Vollständige Berichte sind über Hirados internationales Partnernetzwerk weltweit verfügbar.
Testfall 1 (Snap Breaker) : 80 % Kostensenkung durch das Brechen von Gießläufen in einer deutschen Gießerei
Die an diesem Testfall beteiligte Gießerei befindet sich in Norddeutschland. Die Formlinien sind manuell und halbautomatisch. Die Gießerei produziert bis zu 40 Formen pro Stunde. Es werden verschiedenste Grau- und Sphärogussteile (bis GJS 700 ) mit Gewichten bis 3.000 kg hergestellt.
Die Abmessungen der einzelnen Läufe haben einen Bereich von 30 bis 60 mm in runden und quadratischen Formen. Da die meisten Läufe 1 bis 2 Meter lang sind, ist es notwendig, sie in kleinere Stücke zu schneiden/brechen. Dadurch wird eine Brückenbildung im Ofen beim Umschmelzen verhindert. Die kleineren Stücke erhöhen auch die Packungsdichte des Ofens, was energieeffizienter ist.
Die Gießerei schneidet zurzeit die Läufe mit großen Schleifmaschinen ab. Dies löst das Überbrückungsproblem, erhöht jedoch die Arbeitskosten und die Durchlaufzeit und verursacht meistens hohe Kosten für Verbrauchsmaterialien (Schleifscheiben). Beim Besuch in der Gießerei wurde uns ein Container mit den verschlissenen Schleifscheiben gezeigt, die teuer entsorgt werden müssen (Bild 3).
Aufgrund der oben beschriebenen Hintergrundinformationen und Demonstrationserfahrungen wurde die SBH-2 (222 kN Leistung) für die erste Vor-Ort-Demonstration in Deutschland eingesetzt. Der Snap Breaker SBH-2L (397 kN Power) wurde als die beste Option angesehen. Nach dem Kauf des SBH-2L stellte sich dies als richtig heraus. Dies wurde bei der jährlichen Inspektion erneut bestätigt.
Der Test zeigte, dass der Snap Breaker SBH-2 GJS 450 50x50 mm Angüsse mit 80 % Kraft (177 kN) innerhalb von 2 Sekunden brechen konnte (Bild 4). Die 55-mm-Lauf konnte jedoch aufgrund der maximalen Öffnung und der begrenzten Leistung des SBH-2 nicht gebrochen werden. Aufgrund der Demonstrationsergebnisse konnte jedoch gefolgert werden, dass der SBH-2L aufgrund seiner höheren Leistung (397 kN) für die Aufgabe ausreichen würde.
Die Daten der aktuellen Schleifmethode (Gehalt, Verbrauchsmaterialkosten, beteiligte Mitarbeiter, Zeit) wurden von der Gießerei bereitgestellt und den Ergebnissen der Demonstration gegenübergestellt. Es zeigte sich, dass man die Hälfte der Zeit brauchte, um die Läufe mit dem Snap-Breaker abzuschneiden. Es zeigte sich auch, dass die Verbrauchsmaterialkosten von bis zu 39.000 Euro um über 95 % gesenkt werden konnten, da der Snap Breaker praktisch keine Verbrauchsmaterialien benötigte.
Der Einsatz des Snap Breakers in der Gießerei reduzierte die Arbeitszeit und erhöhte die Sicherheit der Mitarbeiter. Die Kostenanalyse zeigt, dass die aktuellen jährlichen Kosten von 70.000 Euro um mehr als 80 % gesenkt werden können. Diese enorme Menge an Vorteilen und Einsparungen haben die Investition in den Snap Breaker gerechtfertigt.
Testfall 2 (Casting Splitter – Trennkeile): Bessere Arbeitsmoral und Produktion, weniger Ausfallzeiten und starke Kostensenkung in Italien
Die an diesem Testfall beteiligte Gießerei befindet sich in Norditalien. Ziel war es, eine höhere Produktionsgeschwindigkeit und bessere Arbeitsbedingungen für die Mitarbeiter mit weniger Ausfallzeiten und natürlich, wenn möglich, Kosteneinsparungen zu erreichen. Die Formlinien sind neu, vollautomatisch und können bis zu 300+ Formen pro Stunde produzieren.
Die Gussteile sind hauptsächlich für die Automobil- und Bauindustrie gedacht. Durchschnittliches Gussgewicht 40 kg mit Materialqualitäten bis GJS 700, überwiegend GJS 450. Während der Vorführung stehen in der Gießerei zwei Mitarbeiter auf einem Metallförderband (nicht vibrierend). Ein konkurrierendes hydraulisches Keilsystem wird bereits verwendet, um Speiser und Gießläufe von den Gussteilen zu entfernen. Der aktuelle Hydraulikkeil wiegt 30 kg und hat eine maximale Kraft von 126 kN.
Während der Demonstration lief die Formanlage und die restliche Produktion auf Hochtouren. Die zwei Mitarbeiter konnten die fertigen Gussteile nicht in der geforderten Geschwindigkeit abarbeiten. Daraus resultierend werden die Gussteile nicht kontinuierlich verarbeitet und regelmäßig vom Förderband entfernt. Später werden diese Gussteile wieder auf die Strecke gelegt, sodass die Trennung der Läufe trotzdem stattfinden kann.
Das verursacht Nebenkosten. Das Ergebnis ist ein Engpass und eine schwierige Produktion. Man entscheid sich, die Produktion in der Woche für ein paar Tage zu schließen. Um diesen unnötigen Stopps entgegenzuwirken, erwog die Gießerei den Einsatz zusätzlicher Hydraulikkeile (und Mitarbeiter).
Aufgrund der bekannten Hintergrundinformationen, der Größe der Anschnitte (max. 30 x 30 mm) und der Demonstrationserfahrung wurde beschlossen, den Casting Splitter EP-80N(23) zu testen (Bild 5). Durch den Austausch anderer Keile und Gegenkeile können Öffnungsweite und Länge der Keile einfach angepasst werden. Ein EP-80N(23) kann einfach zu einem EP-80N(30)L umgebaut werden. Der Test des EP-80 wurde in der Produktion mit eigenen Mitarbeitern der Gießerei an den Gussteilen durchgeführt.
Auf der anderen Seite des Förderbandes nutzte ein anderer Mitarbeiter den aktuellen Hydraulikkeil, um direkt vergleichen zu können. Während des Tests wurde der Unterschied zwischen dem derzeit verwendeten Hydraulikkeil und dem EP-80(23) sofort deutlich. Der Gewichtsunterschied (13 kg) bedeutete, dass der Arbeiter mit der EP-80(23) den Guss viel schneller putzen konnte und dadurch Zeit sparte. Weil der EP-80(23) sowohl horizontal als auch vertikal und die Gegenkeile um 360 Grad gedreht werden können, konnte der Mitarbeiter das Gussstück vom Lauf trennen, ohne dieses mit der Hand aufzunehmen .
Im Vergleich dazu musste der Arbeiter mit dem aktuellen Hydraulikkeil jedes Gussstück aufnehmen und verlor dadurch Zeit. Neben der Geschwindigkeit wurde auch beobachtet, dass die EP-80(23) das Umlaufsystem von jedem Gussteil mit 70 % Leistung in einem Schuss entfernen konnte (Bild 6). Der derzeitige hydraulische Keil konnte das Eingießsystem bei den meisten Gussstücken nicht in einem Schuss entfernen und brauchte mehrere weitere Schüsse. Die aktuell eingesetzte Hydraulikpumpe kann keinen Druck aufbauen und läuft immer mit 100 % Leistung im Gegensatz zur Hirado-Pumpe, die immer Druck aufbaut.
Aufgrund der oben genannten Vorteile im Vergleich zu den derzeit verwendeten Hydraulikkeilen konnte gezeigt werden, dass der EP-80N(23) das Eingießsystem in weniger als der Häfte der Zeit (19 Gussteile vs. 8 Gussteile) und sogar bei geringerer Leistung entfernt hat (70% vs. 100%), weniger Energie braucht (3,7 kW vs. 5,5 kW) und weniger körperliche Ermüdung aufgrund des Gewichtsunterschieds (17 kg vs. 30 kg) aufweist. Die Daten aus diesem Test - sowohl die Ausrüstung als auch die von der Gießerei bereitgestellten Daten (Mitarbeitergehalt, Fähigkeiten der Formlinie) wurden in Hirado Dokumentation verwendet, um die jährlichen Kosten und Einheiten zu berechnen, die zur Lösung des Engpassproblems erforderlich sind.
Die Analyse ergab, dass zur Lösung des Engpassproblems zusätzlich drei Gießereikeile (und drei Betreiber) des aktuellen Herstellers erforderlich wären. Dies würde zum Kauf von fünf Gießereikeilen führen, die von fünf Bedienern eingesetzt würden. Hierdurch würden Kosten von ca. 180.000 Euro entstehen. Im Vergleich dazu wären bei einem Wechsel zum EP-80-System von Hirado nur zwei Systeme und zwei Bediener erforderlich. Im 1. Jahr würde die Kostenreduktion 30 % betragen, während auf 5-Jahres-Basis die Kostenreduktion zu mehr als 60 % führen könnte. Durch die Implementierung des Hirado EP-80-Systems konnte die Gießerei ihre aktuelle Produktion um 40 % steigern und eine schnelle Lieferzeit sicherstellen.
Hirado in Deutschland und Europa
Die Zusammenfassung der obigen Testfälle bietet nur eine kleine Vorstellung wie die Gießereimaschinen von Hirado zu einer effizienteren Produktion, einer höheren Rentabilität und einer wettbewerbsfähigeren Gießerei beitragen können. Hirado und sein Partner Fatol Mulder sind ebenfalls stolz bekanntzugeben, dass, unabhängig von der aktuellen Pandemie, mehrere Exemplare des EP Casting Splitter und SBH Snap Breaker in verschiedenen Gießereien installiert wurden.
Neben innovativen Maschinen ist Hirado auch der Meinung, dass Service und Feedback genauso wichtig sind. Daher ist die Partnerschaft von Hirado mit Fatol-Mulder BV sehr wichtig. Fatol-Mulder verfügt über ein breites Angebot an Maschinen und Anlagen für die Gießerei-Industrie sowie langjährige Erfahrung. Wenn Hirado einen Partner im Ausland auswählt, betrachten wir mehrere wichtigen Faktoren. Am wichtigsten sind Fachkenntnisse auf diesem Gebiet, die Fähigkeit einen soliden Service zu bieten und engagierte Vertriebsmanager, die sich wirklich darum kümmern, die beste Lösung für den Kunden zu bieten. Fatol-Mulders erfüllten diese zentralen Anforderungen und die Synergie zwischen unserer Unternehmenspolitik und unseren Produkten ist hervorragend. Ihr Fachwissen, die gemeinsame Vision und ein guter Kundenservice sind ein weiterer Aspekt, der von größter Bedeutung ist.
Wir alle glauben, dass wir keine Maschinen verkaufen, sondern Lösungen anbieten. Fatol Mulder ist auch in der Lage, eine kostenlose Vor-Ort-Analyse und Demonstration der Maschinen, wie in den oben genannten Testfällen beschrieben, anzubieten. Hirado freut sich darauf, unsere Marke mit Fatol Mulder in den Niederlanden, Belgien, Deutschland, Österreich und der Schweiz auszubauen und wir sind weiterhin bestrebt, die harte Schwerstarbeit von Gießereien sicherer, schneller und effizienter zu machen.
Um mehr über Hirado und ihre innovativen Maschinen zu erfahren, besuchen Sie bitte die offizielle Website unter www.hirado.co.jp/en