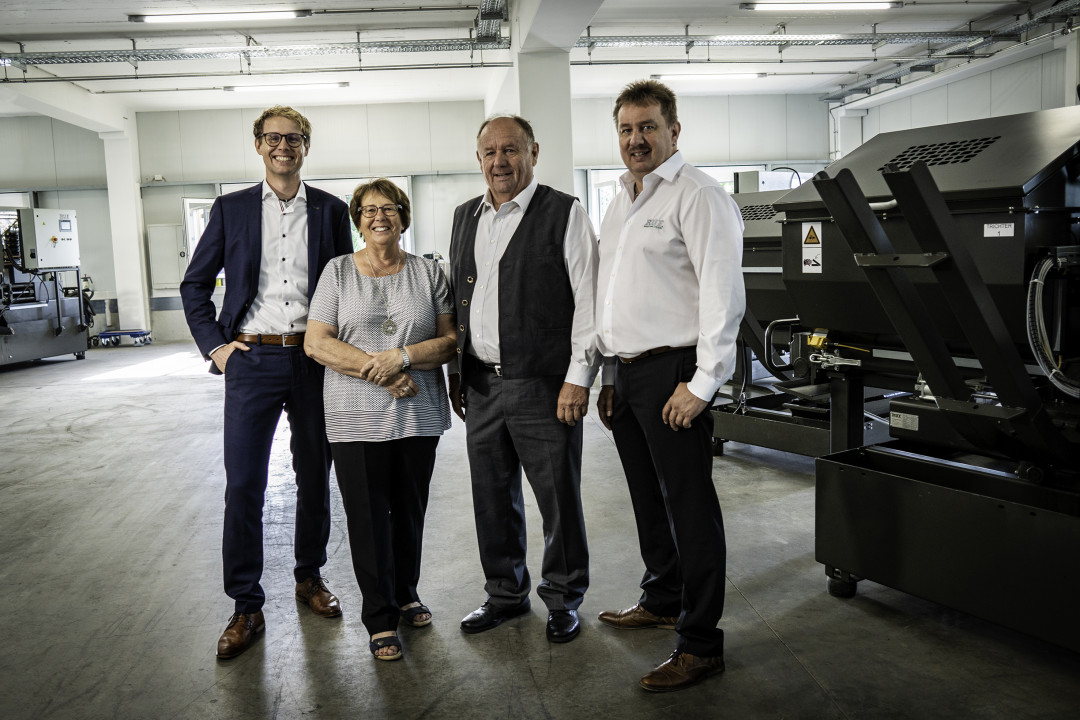
In 1993, RUF Maschinenbau succeeded in transferring the principle of alternating mould briquetting successfully from wood residues to metal chips. Two years later, in addition to the "wood machines", the first ten briquetting systems for metal had already been sold. Today, RUF briquetting technology has become an indispensable part of the recycling of metal chips. A success story from a medium-sized company.
When Hans Ruf developed his first briquetting press in 1985 and founded his own company shortly afterwards, he had no idea that it would become a real success story. Today, RUF Maschinenbau GmbH & Co.KG, Zaisertshofen, is the world market leader for hydraulic briquetting presses - a technology that started with wood but eventually also revolutionised the recycling of metal scraps.
The basis for this was the invention of so-called hydraulic exchange mould briquetting and its transfer from wood to metal, which the inventor Hans Ruf achieved 30 years ago. The decisive factor was various adaptations of central components such as the press mould, press plunger and hopper. To prevent excessive wear, they were designed from hardened steel, which is particularly resistant. In addition, Hans Ruf designed all relevant wear parts so that they can be changed quickly and easily.
In addition, the resourceful machine builder decided on a round format for metal briquettes, as his calculations and numerous tests showed that the pressure distribution during the pressing process works best here. Even then, the machines produced briquettes with a very high density.
Steady growth in sales of metal presses
Interest in the market was correspondingly high. Within two years, RUF sold the first ten machines, and after ten years the hundred mark was passed. In the next ten-year period (2003 to 2013), the company increased its sales to a good 700 metal briquetting systems, and from 2013 to 2023 the number almost doubled again to around 1300.
Last year alone, the Bavarian machine manufacturer sold 185 metal briquetting systems, which can briquette not only aluminium but also steel, stainless steel, cast iron, copper materials, magnesium and titanium and are used in a wide range of industries. Among the most important are the broad field of the metal-cutting and automotive industries as well as foundries and recycling companies. All of them benefit from the reliable technology in several ways.
With RUF briquetting systems, users can conserve resources and increase their profitability at the same time. The more space-consuming the chips are after processing, the more important efficient briquetting is. This is the only way to achieve a high briquette density that is close to the solid material. The decisive factor here is a high specific pressing pressure. With RUF systems, for example, this is up to 4,000 kg/cm2 for cast iron and up to 3,000 kg/cm2 for aluminium.
Briquetting offers many advantages
The advantages of RUF briquettes over loose chips are manifold: Firstly, all users save a lot of space. Secondly, logistics are simplified - both internal forklift logistics and external transport logistics, i.e. lorry journeys from manufacturing companies to recycling plants or smelters. Thirdly, the metal yield can increase when melting down. The background to this: Since the chips are light, they float in the melting bath. Consequently, high burn-up losses occur. Briquettes, on the other hand, immerse quickly thanks to their high density and thus prevent unnecessary burning.
A fourth plus point is based on the fact that high-performance machining often involves the use of cooling lubricants, which also end up sticking to the chips. When briquetting with RUF systems, it is possible to reduce the moisture value of the metal chips from sometimes 15 percent to less than two percent, depending on the material, and to collect the valuable wet for later recycling.
In order to meet the volume requirements of the respective user in the best possible way, the Bavarian machine manufacturer offers plants in various sizes and designs. The specific pressures vary just as much as the throughput rates. The latter start at about 30 kg/hour and reach up to 2,500 kg/hour for aluminium, up to 3,000 kg/hour for cast iron and up to 5,000 kg/hour for copper materials, depending on the material.