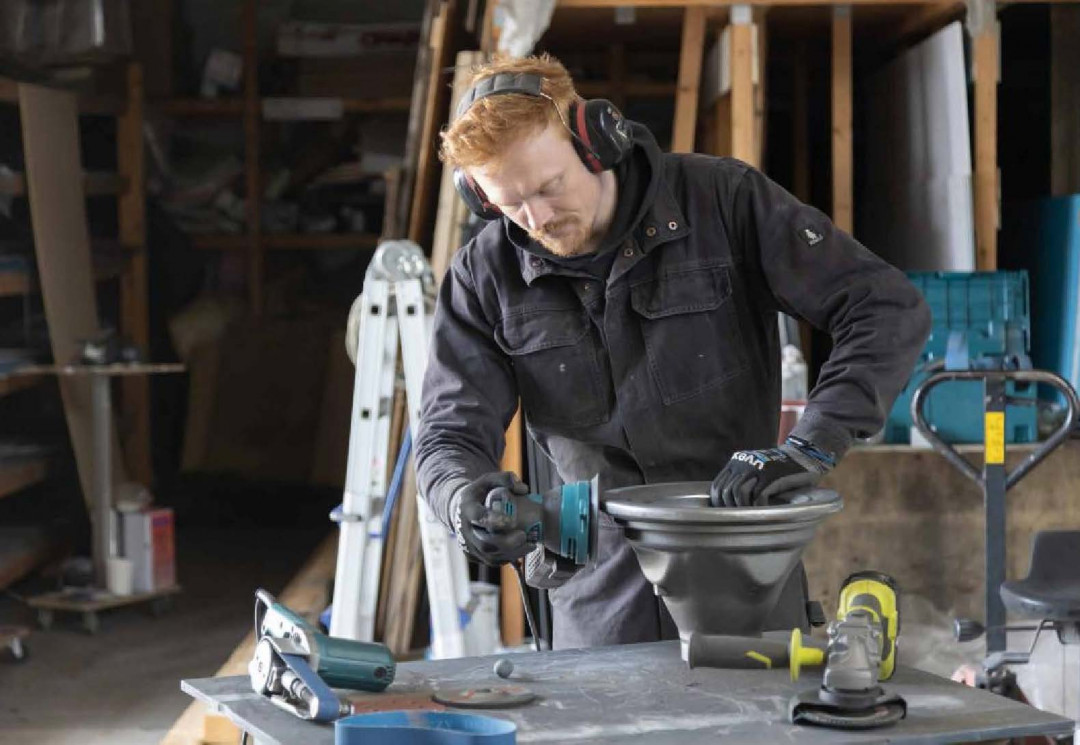
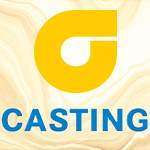
Many months of preparation go into a trade fair appearance such as the one Foseco will make at the "Bright World of Metals". Everything has to go hand in hand in order to have all the exhibits perfectly prepared in time. Assembly, sanding and painting is done right up to the last minute. GIESSEREI was able to take a look behind the scenes of the preparations in Borken and talk to some experts.
BY CHRISTIAN THIEME
It is only a few weeks until the stand is set up - but there is no sign of a hectic pace. In the workshop, pallets are lined up with finished exhibits, while employees work diligently on further exhibits. Martin Scheidtmann (Fig. 1), International Trade Show Manager at Vesuvius GmbH, bends over a printed plan of the trade fair stand and lets his finger glide over numerous stations. "We have many innovations to show visitors again this year, this time on more than 900 m2 in Hall 12." Until then, there is still a lot to be done. The plan shows the open tasks and gives an overview of the overall concept. "As always, all visitors are invited to come to our creative stand and exchange professional ideas with our international colleagues. This time, we will present the exhibits on stacks of pallets that are currently being prepared in the warehouse". Several employees are working on the pallets in the warehouse. Due to the high fire protection requirements, the pallets have to be prepared by hand before they can be used later. Next to them are some of the exhibits that are already ready to be measured.
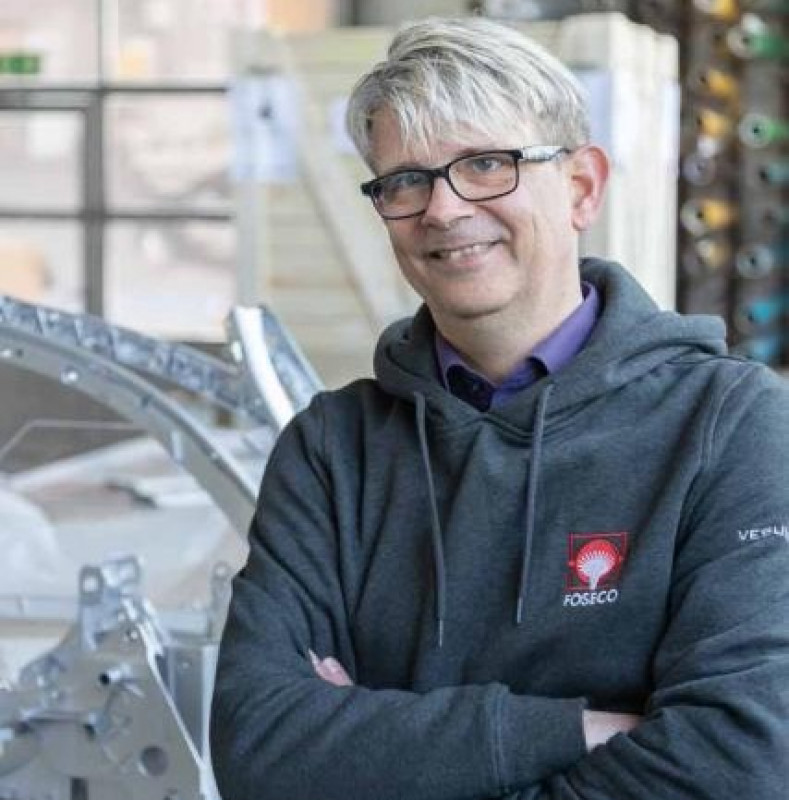
Exothermic feeders for non-ferrous applications
"Here we have prepared exhibits from the non-ferrous sector in order to visualise our new developments in the feeder area," explains Dipl.-Ing. (FH) Arndt Fröscher, European Product Manager Methoding & Coating Non Ferrous. "For example, we have a gearbox housing that was conventionally cast with insulating feeders and natural feeders from above. We then switched to using our new exothermic Feedex NF 1 feeders. The additional energy has meant that we have been able to significantly reduce the size of the feeders. The advantage for the foundry is that a lot of material has been saved in the feeder area, in this case 13 kg (Fig. 2). The removal of the risers is also easier, which reduces the energy consumption and fettling costs.
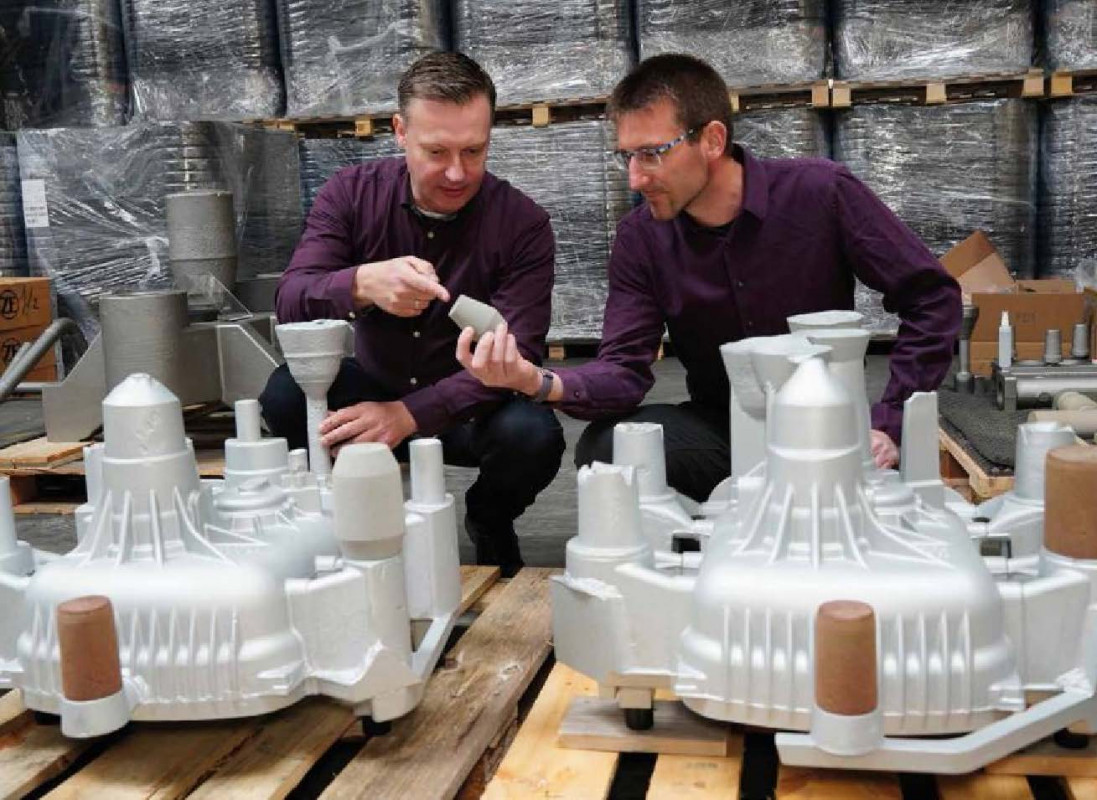
The use of exothermic risers in the non-ferrous sector opens up completely new possibilities for foundries". The optimised feeder system was calculated with a new software plug-in for Magmasoft and validated in a later model test. The new feeder type is also used for copper and copper alloys. Foseco presents a component from the mining sector (Fig. 3). Compared to the original workpiece, the natural feeders were replaced by the new type and thus 35 kg less material had to be poured per cast tube.
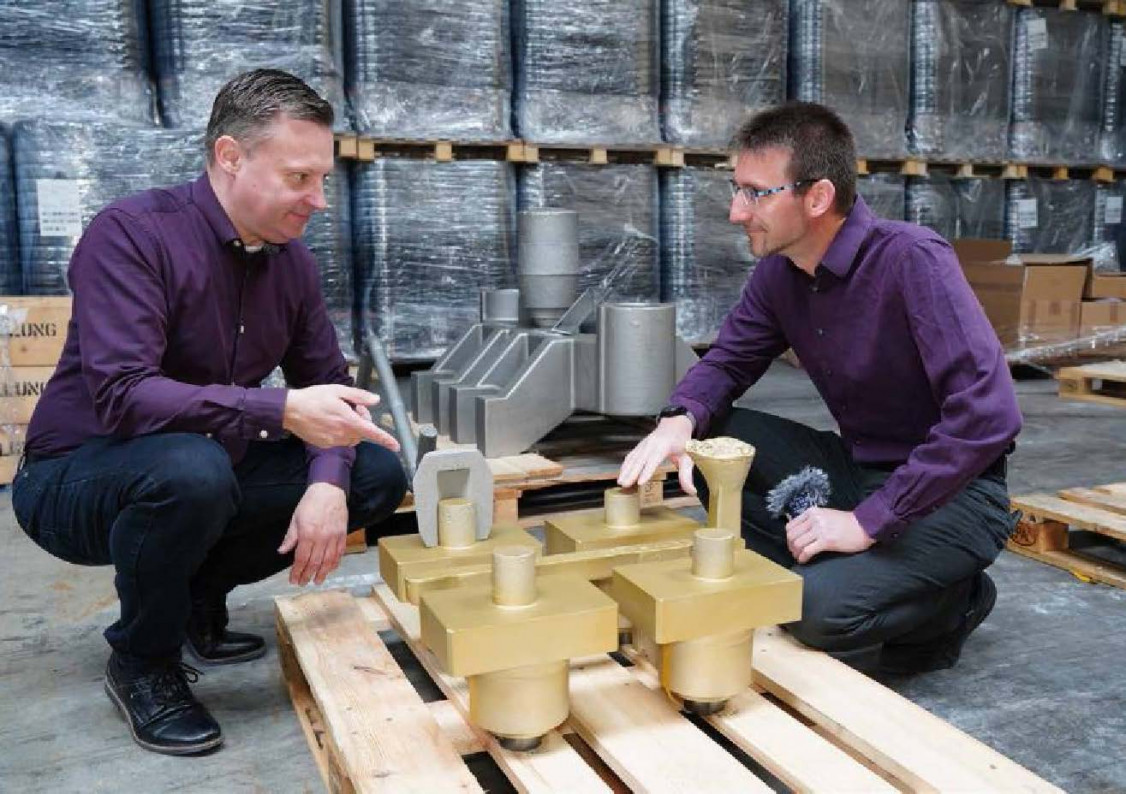
New coating development
As an expert for the coating sector, Harry Wolf will be available to answer questions at the trade fair stand. "A special highlight will be our colour change coating process. In this process, all water-based coatings can be mixed with a colour indicator and bonded to a sand value". The original idea dates back to 2019, when Baumgarte approached us about process problems. It was suspected that the cores were used too soon, i.e. still moist, were used in the casting process," explains the expert. A trial phase brought the realisation that the drying process can be visualised and the drying times of the coating can be adjusted. With the cores, it was evident that drying was ten minutes faster. "A conventional coating changes colour from light to dark, which is not so easy to see. This led to the development of our new product: a coating that uses a colour indicator to show exactly how dry it is. When the coating is wet, it is dark grey, but when it is dry, it is yellow (Fig. 4). However, it can also be seen if the core has been dried too hot, in which case the coating takes on a red colour. These properties save a lot of energy in the process and lead to far fewer casting errors," Wolf states. Another advantage is that the coating also reacts to excessive humidity. This allows foundries to adjust their drying processes and save energy and CO2. "The next step was to save even more energy through a faster drying process. We then optimised the coatings so that we could shorten the drying time by another 15 percent. For this purpose, the solid content was increased, but the good flow properties were retained. With regard to the TALuft, we even managed to design the coating without formaldehyde," Wolf adds.
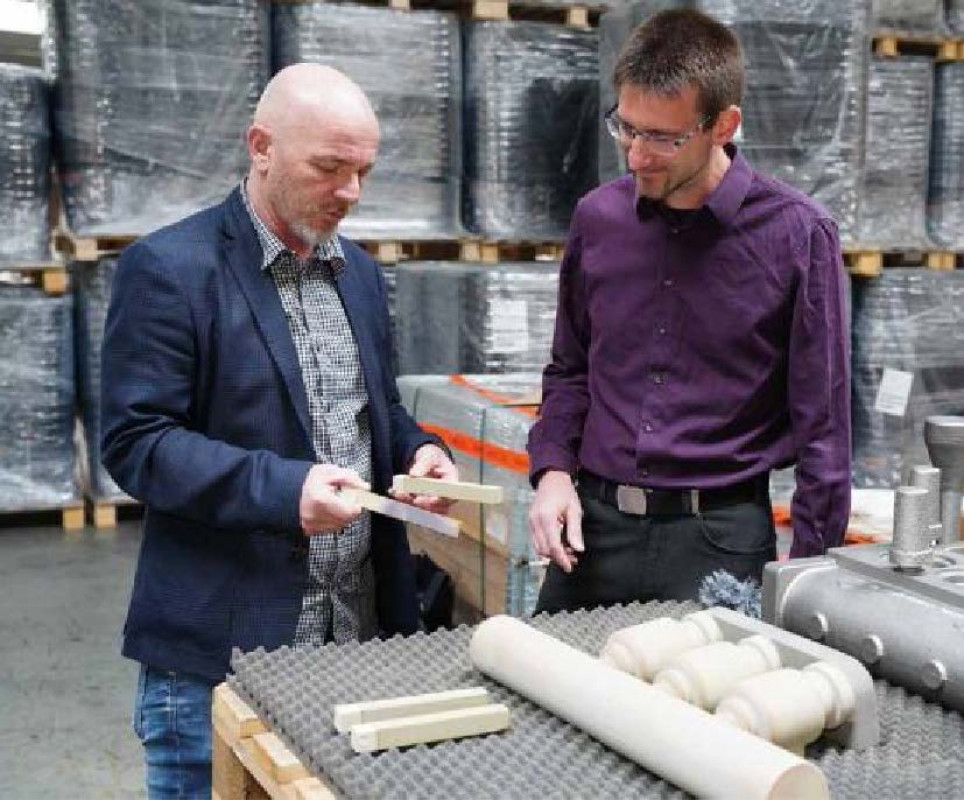
Solutions for steel casting
Cast steel is also represented with a number of exhibits made with filters and feeders. "We have an inlet housing from the food industry here, made of high-alloy cast steel," explains Dipl.-Ing. Stephan Giebing, European Product Manager Ferrous Filtration. "The special feature here is that Hollotex EG Runner for Steel was used". Foseco introduced Hollotex as a product about ten years ago. Previously, the maximum application temperature was limited to 1450 °C. "In our new version, we have added a coating on the inside to achieve a higher temperature resistance. This means that it can now be used up to 1600 °C." Compared to the conventional ceramic system, the new one weighs only a tenth. The individual components can be cut by hand, so that no special lengths are required, which simplifies stock-keeping. "The system is significantly easier to handle and process, which reduces the workload on employees," adds Giebing. "In addition, this pipe appears as a combustion residue on the casting system. As a result, the sand system is not stressed and no ceramic components have to be separated from the sand system". On the last pallet is a crosshead made of ductile cast iron. Stephan Giebing explains that the piece was previously cast using a conventional casting system with a filter. The original weight was 960 kg and a yield of 83 per cent was achieved. Foseco changed the casting to a feeder casting system with the SCK system and was able to reduce the weight to 865 kg and increase the yield to 93 per cent. "We were also able to reduce the footprint of the feeder by 75 per cent," says Giebing. "The special thing is that in this case an additive manufactured filter was used - STELEX Optiflow3D (Fig. 5).
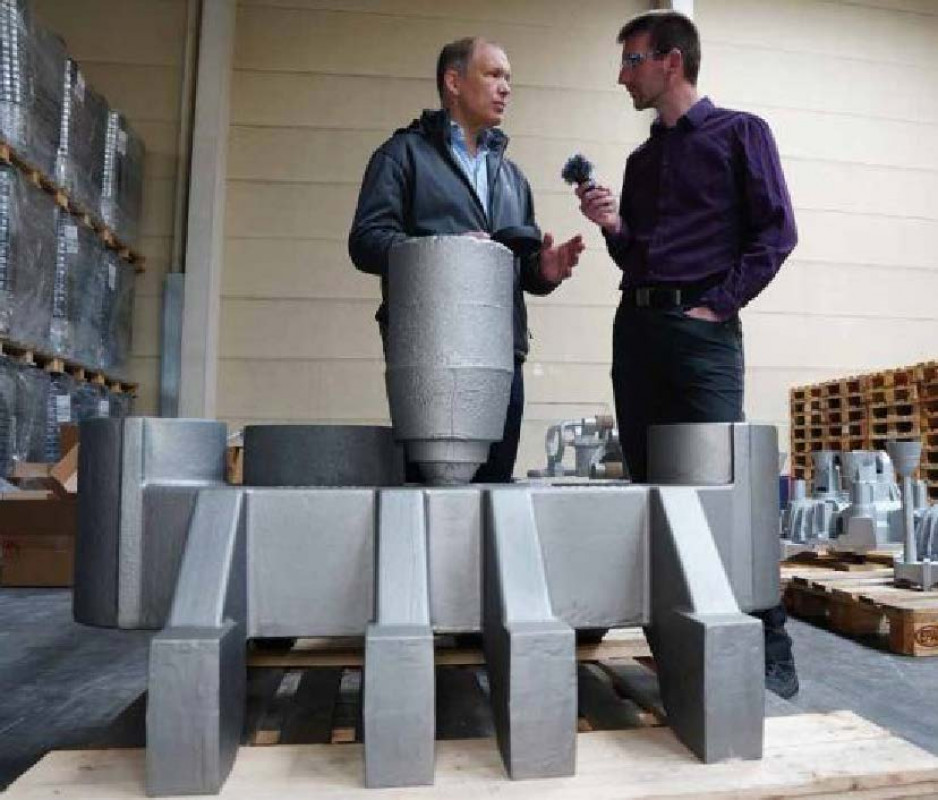
3-D printing allows greater freedom in filter structure, especially with regard to the pore size. This means that, among other things, higher casting weights are possible. In the future, this technology still has a lot of development potential, which we are currently working on. A look at the plan of the exhibition stand shows that Foseco has only shown a small part of the planned exhibition today. It will be interesting to see what else the manufacturer will present.