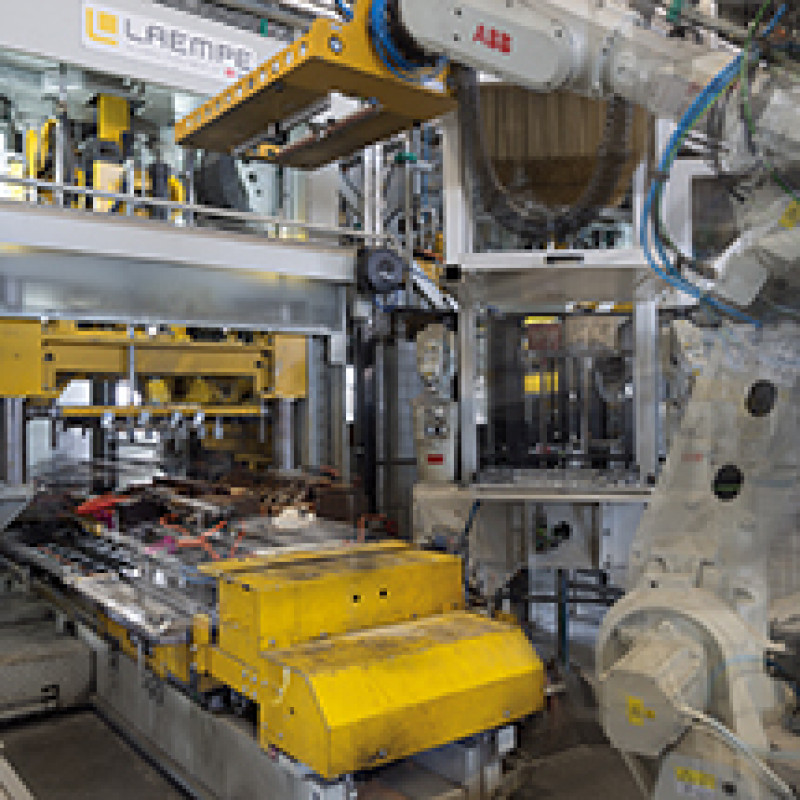
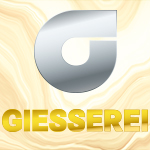
Sie soll eine Benchmark für die Branche in Sachen Digitalisierung, Vernetzung und Effizienz werden: die neue Kernmacherei Inacore, ein Joint-Venture von Laempe Mössner Sinto, Barleben, und der R. Scheuchl GmbH aus Ortenburg. Um in den kommenden Jahren über 1,5 Millionen Kernpakete für die Motorenproduktion der BMW-Leichtmetallgießerei in Landshut zu fertigen, begann die Produktion bereits vor einem Jahr – jetzt startete auch der Dreischichtbetrieb im niederbayerischen Ergoldsbach, um die Kapazität weiter zu erhöhen.
Bis zu zweitausend Fahrzeuge sollen bei BMW künftig pro Tag vom Band rollen, deren Zylinderkurbelgehäuse mithilfe von Inacore-Kernen gefertigt werden, hieß es bei der offiziellen Eröffnung des Werks Ende September 2018 in Ergoldsbach. Die BMW-Leichtmetallgießerei in Landshut setzt für die Fertigung von 4-Zylinder-Benzinmotoren der 3er- und 5er-Modelle bereits seit Anfang 2018 anorganisch gebundene Kerne von Inacore für die Gießformen ein. Finanziert wurde der Bau der hochmodernen Kernmacherei mit einem guten zweistelligen Millionenbetrag, den die Gesellschafter und Banken tragen.
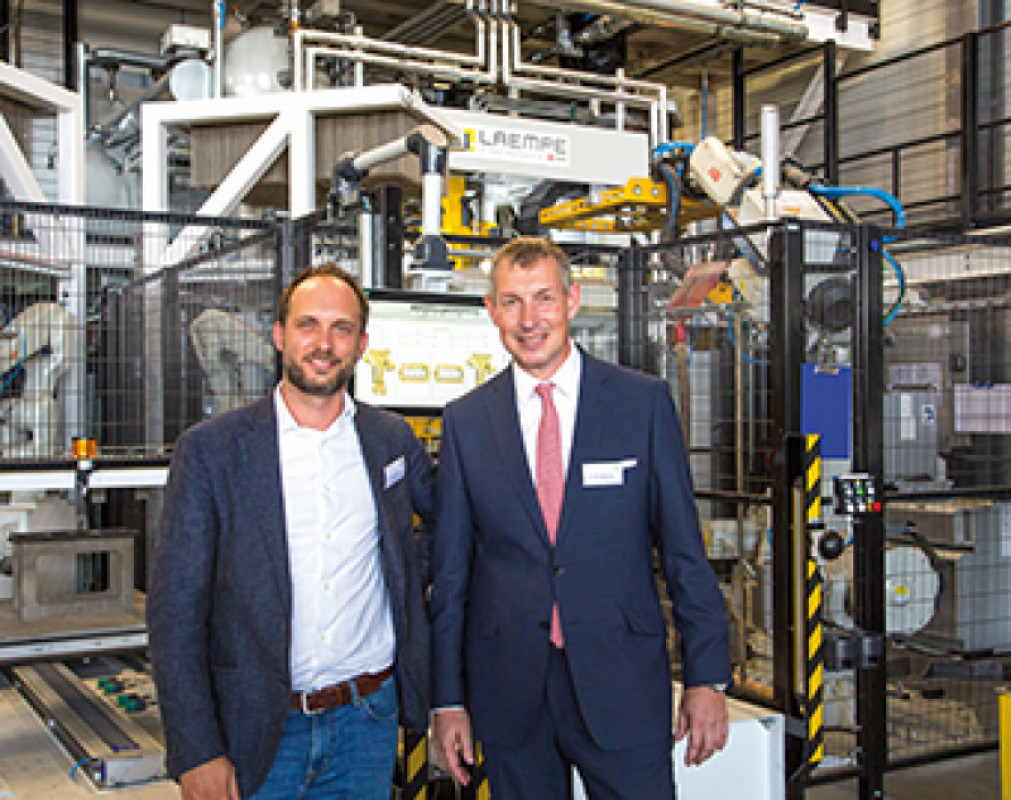
Knappes Zeitfenster für den Bau des Werks
Mit dem Baustart Mitte 2017 im Gewerbegebiet von Ergoldsbach startete der Countdown bis zum Produktionsanlauf. Der Plan sah vor, dass die Erstbemusterung Anfang Dezember 2017 und die Auslieferung erster Kerne bereits im Januar 2018 erfolgen sollte. Logistisch war der Standort gut gewählt. Bis zum BMW-Kernlager, für deren Versorgung mit Kernen Inacore verantwortlich zeichnet, sind es nur 19 Kilometer. Zudem ist Ergoldsbach eine Pendlerstadt mit wenigen eigenen Betrieben. Das neue, bislang einzige Industrieunternehmen vor Ort bot daher neue berufliche Perspektiven, die schnell ergriffen wurden. Zahlreiche Mitarbeiter unterschrieben ihre Verträge bei Inacore noch bevor die Kernmacherei ihre Arbeit überhaupt aufgenommen hatte – heute sind bei Inacore mehr als 30 Mitarbeiter beschäftigt. Die Verwaltung sowie die Forschung & Entwicklung für das neue Unternehmen sind bei den Joint-Venture-Partner Scheuchl und Laempe Mössner Sinto angesiedelt.
Hochautomatisierte und vernetzte Produktion
Um die Versorgung von BMW mit Kernpaketen zu je neun Einzelkernen sicherzustellen, sind sechs vollautomatisierte High-Tech-Kernschießmaschinen vom Typ LHL30 von Laempe Mössner Sinto im Einsatz. Mit den Maschinen werden u. a. Wassermantelkerne, Mittelkerne und Ausgleichswellenkerne geschossen. Werkzeugwechsel sind in wenigen Minuten möglich. Nach dem Schuss übernehmen Industrieroboter von ABB die Entgratung, bevor Mitarbeiter die finale Qualitätsprüfung der Kerne durchführen und sie in den mit RFID-Chips ausgestatteten Stellagen ablegen.
Die Stellagen – und damit die im RFID-Chip gespeicherten Produktionsparameter der Charge – werden damit zur Schnittstelle zwischen Fertigung, Klimalager und dem Kernlager im BMW-Werk. Die Produktionszyklen sowie die damit verbundenen Daten sind per Computer oder Tablet in Echtzeit abrufbar und können auch mit Altdaten abgeglichen werden. Eine Digitalisierung vom Feinsten, die die Inacore-Gesellschafter und Geschäftsführer Udo Dinglreiter und Andreas Mössner begeistert und zu kühnen Plänen anspornt: „Wir arbeiten gemeinsam mit dem Mathematik-Lehrstuhl der Universität Passau an einem mehrparametrigen System, das von einer künstlichen Intelligenz (KI) gesteuert wird. Hier stehen wir noch ganz am Anfang, unser Fernziel ist aber, dass die KI lernt, aus den Daten Schlüsse abzuleiten und Fehler letztlich irgendwann nicht mehr zuzulassen“, erklärt Udo Dinglreiter und Andreas Mössner ergänzt: „Die Maschinen- und Anlagenbauer müssen Industrie 4.0 selber in die Hand nehmen.“ Weitere technische Möglichkeiten wie Augmented Reality, also die computergestützte Erweiterung der Wahrnehmung, und der Einsatz von Virtual Reality könnten eines Tages für die Wartung und Instandhaltung zum Einsatz kommen.
Nach der Gründung des Gemeinschaftsunternehmens im April 2017 begann parallel zum Aufbau des Standorts im Gewerbegebiet von Ergoldsbach die Schulung der Mitarbeiter. Da das Personal über keinerlei spezifische Kernmacherei-Erfahrung verfügte, wurde es bei BMW einem Intensivtraining unterzogen. Für die Digitalisierung tat sich Laempe Mössner Sinto bereits im Januar 2017 mit dem Start-up pragmatic industries zusammen. Angesichts des kurzen Zeitfensters bis zum Produktionsanlauf verfuhren die Partner nach dem Prinzip „Learning by Doing“. Erklärtes Ziel war es, eine Kernmacherei als Benchmark der Branche zu errichten und dadurch versteckte Potenziale aufzudecken. Die Werkzeuge dafür sollten die Möglichkeiten konsequenter Digitalisierung mit den Säulen Transparenz, Vernetzung und Rückverfolgung bieten. „Es ist immer noch Neuland“, gesteht Andreas Mössner ein.
Doch neben dem technikgetriebenen Anspruch musste reichlich Know-how eingebracht werden. Scheuchl setzte seine langjährige Erfahrung beim Aufbau der Werksinfrastruktur, der Klimatechnik und beim Projektmanagement ein, Laempe bei den erforderlichen Maschinen – von den Kernschießanlagen, über die Sandmischer bis zur Sandfördertechnik. In zunächst zwei Hallen installierten die Partner die notwendigen Anlagen. Halle 1 beherbergt die Fertigung mit den sechs Kernschießmaschinen und den Manipulatoren. Halle 2 das Klimalager sowie die Server, die Rohstofflager und die beiden Sandsilos der Firma FAT aus Niederfischbach. Eine dritte Halle ist in Planung.
Bei so viel High-Tech, darf die IT-Sicherheit nicht außen vor gelassen werden, sonst drohen Gefahren von Cyberkriminellen durch Trojaner, Hacks oder Überlastungsangriffe. Für die Datensicherheit haben die Gesellschafter rund 100 000 Euro für die Server und eine doppelt gesicherte Sicherheitstechnik in die Hand genommen. Zuversichtlich in Sachen IT-Sicherheit macht Udo Dinglreiter und Andreas Mössner, dass die Daten nicht so leicht zu interpretieren sind.
Nachhaltige Klimatisierungstechnik
Knackpunkt bei der Fertigung von anorganischen Kernen ist die Klimatisierung, die über die Haltbarkeit und Funktionsfähigkeit der Kerne entscheidet. Hier wählten die beiden Familienunternehmen einen nachhaltigen Ansatz: Sie nutzen die Abwärme der Kompressoren für den Antrieb des Sorptionsrotors, der die Temperatur im Klimaraum regelt. „Die Kerne härten in der Kernschießmaschine aus, dann kommen sie in den Klimaraum, der durch Abwärme klimatisiert wird“, erläutert Udo Dinglreiter. Um den Transport vom Werk zum BMW-Lager mit einer Luftfeuchtigkeit von wenigen Gramm pro Kubikmeter sicherzustellen, arbeitet Inacore mit einer Spezialspedition zusammen, die die Kerne in luftdichten Lkws ausliefert.
Für die nachhaltige Klimatisierungstechnik entschieden sich die Partner Andreas Mössner zufolge nicht nur aus rein wirtschaftlichen Gesichtspunkten: „Jeder hat Kinder, daher ist Nachhaltigkeit die Leitplanke für unternehmerisches Leben. Wo man sie steuern kann, tut man es, wenn es wirtschaftlich ist: umso besser.“ In Ergoldsbach werden derzeit 2000 Kernpakete am Tag hergestellt, eines wiegt 15 Kilogramm. Insgesamt ist eine Sandmenge von 30 Tonnen täglich erforderlich – und die muss bewegt werden: von den Sandsilos über Sandsender zu den Sandmischern, die aufgrund der Infrastruktur der Halle extra so umgebaut werden mussten, dass sie auf dem Boden stehen können. Dann fließt der Sand über weitere Sandsender zu den Kernschießmaschinen in Halle 1. Der Füllstand der Silos soll künftig mit den Sandlieferanten vernetzt werden, um die Sandversorgung der Silos jederzeit sicherzustellen.
Nach dem Aushärten der Kerne in den Kernschießmaschinen gelangen die Kerne ins Klimalager, wo neun verschiedene Kerntypen mithilfe eines ERP-Systems eingelagert sind. Dabei wird auch das Know-how über die Lagerfähigkeit anorganischer Kerne eingesetzt und bei der Auswahl der Lagerplätze berücksichtigt. Bei Inacore wird das Lager wegen der sensiblen Klimatisierung aber nicht nur vom eigenen Team überwacht, es gibt auch eine Echtzeitvernetzung mit dem BMW-Lager – Transparenz auf beiden Seiten, die die Produktionssicherheit und Zusammenarbeit optimieren soll.
Großen Wert legten die Partner auch auf die Qualität: Über 200 000 Euro investierten sie in Equipment für die Qualitätssicherung. Dazu gehören eine Labor-Kernschießmaschine zur Ermittlung der Sandqualität, der Mischqualität und der Kernbruchfestigkeit sowie ein Zeiss-Messgerät, mit dem u. a. Messungen als Nachweis des Zulieferers für den Kunden durchgeführt werden. Im Labor wird auch die Sandkorngröße ermittelt und bestimmt. Die mittlere Korngröße bei Inacore beträgt 0,32 Mikrometer. Für die Feuchtigkeitsmessung steht darüber hinaus ein kleiner Ofen zur Verfügung.
Inacore soll Prozessverständnis erhöhen
Kurz vor dem Bemusterungstermin Anfang Dezember 2017 war es dann soweit: Die Produktion in Ergoldsbach konnte starten. 30 Kernpakete wurden pünktlich auf den Weg zu BMW geschickt, die dann auch die Anforderungen des Autobauers erfüllten. Der Schachzug war geglückt und aus den Maschinen- und Anlagenbauern R. Scheuchl GmbH und Laempe Mössner Sinto waren Kernmacher geworden. Denn die beiden Partner überschreiten bewusst die angestammten Geschäftsbereiche im Maschinen- und Anlagenbau, um Betreiberwissen zu erlangen. „Die Anforderungen sind gestiegen, heute ist Prozessverständnis gefragt. Wie will man Anlagen planen, ohne die Details zu verstehen?“, fragt Andreas Mössner und ergänzt: „Wir wollen das tägliche Doing verstehen und damit auch die Maschinen verbessern“.
Eine weitere Motivation hinter der Großinvestition von Laempe und Scheuchl war jedoch sicherlich auch der Auftrag von BMW. Das neue Unternehmen will sich allerdings nicht allein von einem OEM abhängig machen und so läuft derzeit auch die Akquise weiterer Kunden für die High-Tech-Kernmacherei. Der Blick in die Zukunft des neuen Unternehmens war allseits von Zuversicht geprägt, wie die Eröffnungsveranstaltung im September 2018 zeigte. Neben hochrangigen Personen aus Politik und Wirtschaft war auch der Gründer der R. Scheuchl GmbH anwesend. Schließlich wurde auf der Leinwand in der Produktionshalle auch das BMW-Team zugeschaltet. Die Männer in den BMW-Westen übten den Schulterschluss mit dem Inacore-Team – und feierten damit zugleich eine beispielhafte Zusammenarbeit zwischen Zulieferer und Kunde.
VON ROBERT PITEREK, DÜSSELDORF
Schlagworte
AnlagenbauDigitalisierungFertigungForschungIndustrie 4.0InstandhaltungNachhaltigkeitProduktionSicherheit