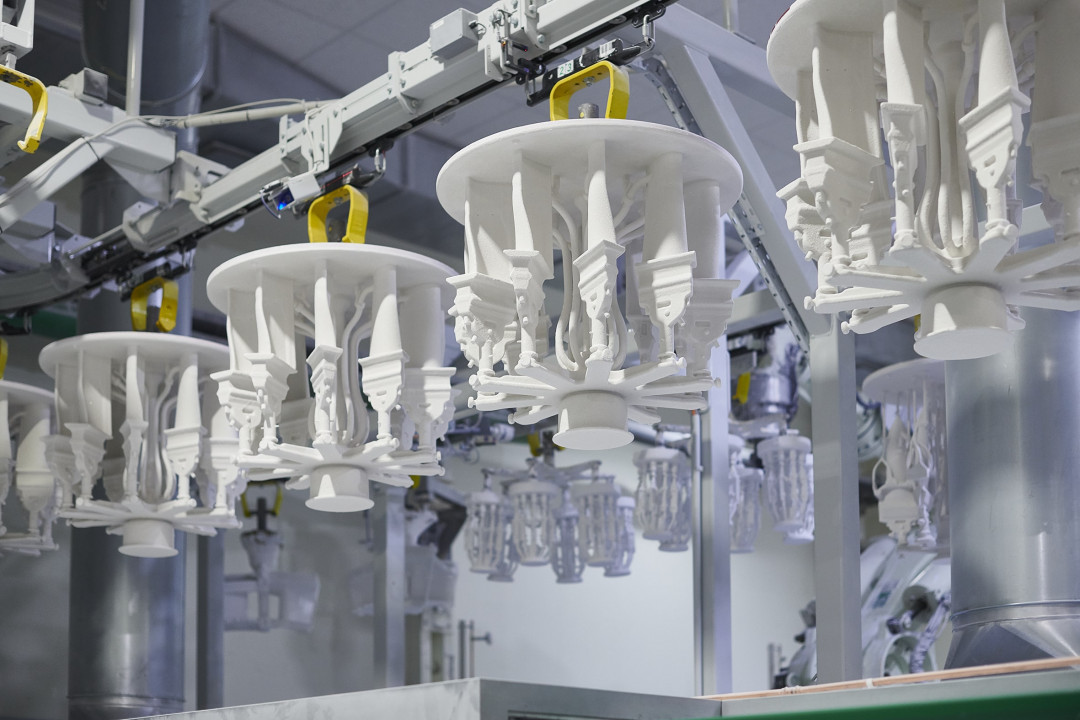
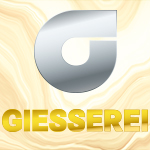
Per Funk zum drehbaren Robotergreifer - diese Art der Signalübertragung haben die Betriebstechniker der Bochumer Präzsionsgießerei Doncaster in Eigenregie realisiert. Dabei kommt ein Funksensor von Steute zum Einsatz: Er signalisiert den Betriebszustand des Greifers, der die Gusstrauben von einem Hängeförderer entnimmt. Ein Blick auf die Technik.
Von Gerald Scheffels
Ein Roboter entnimmt eine Gusstraube mit Wachsmodellen von einer Hängebahn, taucht sie in ein Becken mit einer weißen, zäh wirkenden Flüssigkeit auf Keramikbasis und bewegt die Traube so, dass die Flüssigkeit auch in Hinterschneidungen gelangt. Anschließend hält er die Traube in eine rotierende Trommel, wo sie "besandet" wird. Das heißt: Die noch feuchte Traube wird mit Sand umhüllt. Dieser Vorgang – zu dem auch die Trocknung der besandeten Keramikmasse in einer Trockenkammer gehört – wiederholt sich mehrfach. Ergebnis ist eine Keramikform, die das Wachsmodell umschließt und sich durch hohe Formstabilität auszeichnet. Aus dieser Form wird im weiteren Prozess das Wachs ausgeschmolzen, und das flüssige Metall kann, nach dem Brennen der Form, in den entstehenden Hohlraum eingefüllt werden.
Hoch komplexer Fertigungsprozess
So entstehen bei Doncasters Precision Castings in Bochum (DPC) die Gießformen von Lauf- und Leitschaufeln für stationäre Gasturbinenkraftwerke und für Flugzeugtriebwerke. Das ist nur einer von vielen Schritten des hochkomplexen Feingussprozesses, bei dem im Wachsausschmelzverfahren bis zu 80 cm lange Turbinenschaufeln erzeugt werden, die höchsten Ansprüchen standhalten: In Gasturbinen werden die Schaufeln mit bis zu 1400 °C heißem Gas angeströmt und erreichen Drehzahlen von 50 bis 60 Hz (Umdrehungen pro Sekunde). Unter diesen extremen Bedingungen erreichen sie – so die Anforderung der Turbinenhersteller – eine Standzeit von mindestens 10 000 Stunden.
Die Betriebstechniker von Doncasters verfügen über umfassendes Know-how nicht nur im Feinguss, sondern auch in der Produktionstechnik. Deshalb begab sich Guido Neef, Instandhaltungs-Experte im Bochumer Werk, zunächst auf eigene Recherche, nachdem es im eingangs beschriebenen Produktionsschritt der robotergestützten Formenherstellung Optimierungsbedarf gab – genauer gesagt an den Greifern der Roboter. Neef beschreibt den Prozess so: "Der Greifer nimmt die Gusstraube, die mit einer Hängeförderanlage von Station zu Station verfährt, von einem Gehänge ab. In das Rohr des Gehänges fährt pneumatisch ein Bolzen ein, um die pendelnd aufgehängten Gusstrauben zu fixieren – das ist die Voraussetzung für eine gezielte dreidimensionale Bewegung der Gusstraube in den Becken."
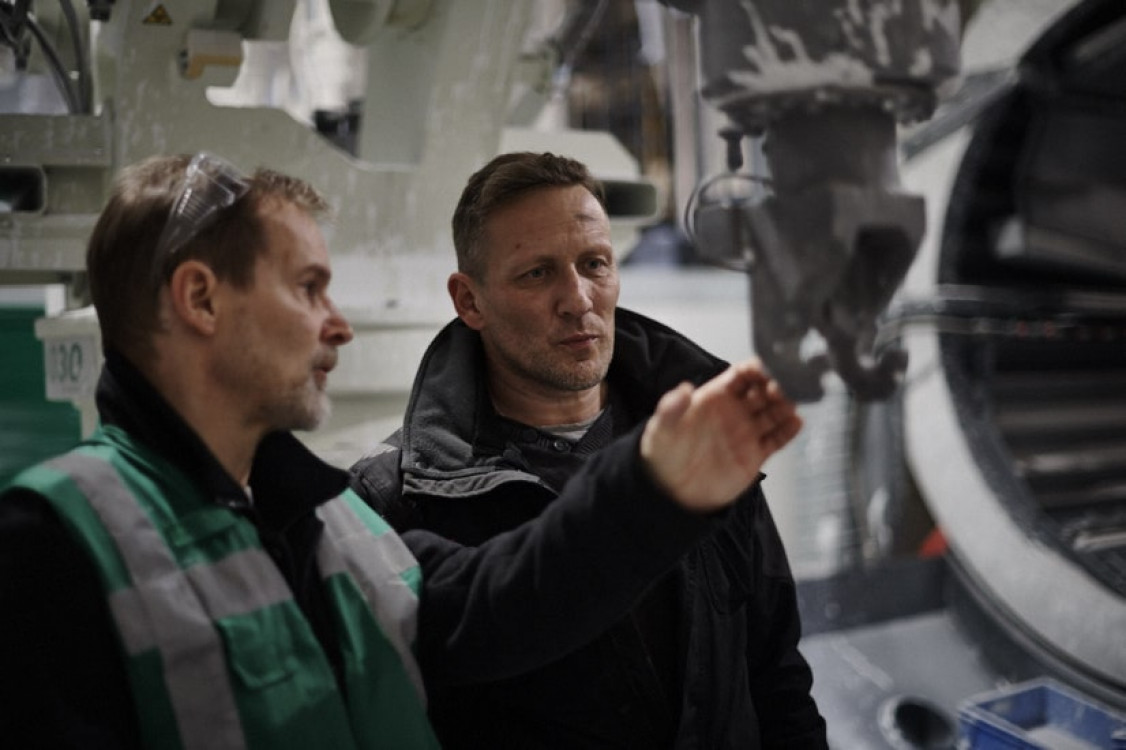
Gesucht: Lösung für die Positionsabfrage
Was den Betrachter erstaunt, ist die Vielfalt der Gusstrauben auf dem Hängeförderer. Die Varianz der Gussteile ist sehr groß, und jedes Bauteil verlangt nach anderen Bewegungsabläufen des Roboters bei der Formherstellung. Deshalb wird an jeder Roboterstation ein RFID-Code abgelesen, der das Teil identifiziert und das entsprechende Programm aufruft.
Optimierungsbedarf gab es hier, weil in einigen Fällen der Bolzen des Robotergreifers nicht in das Gehänge einfahren konnte. Das geschieht, wenn sich der Bolzen zum Beispiel verkantet oder nicht optimal positioniert ist. Die Anlage detektierte dann nicht, dass die vom Roboter geführte Gusstraube pendeln kann. Damit besteht das Risiko einer Kollision mit Anlagenkomponenten. Die Idee: ein Sensor, der detektiert, ob der Bolzen in das Rohr eingefahren ist. Eine solche Abfrage ist grundsätzlich einfach realisierbar, etwa mit einem Induktivsensor. In diesem Fall bestand die Herausforderung aber in der Energie- und Signalzuführung: "Weil der Greifer um 360 °C drehbar sein muss, lässt sich eine Stromversorgung unter den gegebenen Bedingungen schlecht realisieren. Deshalb fährt der Bolzen auch pneumatisch aus", erläutert Neef.
Gefunden: Induktiver Funksensor
Die logische Lösung: ein möglichst batteriebetriebener Sensor, der Signale per Funk sendet. Dann kann man weiterhin auf Leitungen bis zum Greiferkopf verzichten. Die intensive Recherche nach einem solchen Sensor führte Neef unter anderem auf die Homepage des Steute-Geschäftsbereichs "Controltec", der ein umfassendes Programm an industriegerechten Funkschaltgeräten und -sensoren bietet. Sie werden über eine Longlife-Batterie mit Energie versorgt und kommunizieren per Funk mit der zugehörigen Empfangseinheit, die bei größeren Anlagen in deren Schaltschrank untergebracht ist.
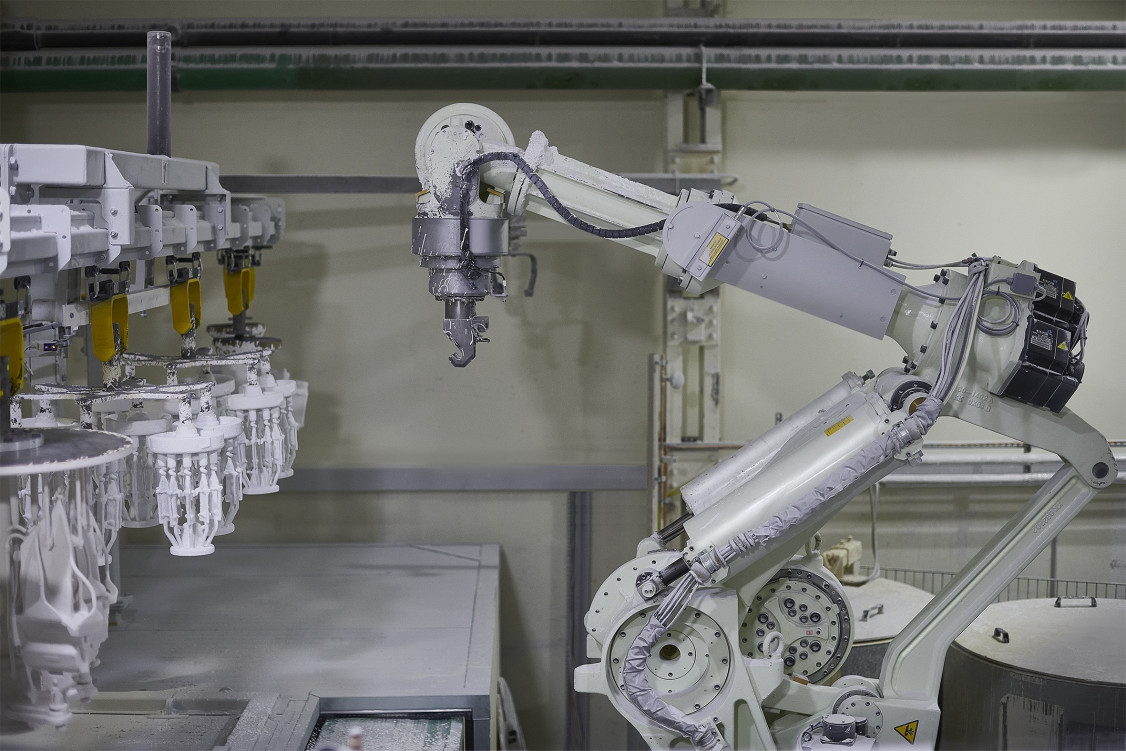
In Abstimmung mit Steute wurde ein Funk-Induktivsensor IS M 12 ausgewählt. Sowohl die Energieversorgung per Batterie als auch das Senden der Signale übernimmt ein separates, kompaktes Modul. Dabei kommt die von Steute entwickelte sWave-Funktechnik zum Einsatz, die auch unter ungünstigen Bedingungen im Industriebetrieb eine zuverlässige Signalübertragung gewährleistet.
Einen solchen Sensor installierte das Instandhaltungsteam von Doncasters zunächst testweise an einem Robotergreifer – und schützte dabei das separate Batteriemodul mit einer selbst gebauten Einhausung. Der Sensor sitzt im Greifer und detektiert zuverlässig, ob der Bolzen ausgefahren und somit die ansonsten pendelnde Verbindung zwischen Greifer und Gusstraube starr ist. Der Roboter startet nur, wenn der Sensor das Signal gibt. Dieses Signal wird von einer Empfangseinheit mit Antenne empfangen, die am einige Meter entfernten Steuerschrank der Anlage befestigt ist.
Risiken minimiert, Verfügbarkeit erhöht
Zugegeben: Es verlangt sehr hohe Kompetenz, als Anwender einer hoch automatisierten Anlage sowohl in die Mechanik (Installation des Funksensors in den Greifer) als auch in die Steuerungstechnik (Integration des Sensorsignals in die Robotersteuerung) einzugreifen. Das wird sich längst nicht jeder Fertigungsbetrieb zutrauen. Doncasters hat die Expertise, um diese anspruchsvolle Aufgabe anzugehen und umzusetzen. Das Ergebnis spricht für sich: Der kabellose Sensor mit der Punkt-zu-Punkt-Funkverbindung funktioniert auch in Grenzbereichen einwandfrei. Der Roboter startet nur dann, wenn der Bolzen vollständig in den Greifer eingefahren ist. Somit ist das Risiko einer Havarie oder Beschädigung sowohl der Anlage als auch der Gießformen ausgeschlossen. Die Konsequenz, laut Neef: "Von den fünf Robotern in der Formenproduktion haben wir schon drei mit den Funksensoren ausgerüstet, die anderen beiden werden folgen."
Gerald Scheffels ist Fachjournalist aus Wuppertal.
Beitragsbild: Udo Kowalski/Steute