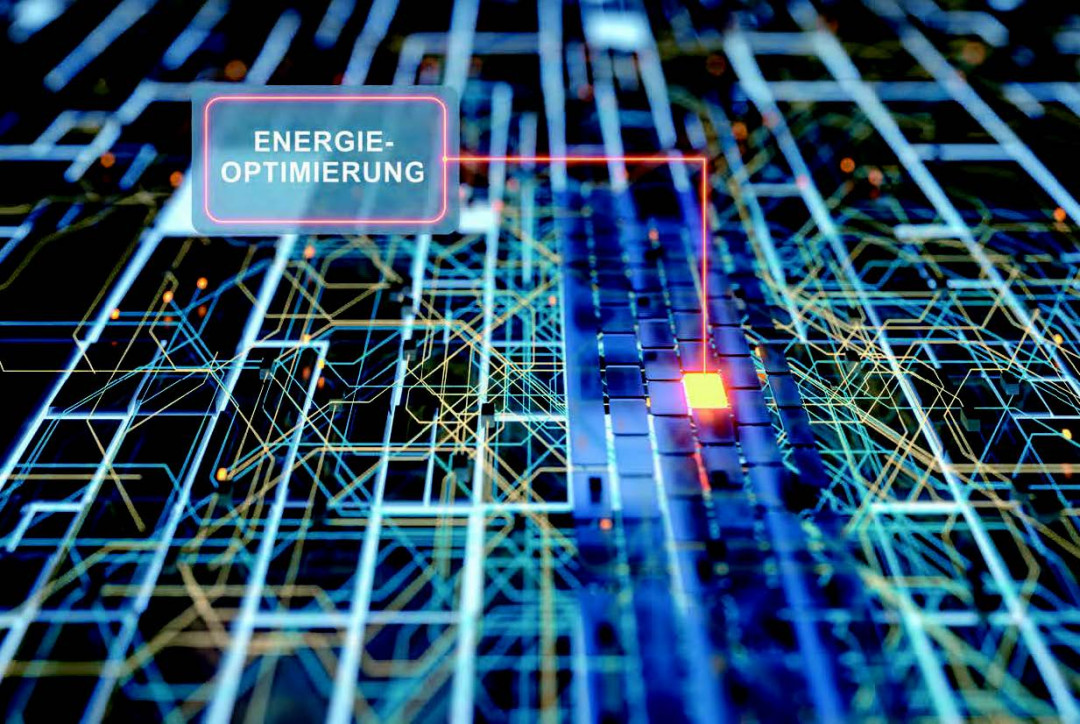
Neben den Personalkosten sind in Gießereien die Energiekosten in der Regel der zweithöchste Kostentreiber im Prozess. Daher mussten Gießereien in einem hart umkämpften Markt schon immer ihre Energiekosten optimieren. Die aktuellen Krisen, aber auch die langfristigen Veränderungen aufgrund des Ziels der Klimaneutralität sind durch die stark steigenden Energiekosten existenzbedrohend. Daher versuchen die Betriebe alles, um ihre Energiekosten weiter zu senken, hier vorgestellt am Beispiel von G.A.Röders.
Von Klaus Dilger, Norbert Hoffmann, Olgierd Lemanski, Gerd Röders
Die Firma G.A.Röders in Soltau ist eine über 200 Jahre alte Gießerei und seit vielen Jahren in der Forschung aktiv. Zusammen mit weiteren Gießereien und Zulieferern der Gießerei-Industrie wird in Soltau das Leichtmetallzentrum der Universität Braunschweig betrieben. Ein Schwerpunkt dieser Kooperation ist es, ein methodisches Energiemanagementsystem zu etablieren. Im Folgenden sollen aktuelle und bereits umgesetzte Methoden beschrieben werden, die zu erheblichen Einsparmöglichkeiten geführt haben.
Erster Schritt: die Analyse
In einer Arbeit im Rahmen des Forschungsvorhabens „Progress“ analysierte die Firma Bühler den sehr unterschiedlichen Energieverbrauch von Gießereien je Kilogramm guter Guss. Dabei unterscheiden sich die befragten Betriebe außerordentlich. Dieser Unterschied ist nicht nur auf unterschiedliche Infrastruktur und Arbeitsweise, sondern auch auf Maschinengrößen, Losgrößen und Art der Schmelzanlagen zurückzuführen. Insofern gibt es keine eindeutige Vergleichbarkeit zwischen den Gießereien, die zu einer Art Rangliste führen würde. Im Gegenteil ist jeder Betrieb dazu aufgerufen, sich selbst zu verbessern. Grundsätzlich kann aber festgehalten werden, dass beim Gasverbrauch über alle Gießereien hinweg etwa zwischen 15 und 40 % für die Infrastruktur und 60 bis 85 % für den Prozess verbraucht wurden. Beim Strom sind es 40 bis 50 % für den Prozess und 50 bis 60 % für die Infrastruktur (Bild 1).
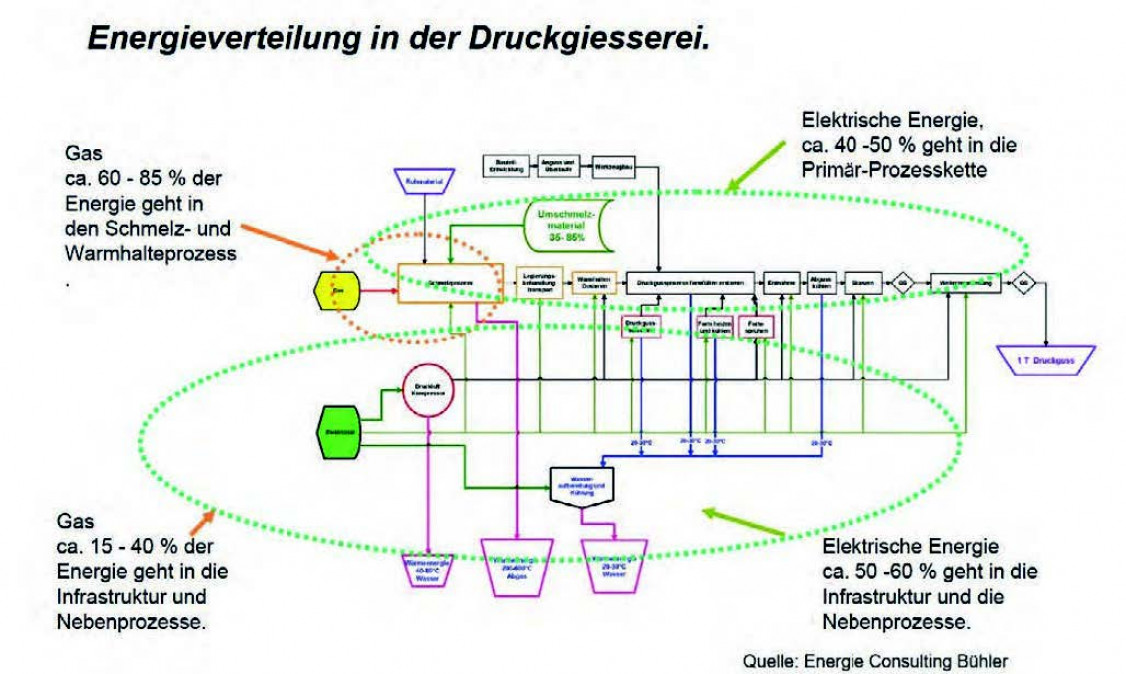
Für G.A.Röders wurde die Energieverteilung nach Abteilungen und Energieart vorgenommen. Der größte Anteil war zunächst bei Beginn der Arbeiten der Gasbedarf und dieser besonders in der Gießerei (Bild 2a, b).
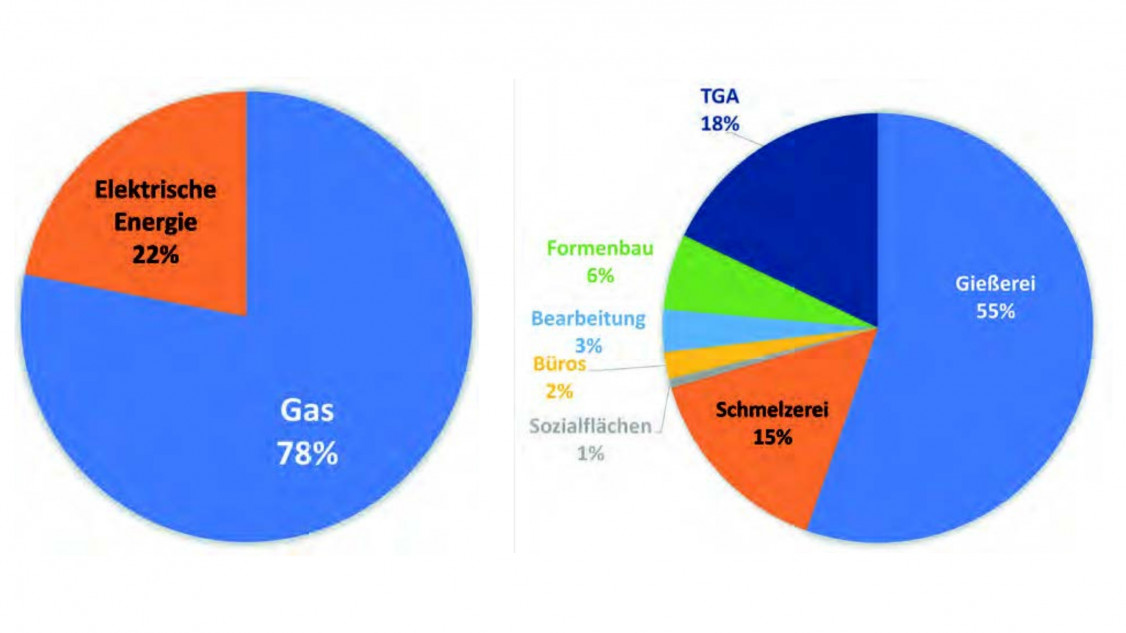
Eine genauere Analyse zeigt neben der Energiefluss der Energieträger Gas und Strom bei Röders auch den Wasserverbrauch an (Bild 3). Hier zeigte Florian Korten in seiner Arbeit welche Energieverbraucher welche Energieträger nutzten und in welcher Form die Energie umgewandelt wurde.
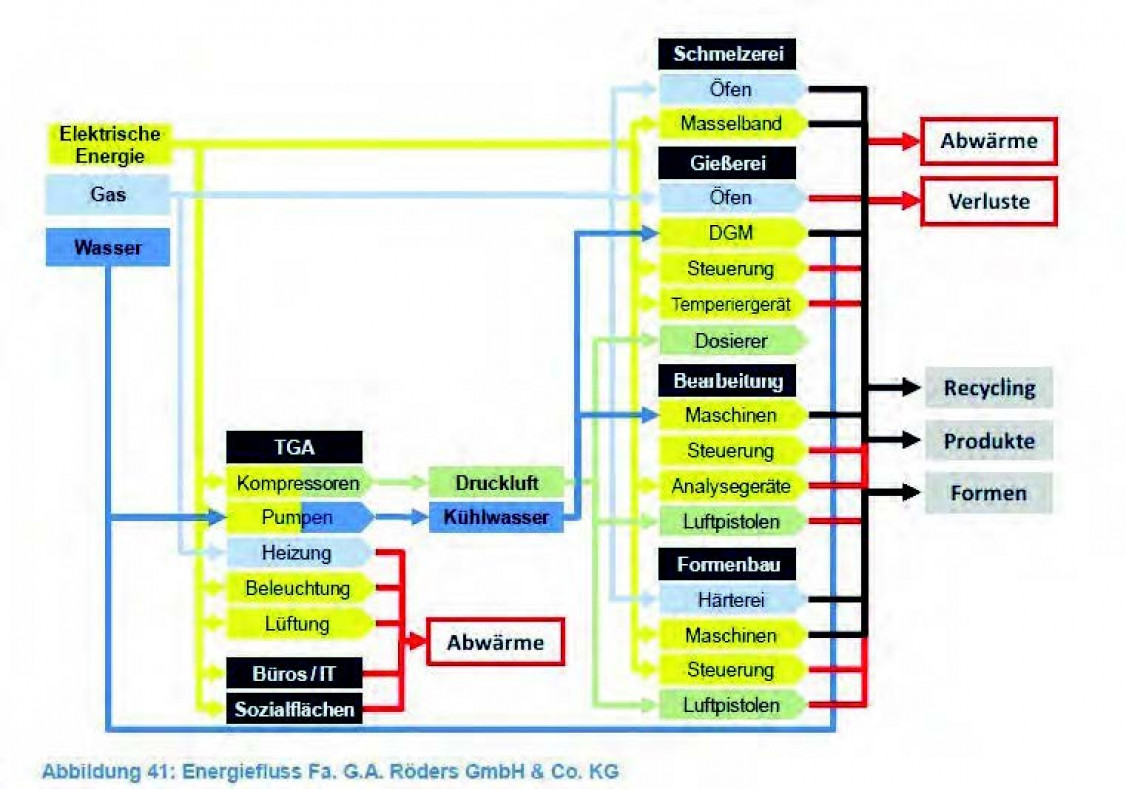
Wichtig dabei ist es, einen möglichst geringen Energieverlust in Form von Abwärme zu erzeugen.
Maßnahmen
Durch einen gewichteten Energiefluss konnten erste mögliche Schwerpunkte für eine Optimierung bestimmt werden. Dabei sind insbesondere die hohen Verbräuche von Gas an den Warmhalteöfen aufgefallen (Bild 4). Diese stellten ein besonderes Problem der Firma G.A.Röders dar. Als Spezialist für Gussprodukte mit hohen Anforderungen bei vergleichsweise kleinen Serien vergießt Röders zwölf verschiedene Legierungen und rüstet fast jede Maschine täglich. Deswegen wurden die Prozesse in der Schmelzerei von denen der Gießerei getrennt. Rücklaufmaterial wurde in der Schmelzerei geschmolzen und verblockt und anschließend an der Gießmaschine erneut geschmolzen und vergossen. Insofern wurde das gesamte Rücklaufmaterial jeweils doppelt geschmolzen, was zu erheblich höherem Energiebedarf führte.
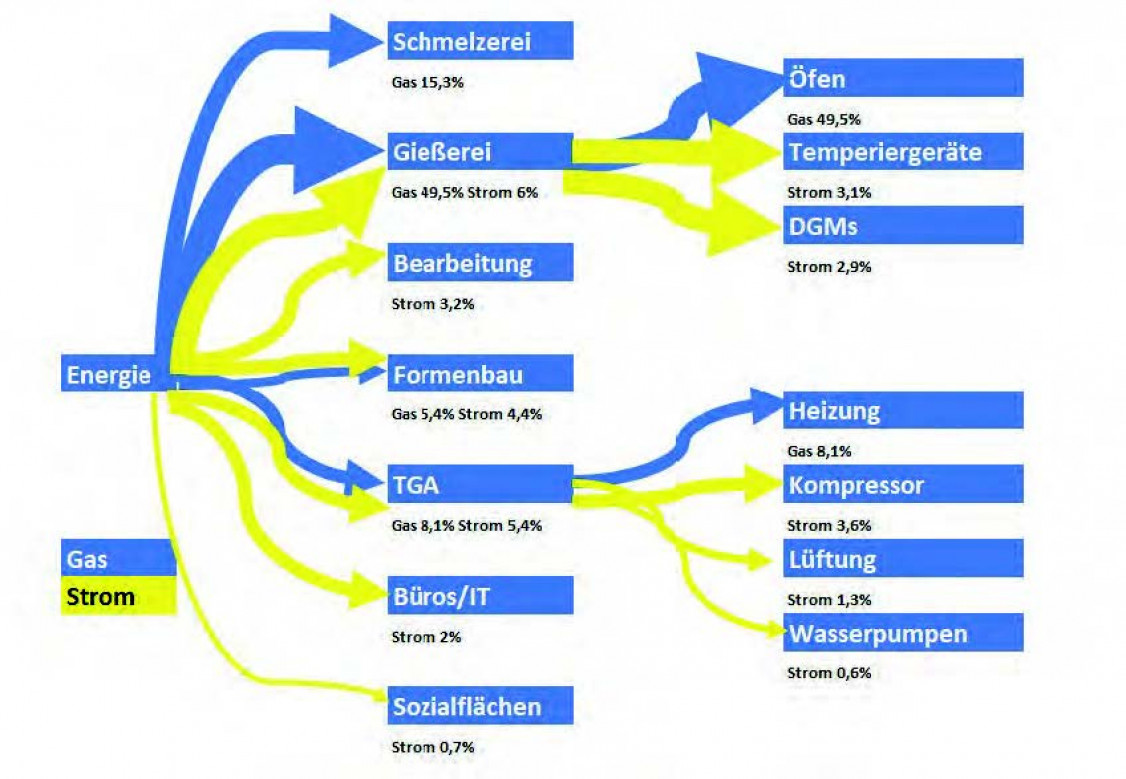
Im nächsten Schritt wurde eine Analyse der einzelnen Fertigungsmaschinen erstellt. Wichtig hierbei waren neben der Anschlussleistung auch die Laufzeiten der Maschinen. Maschinen mit geringer Laufzeit und niedrigen Anschlusswerten wurden im Fortgang zunächst nicht weiter betrachtet. Maschinen mit hohem Anschlusswert aber geringer Laufzeit müssen so eingesetzt werden, dass die Gesamtstrombelastung geringer wird. Hierfür eigenen sich zum Beispiel die Spät- oder Nachtschicht. Maschinen mit hohen Laufzeiten und geringer Anschlussleistung werden daraufhin untersucht ob Einsparungen möglich sind. Das größte Potenzial bieten jedoch die Maschinen mit hoher Laufzeit und hohem Anschlusswert (Bild 5).
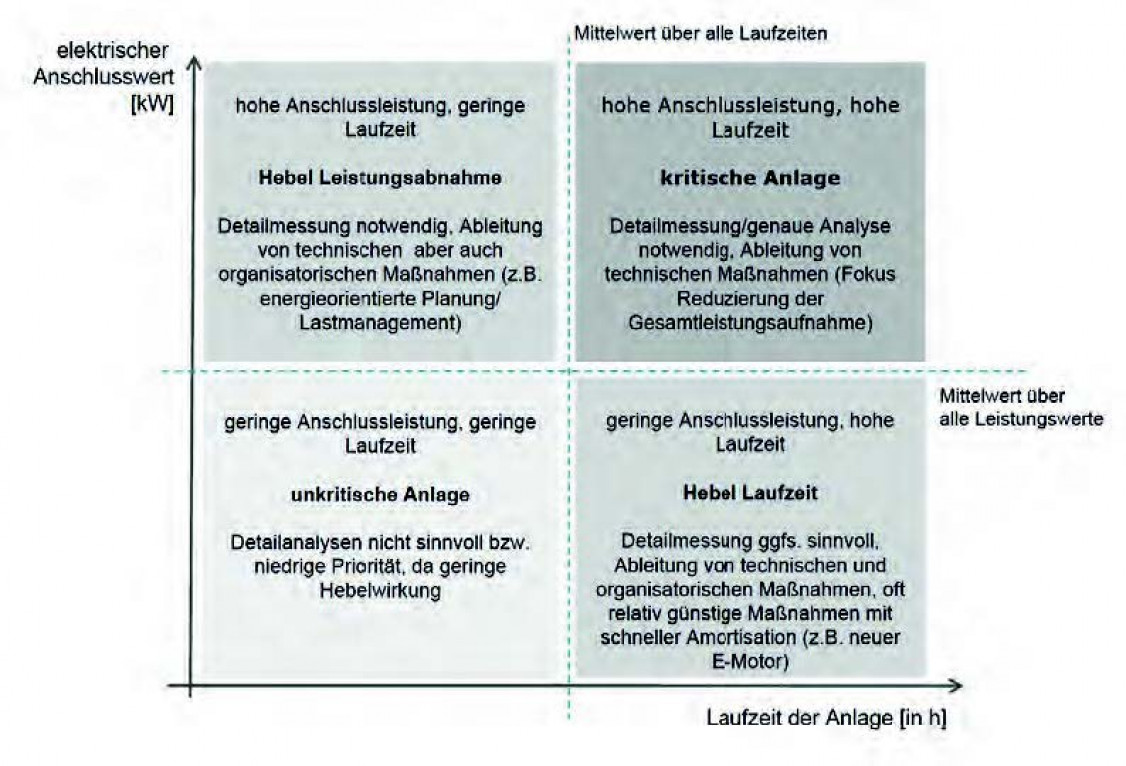
Sofern es sich bei den Messungen um ganze Maschinengruppen wie z.B. eine Gießzelle handelte, wurden diese in „Setcards“ zerlegt (Bild 6). Aktuell sind viele solcher Maschinen über intelligente Stromleser in der Stromverteilung transparent angeschlossen. Erwartungsgemäß waren die Kompressoren die größten Stromverbraucher, danach kamen die Druckgussmaschinen und Bearbeitungszentren. Und beim Gasverbrauch natürlich die Schmelzerei und Warmhalteöfen.
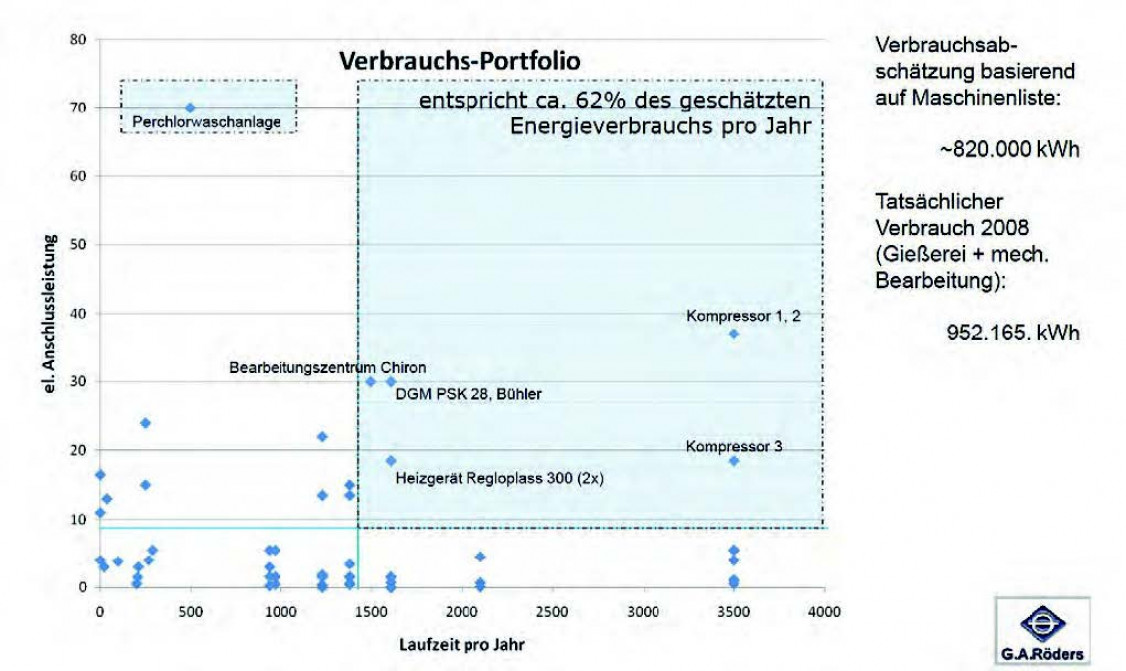
Verbesserungsvorschläge
Anschließend wurden in mehreren Workshops Verbesserungsvorschläge für die kritischen Anlagen erarbeitet. Dabei sind jedoch neben der energetischen Verbesserung auch andere Ziele der Firma zu betrachten. Diese sind insbesondere die Kundenbedürfnisse nach Flexibilität und geringen Stückzahlen sowie die hohen Lohnkosten. Mithilfe einer Nutzwertanalyse wurden deswegen alle möglichen Verbesserungen bewertet. Neben den Energieeinsparungen werden auch die Energiekosteneinsparungen betrachtet. Die Ergebnisse der Nutzwertanalyse sind dynamisch und müssen bei veränderten Parametern wie z.B. gestiegenen Energiepreisen erneuert werden. Dies ist dann jedoch mit minimalem Aufwand möglich. Aus der Nutzwertanalyse ergeben sich nun die tatsächlichen Verbesserungspotenziale.
Ergänzend zur Nutzwertanalyse (Tabelle 1) wurde ebenfalls ein komplettes Fabrikkonzept entworfen, um die Potenziale durch einen Neubau zu ermitteln. Im Nutzwert wurden diese insbesondere für die Kunststoffabteilung und den Werkzeugbau identifiziert und anschließend umgesetzt. Die neue Fabrikhalle arbeitet energetisch optimal und nutzt Restwärme etc. aus. Das Dach ist mit moderner Fotovoltaik bestückt und erzeugt eigenen Strom.
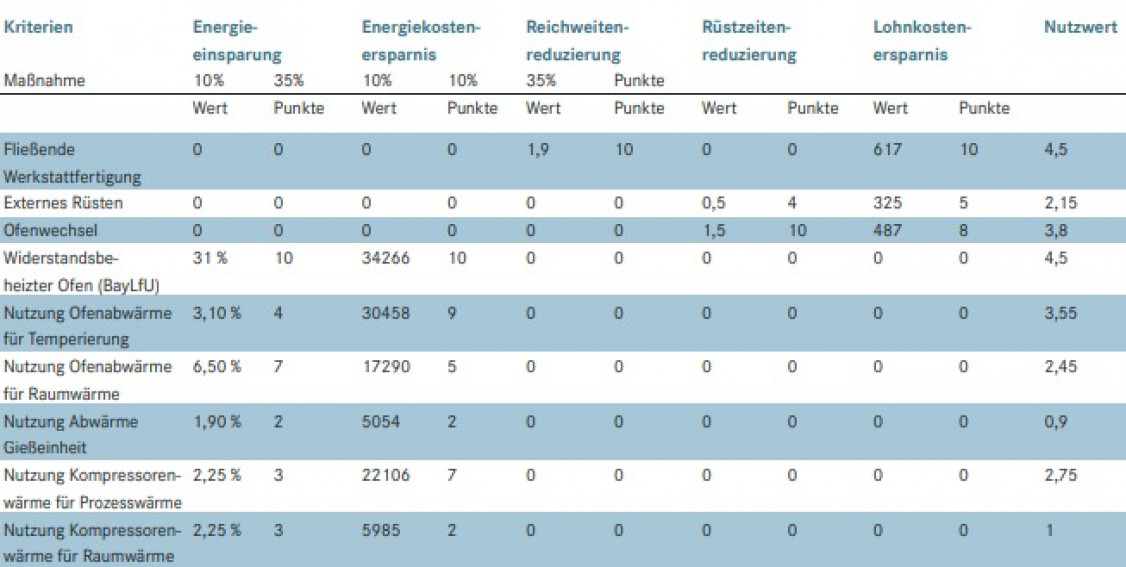
Ergebnisse
Als Ergebnis der Analyse wurden alle Öfen in der Gießerei ausgewechselt. Die neuen direkt geheizten Öfen haben einen wesentlich höheren Wirkungsgrad und können flüssig beschickt werden. Dadurch entfällt das Verblocken in der Schmelzerei. Gleichfalls konnte die Rüstzeit deutlich verringert werden bei gleichzeitig verbesserter Metallqualität. Weiterhin wurde die Einsatzzeit im Tiegelofen optimiert. Die Schmelzerei wurde vom Zweischicht- in den Dreischichtbetrieb übernommen, da die Warmhalteöfen flüssig beschickt werden. Dadurch wurde der Gasverbrauch weiter deutlich reduziert (Bild 7).
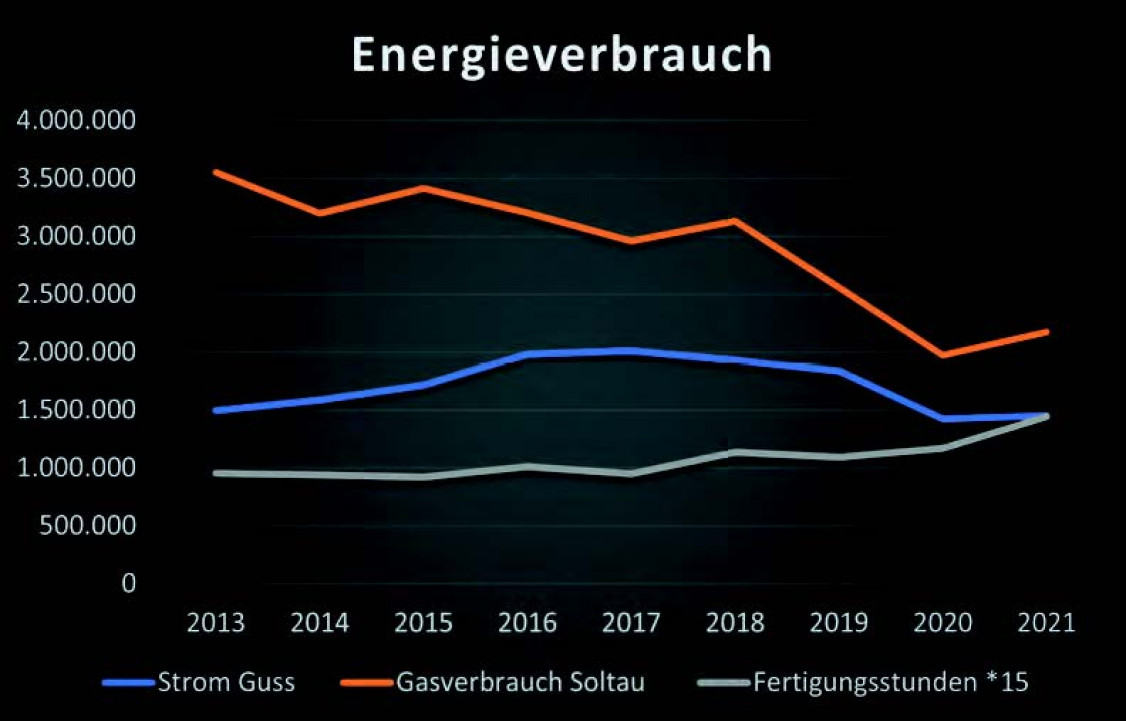
Die Kompressoren wurden teilweise erneuert, die Steuerung an das jeweilige Schichtmodell angepasst und die Abwärme zur Hallenheizung genutzt. Der Gießprozess wurde überarbeitet. Erhebliche Einsparpotenziale ergeben sich durch eine optimierte Temperaturführung im gesamten Prozess. Veränderungen beim Rüsten und bei Störungen der Maschine führen zu ganz erheblichen Einsparungen beim Energieverbrauch ohne negative Nebeneffekte Komponenten mit hohem Energiebedarf werden in solchen Fällen abgestellt, die Störzeiten durch schnelleres Eingreifen reduziert. Mit regelmäßigen Workshops zum Rüsten wird auch die Rüstzeit deutlich verkürzt. Die Absaugungen an den Maschinen wurden optimiert; die aktuellen Anlagen saugen nur dort die Luft ab wo die Verunreinigung entsteht. Dadurch können wesentlich kleinere Lüfter zum Einsatz kommen. Rekuperationsanlagen wurden eingebaut, lohnen sich jedoch erst bei weiter steigenden Energiepreisen. Erhebliche Änderungen wurden auch am Produkt vorgenommen, als Beispiel sei ein Angusssystem genannt: Das neue System benötigt 40 % weniger Material bei gleicher Qualität der Bauteile (Bild 8). Ergebnis sind nicht nur eine beträchtlich geringere Schmelzleistung, sondern auch geringere Gießzeiten. Zusammen mit den Kunden lassen sich hier weitere erhebliche Potenziale nutzen – auch in der Konstruktion der Teile unter energetischen Gesichtspunkten. Ein nicht zu vernachlässigender Aspekt ist die Reduzierung des Ausschusses. Bühler hat hier eine Abhängigkeit des Energieverbrauchs zur OEE deutlich gemacht.
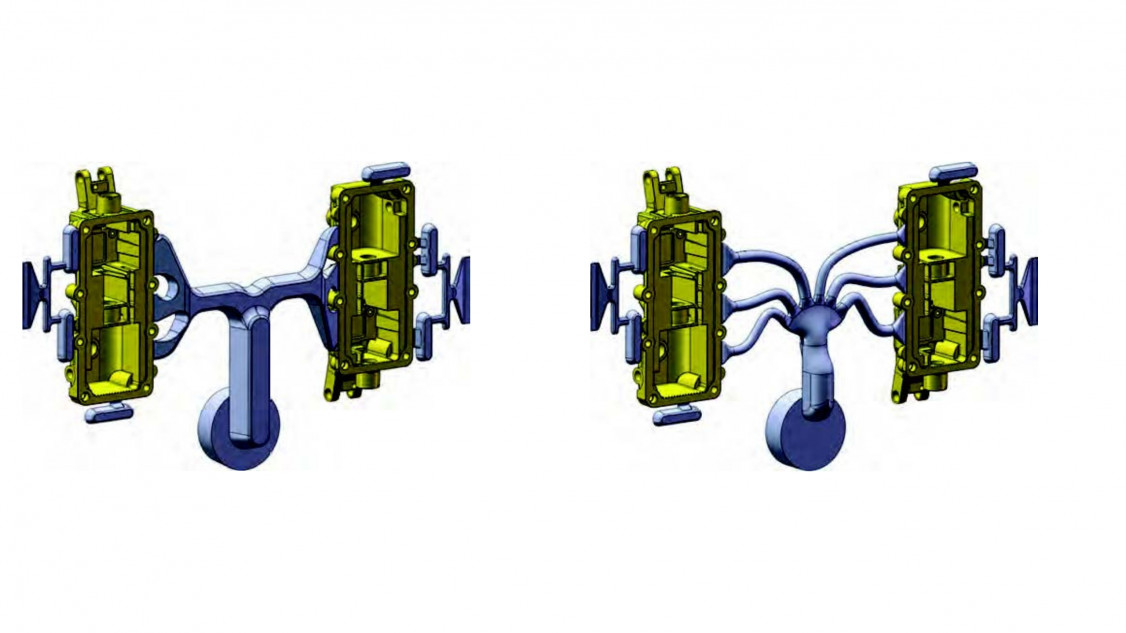
Fazit
Die hier beschriebenen Maßnahmen sollen nur ansatzweise zeigen, dass auch bei scheinbar optimierten Betrieben immer noch Energieeinsparungen in vielfältiger Weise möglich sind. G.A.Röders hat auf diesen Erfahrungen aufbauend ein Energiemanagementsystem entwickelt und ist seit einigen Jahren nach der DIN 50001 zertifiziert. Der CO2-Fußabdruck der Produkte konnte damit signifikant verbessert werden. Die Einsparungen ermöglichten es ebenfalls, seit einigen Jahren ausschließlich Ökostrom zu beziehen und für das Gas eine freiwillige Ausgleichsabgabe zu leisten. Aktuell werden im Forschungsverbund weitere Energieeinsparpotenziale entwickelt und über alternative Energieträger wie Wasserstoff nachgedacht. Das Ergebnis ist ein eigener, auf diese Firma zugeschnittener Pfad, den die Mitarbeiter mittragen. Exemplarisch ist jedoch das methodische Vorgehen beim Energiesparen über alle Prozesse hinweg. Nur im intelligenten Zusammenspiel vieler Einzelmaßnahmen entstehen so energetisch sinnvolle und wettbewerbsrelevante Prozesse.
Prof. Dr.-Ing. Klaus Dilger, TU Braunschweig, Institut für Füge- und Schweißtechnik, Dr. Norbert Hoffmann, Fördergemeinschaft Druckgießforschung, TU Braunschweig, Olgierd Lemanski, Technische Betriebsleitung, G.A.Röders, Gerd Röders, Leichtmetallzentrum Soltau
Literatur
[1] Herrmann, Pries, Hartmann: Energie- und ressourceneffiziente Produktion von Aluminiumdruckguss Springer-Verlag Berlin 2013
[2] Korten: Entwicklung eines energieverbrauchsreduzierten Fabrikkonzeptes für eine Aluminium-Druckgießerei 2011 Diplomarbeit am ifS Braunschweig bei G.A.Röders
[3] Reichen: internationaler deutscher Druckgusstag 2015 Vortrag
[4] Meyer: Prozesskettenbenchmark für Produktfamilien im Aluminiumdruckguss unter Berücksichtigung von Energie- und Ressourcenverbrauch sowie Flexibilität der Produktion Studienarbeit Markus Meyer am ifs Braunschweig bei G.A.Röders
[5] Kerber: Aktuelle und zukünftige Herausforderungen für Druckgießereien Ressourceneffizienz, Flexibilität und steigender Wettbewerbsdruck Vortrag internationaler Druckgusstag 2013
[6] Stephan, Zizmann u.a.: Effiziente Energienutzung in Nicht-Eisen-Schmlezbetrieben, Bayrisches Landesamt für Umweltschutz Augsburg 2015
Schlagworte
AbsaugungAluminiumDruckgussDruckgussmaschinenEisenFertigungForschungFotoGießereiGussKonstruktionProduktionSchmelzanlagenSchmelzereiVerlagWerkzeugbau