
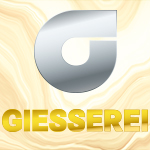
Abstract
Lesen Sie einen Fachartikel aus der GIESSEREI 03/2018. Der Artikel beschreibt, wie mit einfachen Methoden der Digitalisierung in der Fertigung einer Eisengießerei im Handformbetrieb die Grundlagen für eine energie- und ressourcenschonende Prozessregelung geschaffen wurden. Diese Entwicklung wird im Rahmen des von der Deutschen Bundesstiftung Umwelt geförderten Projektes „IEREGUSS“ von der Hochschule Kempten und der Kemptener Eisengießerei Adam Hönig AG durchgeführt. Dabei müssen zunächst Verfahren der Digitalisierung und Erfassung von energierelevanten Prozessdaten und Energieverbrauchsdaten eingeführt werden. Um die Daten nutzbringend zur Verfügung zu stellen, müssen diese mit den anderen betrieblichen IT-Systemen verknüpft und in einer zentralen Datenbank bereitgestellt werden. In weiteren Schritten sind die gesammelten Daten auszuwerten. Dafür eignen sich mathematisch-statistische Methoden, aber auch maschinelle Lernverfahren. Aus den Auswertungen und Ergebnissen resultieren Prozessmodelle und Handlungsanweisungen, in Form von optimierten Steuersignalen, die in die einzelnen Betriebsbereiche eingebracht werden. Entscheidend ist die mit diesem Verfahren mögliche adaptive Prozessführung, das heißt, dass der Nutzen aus den optimierten Steuersignalen wieder neu bewertet wird. Dadurch wird eine kontinuierliche Prozessoptimierung möglich. Zudem können die einzelnen Schritte im Produktherstellungsprozess visualisiert an Panels dargestellt werden. Das schafft eine erhöhte Transparenz, welche eine optimierte Planung der Produktion erlaubt. Daneben unterstützt die Anwendung auch die Abschaffung einer unnötigen „Zettelwirtschaft“ im Unternehmen. Im Folgenden wird das Prinzip der IT-gestützten Prozessoptimierung erörtert, von der Datenaufnahme, zur Datenhaltung, über die Datenauswertung und Visualisierung und deckt zum Ende die versteckten potentiale einer Gießerei auf.
VON STEFAN GRIMM UND DIERK HARTMANN, KEMPTEN
In vielen Branchen wird immer häufiger von einer transparenten Produktion berichtet. Darunter versteht man die lückenlose Rückverfolgung der einzelnen Gussteile über die gesamte Wertschöpfungskette. Dabei werden die anfallenden Prozessdaten auf die einzelnen Teile gemünzt. Dies ermöglicht neben dem Eruieren von Potentialfeldern für Prozessoptimierungen auch die Einsparung von bisher ungeachteten Ressourcen. Dabei ist von Zeit, Energie und Material die Rede. Jedoch ist eine digitale Datenaufnahme bis hin zu einer lückenlosen Rückverfolgung in Gießereien keine triviale Aufgabe, da der Produktionsprozess vom flüssigen Eisen bis zur Entstehung des Gussprodukts sehr viele händische Arbeitsschritte beinhaltet. Des Weiteren sind die einzelnen Teilprozesse, wie zum Beispiel die Kernherstellung, das Formen, das Gießen oder das Auspacken, nicht oder nur lückenhaft untereinander vernetzt. Das bedeutet, dass der Informationsfluss darüber, ab welchem Zeitpunkt ein neuer Teilprozess starten kann, nur „über Zuruf“ erfolgt. Eine IT-Unterstützung ist bislang kaum gegeben. Zur Umsetzung einer Vernetzung und Digitalisierung der einzelnen Insellösungen müssen für jeden Bereich eigene Konzepte zur Datenerfassung entwickelt werden, unter Betrachtung der unterschiedlichen Störfaktoren wie Hitze, Staub und Magnetfelder. Aus diesem Grund ist eine vollständige Rückverfolgung nur durch Einsatz individueller Markierungstechniken und der schnellen und effektiven Prozessdatenerfassung möglich. Diese verschiedenen Ansätze zur Identifikation werden unter dem Sammelbegriff AutoID verstanden. Dazu zählen optisch auslesbare Codes, wie zum Beispiel Barcode, Data-Matrix-Code oder andere Marker-Technologien wie RFID, die elektromagnetische Wellen zur Übertragung nutzen [1].
Durch eine logistische Überwachung der Produktionsprozesse und -abläufe können Daten aufgenommen werden, woraus sich Standzeiten, Durchlaufzeiten und Prozesszeiten ermitteln und als zeitliche Abfolge darstellen lassen (Bild 1).
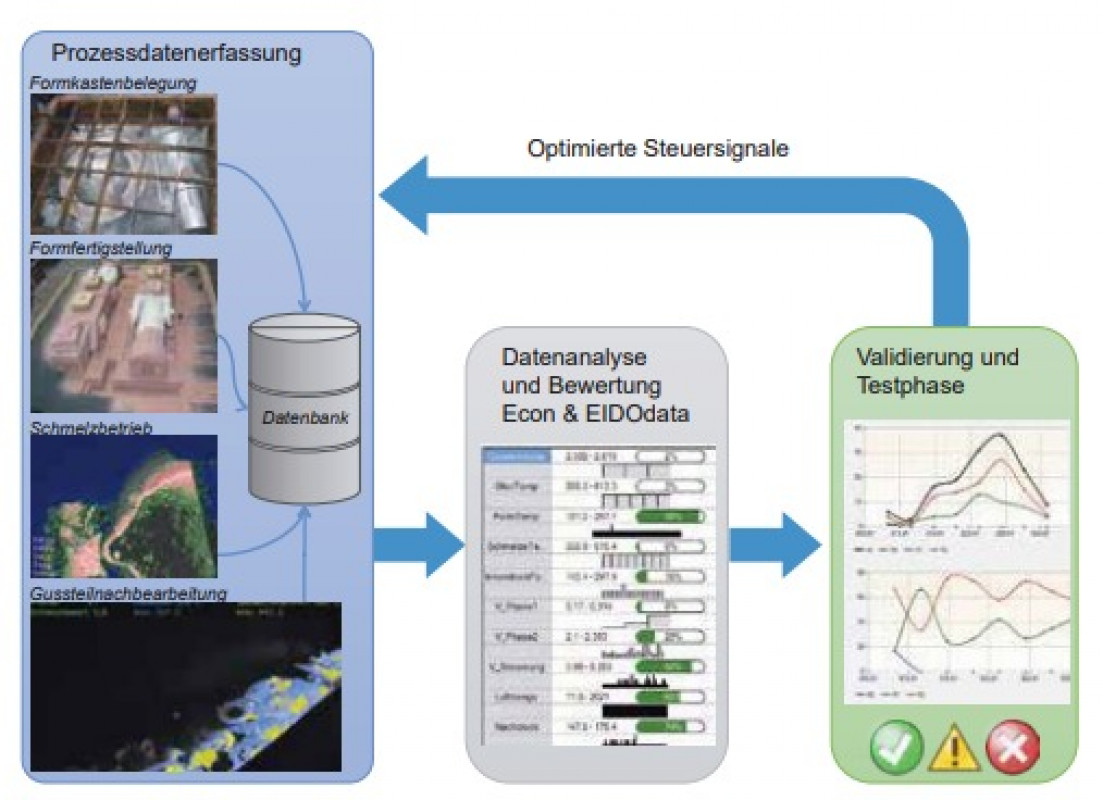
Eine visualisierte Darstellung deckt schnell und übersichtlich zeitintensive Prozesse und Bottle-Necks sowie Potentiale, etwa die Auslastung einzelner Maschinen oder Produktionsbereiche, auf. Bild 2 zeigt exemplarisch die Auslastung der vollautomatischen Formanlage. Dabei wird die Anzahl der gepressten Formballen aufgenommen und die Auslastung über einen Arbeitstag grafisch dargestellt. Um eine bessere Auslastung der Maschine zu erreichen, fehlen noch weitere Informationen über die Gründe der aktuellen Lastverteilung.
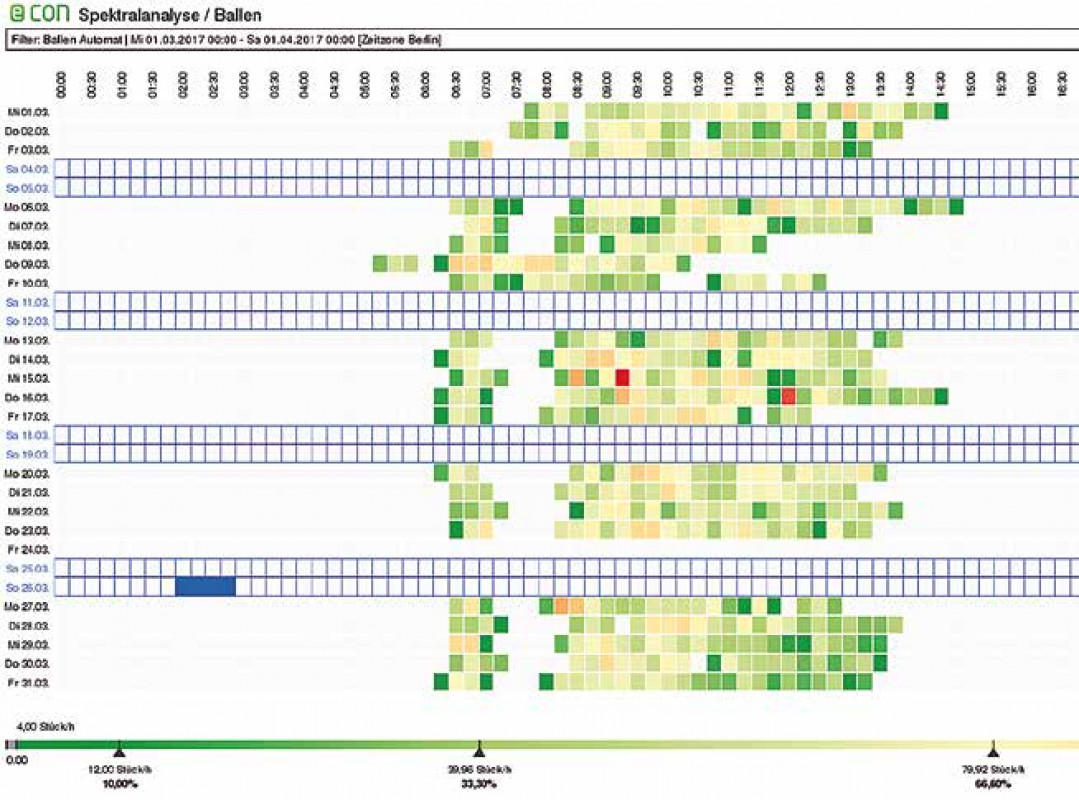
Neben der verbesserten Übersicht können auftretende Fehler und Probleme sofort angezeigt werden. Im besten Fall wird der Fehler mit einer „Known Error Database“ abgeglichen und direkt der optimale Lösungsansatz vorgeschlagen. Dadurch steigt die Prozesssicherheit und der Normalbetrieb kann schnellstmöglich fortgeführt werden.
Neben der Datenaufnahme in den einzelnen Teilprozessen gibt es auch prozessübergreifende Systeme, wie zum Beispiel ein Energiemanagementsystem, welches konstant Daten aufnimmt. Über eine geschickte Datenkorrelation können Auswertungen und Vorhersagen über den Energieverbrauch gemacht und diesen Ereignissen zugeordnet werden. Aber auch einzelne Prozesszeiten, wie Warmhaltezeit, Stillstandzeit und Abkühlzeit lassen sich mit der Aufnahme der richtigen Zeitstempel ermitteln. Solche Analysen erleichtern eine Zertifizierung, wie die ISO 50001 oder 50006, ungemein. Über die Auswertungen sollen erhöhte Verbrauchswerte und Lastspitzen zum frühestmöglichen Zeitpunkt erkannt werden und die Möglichkeit bieten, frühzeitig regelnd in den Prozess einzugreifen. Dabei wird das Ziel verfolgt, Schlüsselstellen im Prozess zu erkennen, die für unnötig hohe Verbräuche verantwortlich sind. Bei einem hochenergetischen Betrieb wie einer Gießerei steht man vor einer großen Herausforderung, wenn es um die Einführung und Realisierung neuer datengebender Systeme geht.
Ausgangssituation
Zur Entwicklung von Optimierungsverfahren ist es im ersten Schritt notwendig, die bestehenden Strukturen und Abläufe bis ins Detail zu betrachten. Innerhalb des Projekts wurde der Fokus auf den Schmelzbetrieb, die Formherstellung und den Sandkreislauf gelegt. Dabei ist zu beachten, dass die Energieverbräuche noch nicht automatisch, sondern monatlich durch manuelles Ablesen der Stromzähler festgehalten werden. Aus dem geringen Datenbestand war eine tiefgehende Analyse von zum Beispiel Spannungsspitzen zwar nicht möglich, eine grobe Kategorisierung der Stromverbräuche analog der Materialflüsse konnte jedoch vorgenommen werden. Somit ließen sich die Verbräuche aus den unterschiedlichen Prozessstufen und Anlagen für das Processing von Eisen und Formsand den produzierenden Abteilungen zuordnen und erste Kennzahlen konnten gebildet werden.
Neben den energierelevanten Daten wurde der Produktionsablauf im Detail betrachtet. Dabei wurde die vorhandene Prozessdokumentation durch das Fachwissen der Meister und Facharbeiter ergänzt. Die erhobenen Daten konnten in Folge mit dem Datenbestand aus dem ERP-System vervollständigt werden, das alle Stammdaten, wie die Kundenbestellungen inklusive der Modellbeschreibungen, Fertigungsgewichte und -legierungen beinhaltet. Ein solches System bildet den digitalen Mittelpunkt der Firma und somit auch das Datenfundament, auf das alle weiteren Prozesse aufbauen. Die Kundenanfragen werden dort aufgenommen und für die Produktion eingeplant. Gerade im Gießereihandwerk werden noch relativ wenige Arbeitsvorgänge automatisiert und computergesteuert bearbeitet, da viele mechanische Schritte durch Facharbeiter händisch ausgeführt werden müssen, um ein Gussteil herzustellen. Dementsprechend schwer lassen sich Prozesse durch IT-Unterstützung optimieren, vor allem im sogenannten Mischkastenbetrieb, bei dem verschiedene Gussteile je nach Tagesprogramm in unterschiedlichen Konstellationen in einem Kasten eingeformt werden. Dazu kommt, dass bis dato überhaupt nur sehr wenige Daten während des Produktionsprozesses aufgenommen werden. Speziell im Bereich Handformguss mit Mischkästen ist es daher äußerst aufwendig, eine genaue Anordnung und Zuordnung der einzelnen Modelle vorzunehmen.
Nach intensiver Betrachtung der bestehenden Produktionsabläufe und eingesetzten Prozesse sowie der existierenden IT-Strukturen hat sich herausgestellt, dass ein weiteres vollautomatisiertes Erfassen von Prozessparametern durch IT-Unterstützung erst sinnvoll ist, wenn die bestehenden IT-Systeme bewusst und optimiert eingesetzt werden. Aus diesem Grund wurde zunächst ein hoher Wert auf die optimale Nutzung der bestehenden Systeme gelegt, um das volle Funktionsspektrum der Software auszunutzen.
Vorgehen und Lösungsansätze
Im ersten Schritt wurde aus den aufbereiteten Prozessinformationen ein vollständiger Prozessablauf ausgearbeitet. Es wurde eine gesamtheitliche End-To-End (E2E) Betrachtungsweise zu Grunde gelegt, mit der ERP-Datenbank im Mittelpunkt als Synchronisationsschnittstelle. Dabei wurden auch die kritischen Pfade im Unternehmen aufgezeigt, das heißt Abhängigkeiten, die zwischen einzelnen Abteilungen und Bereichen bestehen. Bei Verzögerungen hat dies zur Folge, dass nachgelagerte Abteilungen verspätet beginnen und somit unter sehr hohem Zeitdruck arbeiten müssen. Dadurch steigt verständlicher Weise auch die Fehlerquote.
Neben dem Re-Design des Herstellungsprozesses wurden auch neue Methoden der Datenakquise eingeführt. Die Datensätze aus den bestehenden Systemen sowie aus den neuen Quellen mussten in eine gemeinsame Datenhaltung integriert werden. Durch gezielte Auswertung und Visualisierung kann der Herstellungsprozess transparent abgebildet und in einer Web-Applikation dargestellt werden. Nachfolgend sind diese drei Teilbereiche im Detail beschrieben.
Datenakquise
Energiemonitoring. Im Zuge dieses Projektes wurde ein marktgängiges Energiemanagement- und Energiedatenerfassungssystem eingeführt, das den manuellen Arbeitsaufwand des monatlichen Ablesens der Zählerstände einspart. Zudem werden nun die Energiedaten täglich von vielen Messstellen automatisch aufgezeichnet und in einer Datenbank abgespeichert. Durch eine solche konsistente Datenbasis können verschiedene Algorithmen zur Analyse der Daten verwendet und auf die geschehenen Ereignisse gemünzt werden. Es ist somit einfach möglich, Lastspitzen und Überschreitungen von Schwellenwerten aufzuzeigen und zu alarmieren. Es konnte zum Beispiel durch Verkürzen des Zeitintervalls der Wamhaltephase vor dem ersten Aufschmelzen die Kaltstartkurve der Elektroöfen optimiert und dadurch der Energieverbrauch gesenkt werden. Die eingebetteten Auswertefunktionen erlauben es, die Daten darzustellen und aufzubereiten sowie in zeitlicher Relation zu den Prozessdaten darzustellen. Mobile-App. Es werden die qualitätskritischen Prozessparameter der einzelnen Teilbereiche innerhalb des Produktionsprozesses benötigt, um zielgerichtet Optimierungen vornehmen zu können. Damit lassen sich zum Beispiel Kundenaufträge durchgängig rückverfolgen und Fehlerquellen optimiert analysieren. Gerade im Handformbetrieb mit Mischkästen erweist sich eine digitalisierte Protokollierung der Zuordnung der Modelle zu den Formkästen als sehr schwierig. Aus diesem Grund wurden an Kästen und Pfannen Barcode-Tags angebracht. Über eine eigens entwickelte Mobile-App werden verschiedene produktionsrelevante Prozessparameter aufgenommen und an eine Datenbank gesendet (Bild 3). Durch die erste Funktion werden die Kastenbelegung und der Kasten aufgenommen. In der zweiten Funktion wird die Pfanne zum Abstich des Ofens abgescannt. Die dritte Funktion verheiratet die Pfanne mit dem Kasten. Bei der letzten Funktion werden beim Auspacken der Kasten und die Auspacktemperatur aufgenommen. Durch die erfassten Zeitstempel lassen sich einzelne Prozesszeiten wie Zeitpunkt des Formens, des Gießens und des Auspackens festhalten. Zudem können Abkühlzeiten errechnet werden. Des Weiteren lassen sich die Rückmeldungen im ERP-System über diese zusätzlichen Informationen vervollständigen.
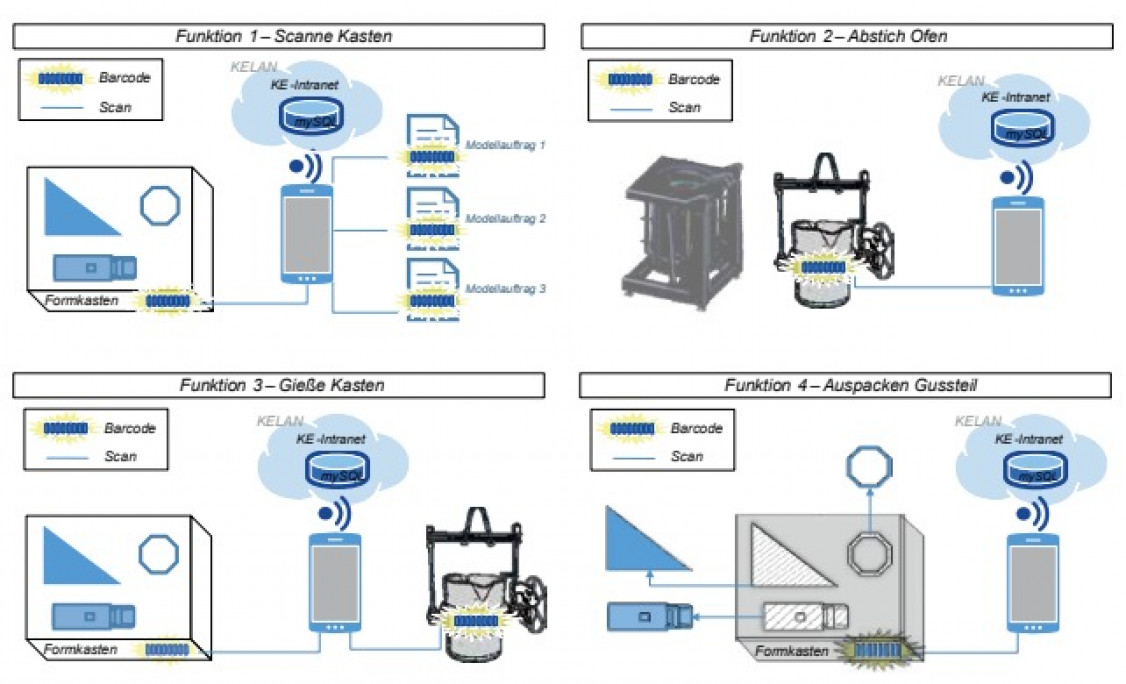
Datenhaltung
Um eine gemeinsame Datenbasis aufzubauen, wurde ein Datawarehouse aufgebaut (Bild 4). Dadurch lassen sich Auswertungen auf einer konsolidierten Datenbasis machen, wie zum Beispiel das Sand-Eisenverhältnis eines „Mischkastens“. Die unterste Ebene zeigt die einzelnen Datenquellen. Danach folgt eine Verdichtung der Daten über einen sogenannten ETL-Prozess (Extract, Transform, Load). Hierbei werden nur die relevanten Tabellen und Spalten aus der Datenbank ausgewählt und anschließend in einer neuen Datenbank gespeichert. Diese neue Datenbank enthält demnach eine Kopie aller wichtigen Datensätze der einzelnen Quellen. Eine tägliche Synchronisation hält die Daten aktuell. Aus dieser Datenbank lassen sich Auswertungen generieren und zum Beispiel in Web-Anwendungen nutzbringend darstellen [2].
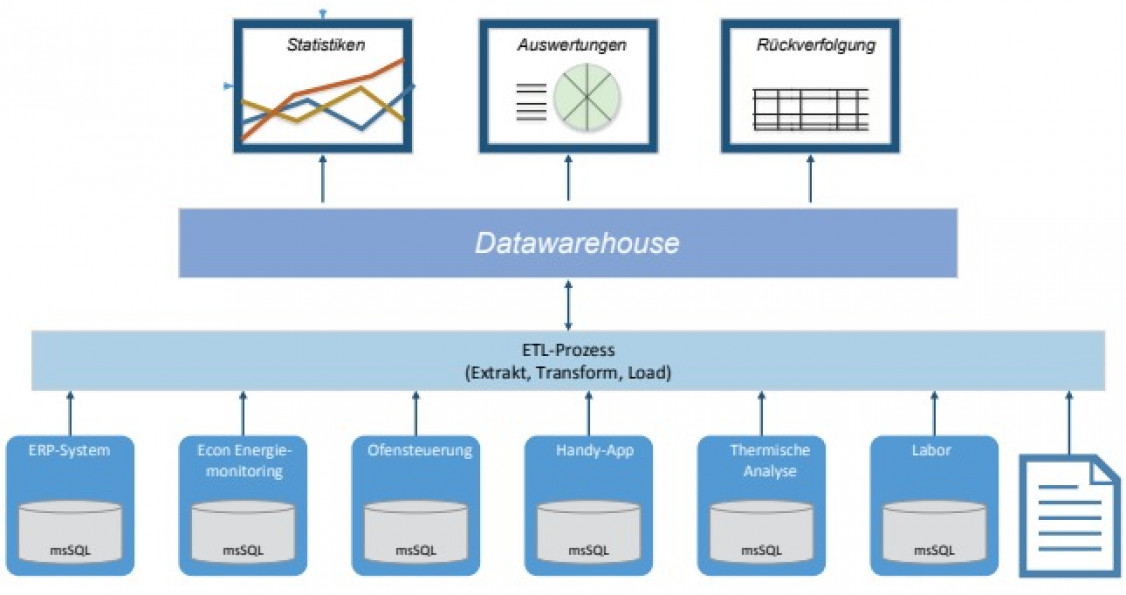
Auswertung & Visualisierung
Auftragsmonitoring. Im Auftragsmonitoring werden die laufenden Aufträge aller Kunden dargestellt. Durch Filterfunktionen kann die Ansicht der angezeigten Daten reduziert werden, um einen schnellen Überblick zu ermöglichen. Es bestehen zwei Ansichten, die Wochenplanung und die Kundenansicht. In der Wochenplanung sind die aktuell anstehenden Kundentermine sichtbar, dies ermöglicht eine optimierte Planung sowie Steuerung von zeitkritischen Aufträgen. Dabei ist auch die Formkastenbelegung ersichtlich. Diese Informationen helfen der Arbeitsvorbereitung, die nächsten Tage zu planen und eine optimale Ausnutzung der unterschiedlich großen Formkästen zu ermöglichen. Die zweite Ansicht ist eine Kundensicht. Dabei werden alle laufenden Aufträge eines bestimmten Kunden angezeigt. Bei kundenseitigen Rückfragen kann somit eine schnelle und valide Aussage über die einzelnen Aufträge gegeben werden. Über Java-Script-Funktionen kann noch weiter gefiltert werden, was für die Meister der unterschiedlichen Bereiche einen erheblichen Vorteil bringt. Alle Informationen werden direkt aus der Datenbank des ERP-Systems entnommen und beinhalten somit immer die aktuellsten Informationen. Durch die Datenkorrelation mit der Ofensteuerung lassen sich die metallurgischen Daten der Schmelze pro Gusskasten nachvollziehen. Somit können Gussfehler bis ins Detail analysiert werden.
Panel im Leitstand der Ofensteuerung. Bild 5 verdeutlicht, welche Daten aus welchen IT-Systemen genutzt werden, um ein digitales Panel im Leitstand der Ofensteuerung aufzubauen. Es zeigt live die Informationen aus dem Formbereich der Gießerei. Dabei werden die einzelnen Gussgewichte der unterschiedlichen Modelle im Formkasten summiert, damit der Ofenmeister die korrekte Menge der Schmelze vorbereiten kann. Früher wurden diese Informationen über Laufzettel an den Ofenmeister herangetragen, mit zusätzlichen Gewichtszugaben für das Anschnittsystem. Durch die neue digitale Übersicht werden direkt die korrekten Informationen aus dem ERP-System verwendet und es kann nicht zu Schreib- oder Verwechselungsfehlern in Gewicht oder Legierung kommen. Ein weiterer großer Vorteil ist, dass in der Detailansicht auch Fotos der Ober- und Unterkästen zu sehen sind. Damit lässt sich die genaue Belegung des Formkastens nachvollziehen und dokumentieren. Bei den Mischkästen kann daraus eine erforderliche Anpassung der Schmelzmenge resultieren. Die Menge des flüssigen Eisens muss möglichst dem berechneten Gießgewicht entsprechen. Wird „aus Sicherheitsgründen“ zu viel Material erschmolzen, ist die Folge ein entsprechender „energetischer Ausschuss“. In diesem Zusammenhang liegt in der exakten Berechnung des Speiser- und Anschnittsystems ein ganz erhebliches Optimierungspotential. Entsprechende Entwicklungsschritte sind eingeleitet.
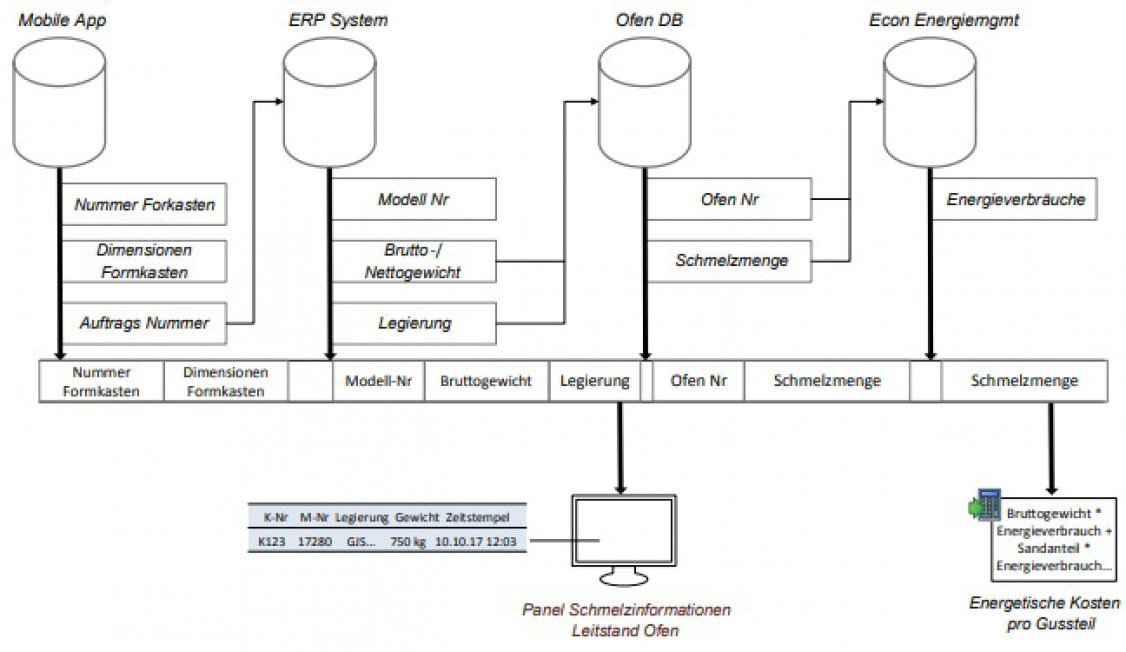
Nutzen & Ausblick
Der offensichtlichste Nutzen der in den betrieblichen Ablauf adaptierten Entwicklungsschritte ist die Transparenz der Prozesskette über alle Abteilungen hinweg. Dadurch lassen sich zeitliche Engpässe schnell identifizieren und einzelne Aufträge gezielt priorisieren. Bei Qualitätsproblemen kann über das Datawarehouse der komplette Herstellungsprozess nachvollzogen werden, vom Kasten über die Pfanne bis hin zu der metallurgischen Zusammensetzung der Schmelze. Ebenso können durch die unterschiedlichen Prozesszeiten Fehler identifiziert werden. Zum Beispiel wenn Gussteile zu früh und somit zu heiß ausgepackt werden. Da die gesamten Informationen über Jahre gehalten werden, können ab einer geeigneten Datenmenge maschinelle Lernverfahren eingesetzt werden, um tiefere Analysen zu fahren. Damit lassen sich immer wieder auftretende Fehlerbilder in einzelne Kategorien aufteilen und über Ähnlichkeitsberechnungen vergleichbare Prozessparameter identifizieren, welche für eine Fehlerbildung der mögliche Grund waren. Wenn solche vermeintlich fehlerproduzierenden Prozessparameter erneut auftreten, kann eine Alarmierung erfolgen und bereits vor dem Abgießen Gegenmaßnahmen ergriffen werden. Somit lässt sich die Ausschussrate senken und der damit verbundene Energieaufwand einsparen. Neben dem Aufbau einer solchen Fehlerdatenbank kann auch eine gesamtheitliche Auswertung des Datawarehouse erfolgen. In Bild 5 sind exemplarisch der Datenfluss und der Informationsgehalt aus den einzelnen Systemen ersichtlich. Es wird angedeutet, dass Informationen nicht nur mitgeführt werden, sondern auch als Input-Parameter für Abfragen bei den aufbauenden Datenbanken zur Verfügung stehen. Als Ergebnis können die gesamten anfallenden Energiekosten von Schmelze und Formsand auf die einzelnen Gussteile berechnet werden. Diese Information war in einem solchen Detailgrad noch nicht bekannt, da die vorweg erwähnte monatliche manuelle Aufnahme der Energieverbräuche nur unzureichende Informationen geliefert hat. Die energetischen Kosten pro Gussteil können für die Preisbildung verwendet werden, helfen aber auch bei Energiezertifizierungen, da ein stetiges und nachhaltiges Konzept zugrunde liegt.
Das Projekt verdeutlicht, wie eine Gießereifertigung mit Hilfe von sogenannten Digitalisierungsmethoden durchsichtiger und strukturierter gestaltet werden kann. Dabei kommt es ganz wesentlich darauf an, eine klare Zielsetzung zu formulieren, in diesem Falle die Verbesserung von Energie- und Ressourceneffizienz. Notwendig ist dies, da jede „Zielsetzung“ immer auch ganz individuelle Informationen und damit auch Datenaufbereitungsmethoden benötigt. In diesem Sinne ist „Digitalisierung“ als eine konsequente und intelligente Anwendung modernster und innovativer IT-Werkzeuge auf eine klar formulierte Zielsetzung zu verstehen. Die in diesem Artikel präsentierten Arbeiten sind Bestandteil des Projektes IEREGUSS, gefördert durch die Deutsche Bundesstiftung Umwelt.
Literatur
[1] Saleem et al.: Giesserei 100 (2013), S. 32ff
[2] Alpar: Anwendungsorientierte Wirtschaftsinformatik, Springer, 2014, ISBN 978-3-658-00521-4, S. 234 ff
Schlagworte
DesignDigitalisierungEisenFertigungFotoGießereiGussGussfehlerGussteileKernherstellungProduktionProzessoptimierungSchmelzenSicherheitSoftware