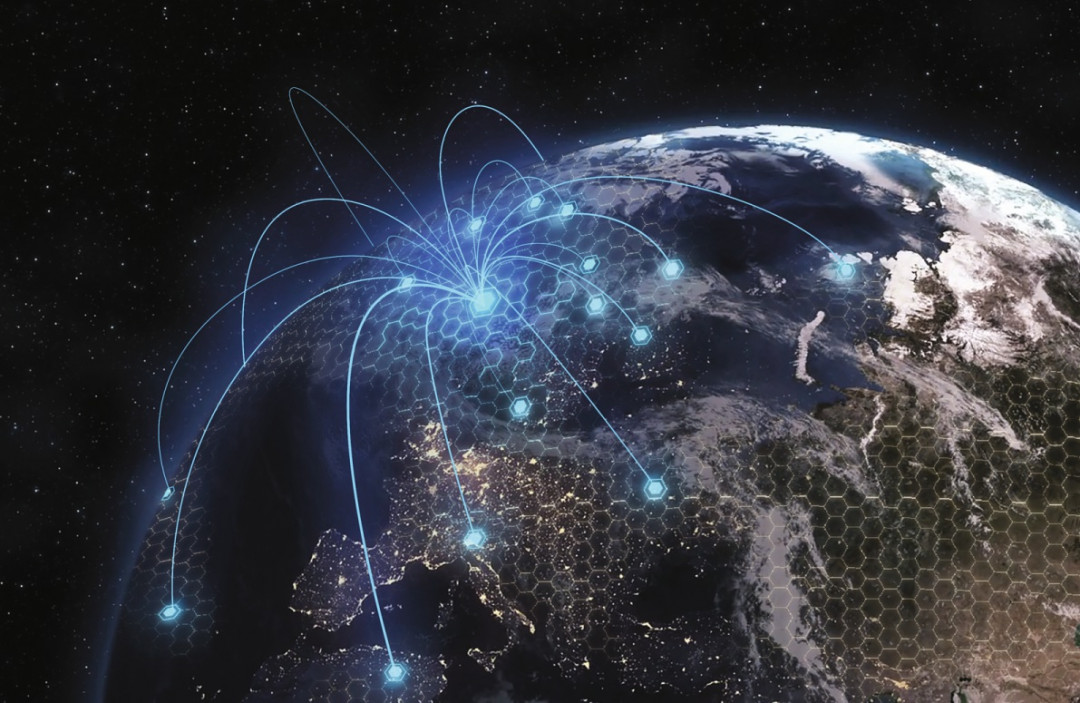
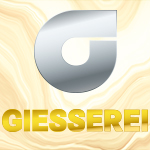
Im Tagesgeschäft sehen sich produzierende Unternehmen stetig unterschiedlichsten Herausforderungen gegenüber, die es möglichst rasch und effizient zu lösen gilt. Insbesondere für Druckgießereien mit ihrem hochgradig anspruchsvollen Produktionsverfahren ist das Erreichen maximaler Produktionseffektivität eine stete Aufgabe. Die umfassende Weiterentwicklung der Digitalisierung hin zum Visionsbild Industrie 4.0 ist dabei ein konsequenter Weg, um diese Hürden besser zu meistern sowie die Flexibilität des Produktionssystems zu verbessern. Mit smartfoundry.solutions bietet die Oskar Frech GmbH und Co. KG entsprechende kundenspezifische Digitalisierungslösungen an.
VON ALEXANDER MARKS UND KAI KERBER, SCHORNDORF
Im Zuge der GIFA 2019 stellte die Oskar Frech GmbH und Co. KG erstmalig das neue Produktportfolio smartfoundry.solutions vor. Im Gegensatz zu traditionellen Produkten eines Maschinenherstellers handelt es sich hierbei um von Druckgießern für Druckgießer entwickelte modulare Software-Applikationen, Dienstleistungen und Shopfloor taugliche Hardwarelösungen. Das Dienstleistungsspektrum enthält zudem die Administration der Systemkomponenten, die Wartung der Hard- und Software sowie das Management der ITSecurity. Druckgießer finden hier ein modulares Leistungspaket, mit dem maßgeschneiderte Digitalisierungsmaßnahmen umgesetzt werden können.
Herausforderungen für produzierende Unternehmen
Als produzierende Unternehmen müssen Druckgießereien eine maximale Produktionseffektivität in einem hochgradig anspruchsvollen Produktionsverfahren bei oft sehr variantenreichem Produktionsprogramm erreichen. Wesentliche Kennzahl ist hierbei die OEE (Overall Equipment Effectiveness) [1], dem Produkt aus Verfügbarkeit, Produktivität und bestmöglicher Qualitätsrate (Bild 1).
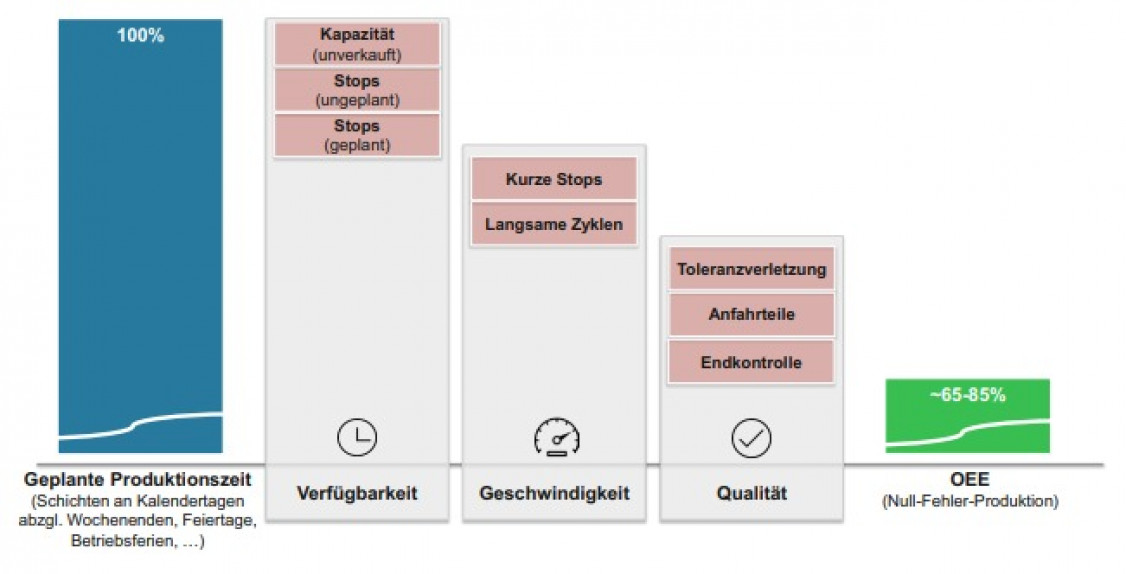
Die sich aus dem laufenden Tagesgeschäft ergebenden Herausforderungen sind dabei möglichst rasch und effizient zu lösen, denn abhängig vom Standardisierungsgrad des Produktionsprogramms kann es zu signifikanten Verfügbarkeitsverlusten durch Wechselzeiten zwischen den unterschiedlichen Produkten kommen. Sie können bis zu 20 Prozent abhängig von der abgebildeten Komplexität betragen.
Der Standardisierungsgrad berechnet sich aus dem Quotienten von Maschinenanzahl durch aktive Produkte (Bild 2).
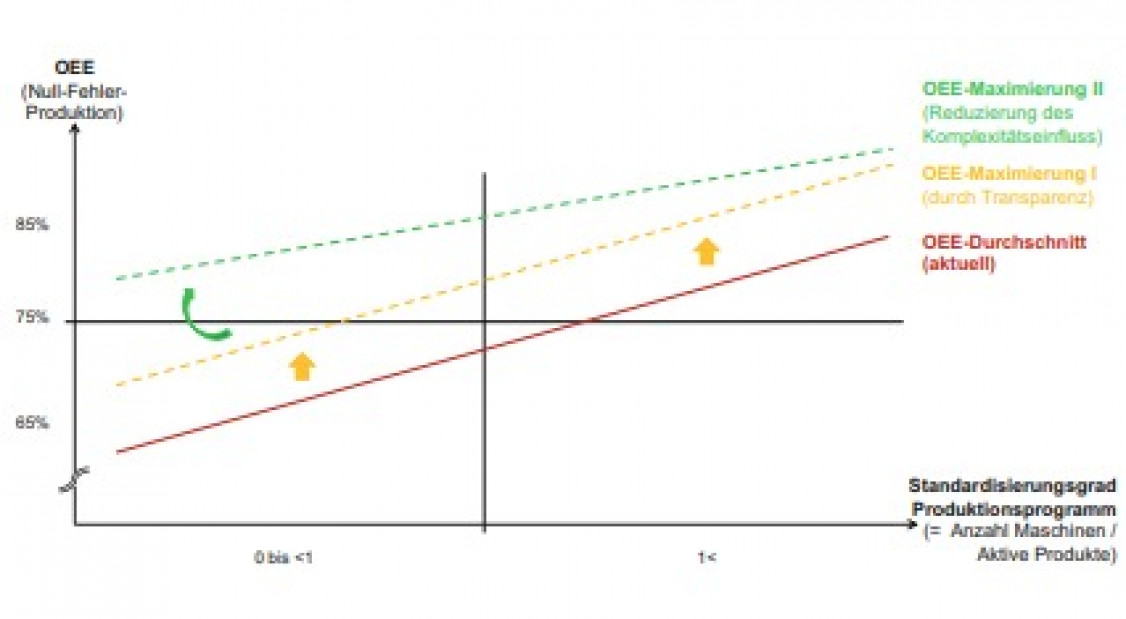
Die Digitalisierung und weitere Maßnahmen zur Umsetzung des Visionsbilds Industrie 4.0, spezifischer der Gießerei 4.0 [2], sind dabei zeitgemäße Hilfsmittel, um die genannten Optimierungsaufgaben besser zu bewältigen sowie die Flexibilität des Produktionssystems zu verbessern. Die smartfoundry.solutions-Software-Applikationen, Hardwaresysteme und Services wurden im Hinblick auf diese Zielsetzung als modulares Produkt- und Services-Portfolio ausgestaltet und spezifisch für den Einsatz in der Druckgießerei entwickelt. Mithilfe der Produkt- und Servicemodule können Druckgießer zusammen mit dem smartfoundry.solutions-Team maßgeschneiderte Digitalisierungsprojekte zielgerichtet und effizient umsetzen.
Zukunftsorientiertes Produktportfolio
Das smartfoundry.solutions-Produktportfolio und dessen Entwicklungs-Roadmap bestehen aus einzelnen Produktgruppen, die sich unter anderem am Industrie 4.0-Maturity-Index [3] orientieren (Bild 3).
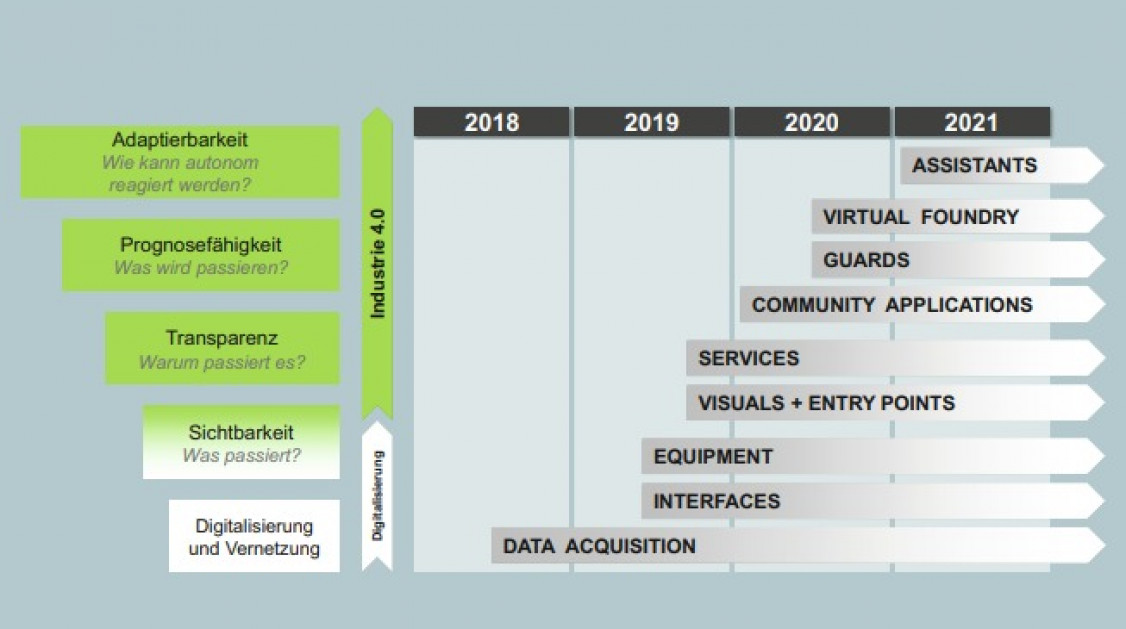
Zur Digitalisierung und Vernetzung werden Komponenten der Produktgruppen Data Acquisition und Interfaces verwendet. Mithilfe von Visual- und Entry-Point-Applikationen, die auf digitalen Ein- und Ausgabegeräten der Produktgruppe Equipment installiert sind, werden Daten visualisiert oder zusätzliche Daten wie z.B. Qualitätsdaten, erfassbar gemacht. Diese Produkte adressieren vornehmlich die Index-Stufen Sichtbarkeit und Transparenz. Sie bilden zudem die Basis für das smartfoundry.network, einem Netzwerk, das alle Komponenten der genannten Produktgruppen vernetzt. Services und Community Applications erhöhen die Transparenz im eigenen Unternehmen und in der smartfoundry.community. Zudem werden mit ihrer Hilfe hochwertige Systeme in den Indexstufen Prognosefähigkeit sowie Adaptierbarkeit entwickelt. Guards (passive Assistenzsysteme) und Assistants (aktive Assistenzsysteme) sind, zusammen mit dem Digitalen Zwilling der Druckgießerei (Virtual Foundry) der höchsten Index-Stufe Adaptierbarkeit zuzuordnen.
Verschlüsselter Datentransfer
Basis des smartfoundry.network bildet das in der Regel bereits vorhandene Ethernet Netzwerk, welches heute für den „Remote Service“ der Produktionsmaschinen genutzt wird. In dieses Netzwerk werden die einzelnen Komponenten integriert, wodurch eine zusätzliche zeit- und kostenintensive Vernetzung entfallen kann (Bild 4).
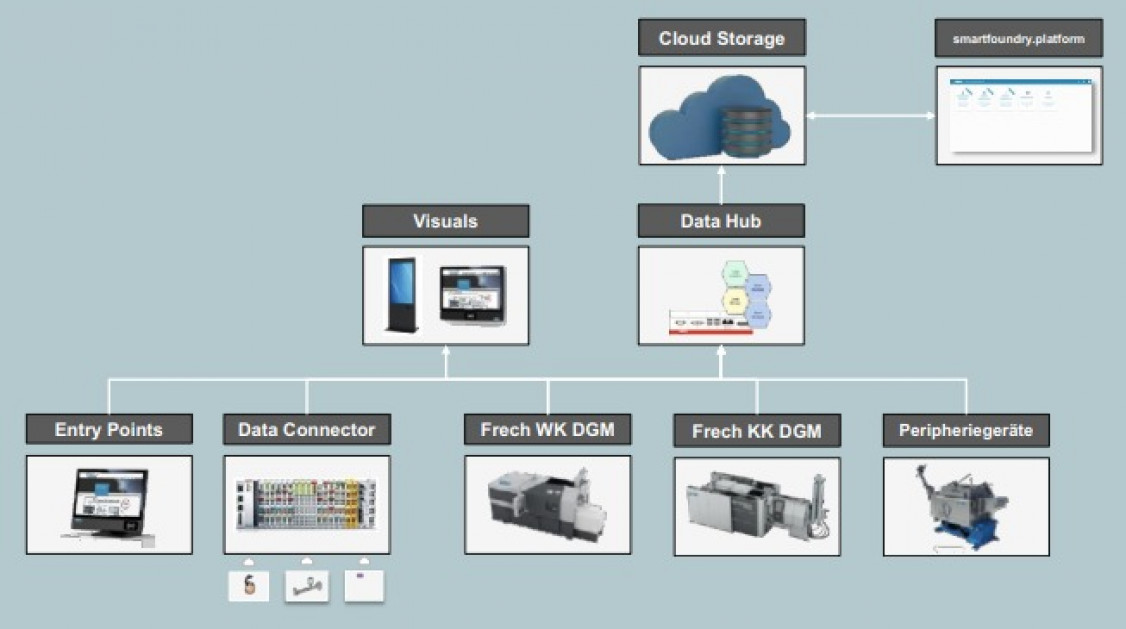
Der Datenaustausch zwischen den einzelnen Komponenten geschieht verschlüsselt. In der Regel ist es heute ausreichend, die ersten Digitalisierungsvorhaben mit dem vorhandenen Netzwerk durchzuführen und im späteren Projektverlauf weitere Netzwerkinfrastrukturen aufzubauen. Im Ermessen der Druckgießerei kann jedoch bereits heute eine dedizierte Netzwerkinfrastruktur genutzt werden, um das Digitalisierungsnetzwerk im Sinne der IT-Security noch zu schützen. Dies erlaubt zudem, für wachsende Datenvolumina in der Zukunft gerüstet zu sein.
Gezielte Datenspeicherung mit dem Data Hub Bei der Erfassung von industriellen Daten und deren Analyse werden heute in der Regel zwei grundsätzliche Vorgehensweisen realisiert. Eine der Vorgehensweisen sieht vor, möglichst alle verfügbaren Daten von Maschinen und Prozessen in ein Speichersystem zu überführen, ohne die Daten zu selektieren oder vorab in Relation zueinander zu bringen. Das Filtern der Daten und die Bildung von Zusammenhängen wird erst in der Analysephase durchgeführt. An dieser Vorgehensweise ist vorteilhaft, dass relativ schnell erste Daten gespeichert und visualisiert werden können. Einer bestehenden Datenanalyse können zudem weitere bereits aufgezeichnete Daten hinzugefügt werden, auch wenn dies ursprünglich nicht absehbar war. Nachteilig an dieser Vorgehensweise gestaltet sich, dass die Daten ggf. nicht im benötigten Format, ausreichend gefiltert oder mit einer ausreichenden Aufzeichnungsrate zur Verfügung stehen. Ebenso werden ggf. nicht nutzbare oder redundante Daten über lange Zeit unbemerkt aufgezeichnet. Kritisch ist jedoch vor allem, dass wichtige Relationen zwischen den einzelnen Daten ggf. nicht mehr erzeugt werden können und so Zusammenhänge verloren gehen.
Bei der alternativen Vorgehensweise werden gezielt nur Daten erfasst, die vorab ausgewählt und oftmals speziell erzeugt worden sind. Die Daten werden zudem meist permanent gefiltert und mit der für den Verwendungszweck angepassten Aufzeichnungsrate erfasst. Zudem werden hierbei alle nötigen Relationen zwischen den Daten gespeichert. Bei diesem Vorgehen ist vorteilhaft, dass bereits eine hohe Datenqualität und Informationsdichte zu Beginn der Analysephase zur Verfügung stehen. Nachteilig ist der zusätzliche Aufwand vor und während der Datenerfassung, was zu einer ausgedehnteren Anfangsphase der Digitalisierungsprojekte „ohne Ergebnisse“ führt. Zudem stehen in der Analysephase ggf. Daten nicht zur Verfügung, da mit deren Nutzung in der Anfangsphase des Projektes nicht gerechnet wurde. Die erste Vorgehensweise erscheint attraktiv, da sie rasch erste Ergebnisse ermöglicht und eine einfache Erweiterbarkeit der Lösungen verspricht. Zudem wird wenig Domänenwissen vorausgesetzt, welches für die Auswahl und Erzeugung von zielgerichteten Datensätzen nötig wäre. In der industriellen Praxis ist diese Vorgehensweise jedoch nur begrenzt zukunftsfähig einsetzbar.
Die heute eingesetzten Produktionsanlagen und deren Maschinensoftware sind in der Regel nicht zur Erfassung von Maschinen- und Prozessdaten konzipiert, sondern dienen der Realisierung von möglichst stabilen Produktionsprozessen. Daten werden vornehmlich für die Prozessregelung und primär für die situative Anzeige auf Bildschirmseiten der Maschinensteuerung erfasst und aufbereitet. Werden solche Daten für Digitalisierungs- und Analysevorhaben verwendet, treten schnell verschiedene Problemstellungen auf. Viele der Informationen sind unzureichend strukturiert bzw. kategorisiert, Informationen sind oftmals nur zu gewissen Zeitpunkten vorhanden. Viele in der Retrospektive wichtige oder interessante Daten sowie nicht visualisierte Zusammenhänge sind oftmals schlichtweg nicht vorhanden.
Für die Datenerfassung der smartfoundry. solutions-Produkte- und Dienstleistungen wurde entsprechend ein modulares Datenbanksystem entwickelt, mit dem die Aufzeichnung von verschiedenen Datentypen mit unterschiedlichster Datendichte möglich ist. Umfassende Relationen zwischen den Daten und den Datenquellen (Maschinen und deren Komponenten, Werkzeuge und Maschinen, Produktionslose und Artikel usw.) können hinterlegt werden. Zudem ging bei der Gestaltung der Datenumfänge das Druckguss-Domänenwissen der Frech Gruppe mit ein, was eine höherwertige, anwendungsbezogene Datenerfassung ermöglicht. Das Datenbanksystem (Local Storage) wird auf einem Industrie-PC, dem Data Hub, betrieben. Der Data Hub bildet den zentralen Punkt des smartfoundry. network. Die Komponenten und andere über Schnittstellen (Interfaces) verbundene Systeme senden permanent verschlüsselte Daten an den Data Hub, der sie im Local Storage temporär speichert und in Relation zueinander bringt. Applikationen des smartfoundry.network können zudem vom Data Hub statische Informationen abrufen, wie z.B. Informationen über Maschinen oder Werkzeuge sowie Analysen aus dem Kurzzeit-Datenspeicher des Systems. Das Local Storage und der Data Hub sind nicht für die permanente Speicherung der erfassten Daten konzipiert. Für die Langzeitdatenspeicherung müssen diese in das Cloud Storage oder in eine lokale vom Druckgießer zur Verfügung gestellte Speicherinstanz übertragen werden.
Stetig wachsendes Schnittstellen-Portfolio
Zur Übertragung von Daten zwischen den verschiedenen Komponenten sowie Produktionsmaschinen werden Interfaces (Schnittstellen) verwendet. Grundsätzlich wird soweit dies technisch möglich ist, eine verschlüsselte Datenübertragung realisiert, um ein Mitlesen oder gar eine Manipulation von Daten zu verhindern. Heute können beispielsweise Frech-Druckgießmaschinen der W- und DAW-Reihe sowie K- und DAK-Reihe über für die Datenerfassung spezialisierte Standard-Schnittstellen in das smartfoundry. network integriert werden. Zudem werden derzeit spezielle Schnittstellen für Datenbank- und Softwaresysteme sowie andere Produktionsmaschinen einer Druckgießerei entwickelt. Das Schnittstellenportfolio wird sowohl im Umfang als auch in der Anzahl der Schnittstellen kontinuierlich erweitert und ist eine der heute wichtigsten Komponenten für die Digitalisierung einer Druckgießerei.
Dreischichttaugliche robuste Prozess- und Maschinendatenerfassung
Primäre Maschinen- und Prozessdaten werden bereits heute von modernen Produktionsmaschinen erfasst und können über Interfaces für die Komponenten im smartfoundry.network nutzbar gemacht werden. Um ältere Produktionsmaschinen in die Datenerfassung zu integrieren, müssen Maschinen- und Prozesswerte in der Regel durch zusätzliche Elektronik oder Sensorik erfasst werden. Auch eine detailreiche Beobachtung der Maschinenkomponenten (z.B. für Condition Monitoring) oder des Druckgießprozesses setzt die Installation von zusätzlichen Sensoren voraus. Als Teil des Produktportfolios steht für diese Aufgabe das industrielle Konnektivitäts- und Messsystem Data Connector zur Verfügung. Mithilfe des auf der SPS-Technologie basierenden Systems werden zusätzliche Sensor- und Maschinendaten dreischichttauglich erfasst und über eine OPC-UA-Schnittstelle zur Verfügung gestellt. Ebenso ist es möglich, mit dem Data Connector z.B. Komponenten zu identifizieren (RFID) oder Aktionen auszulösen (Signalleuchten). Der Data Connector wandelt dabei Messdaten in Informationen um, indem z.B. aus einem Messwert eines Sensors über die Verknüpfung mit Metadaten eine „Medientemperatur“ erzeugt wird und wichtige Aggregationen (z.B. Medienbedarf pro Produktionszyklus) berechnet werden. Die Rohdaten der Messung, der Aggregationen und die Metadaten werden über die OPC-UA-Schnittstelle erfassbar gemacht. Die entsprechenden Daten werden anschließend vom Data Hub einer Produktionsmaschine und z.B. einem Produktionslos zugeordnet, sodass die zusätzlich vom Data Connector erfassten Sensordaten nahtlos in die Datenerfassungslogik der Produktion einfließen können.
Für erste im Druckguss häufig auftretende Anwendungsszenarien stehen robuste Sensorsysteme in Anwendungspaketen zur Verfügung (z.B. Überwachung der Werkzeugtemperierung, Erfassung der Umgebungsbedingungen, Funktionsüberwachung der Maschinenkühlung usw.). Ein Sensorpaket umfasst hierbei die eigentliche Sensorik, Montagematerial, Anschlussklemmen der SPS- und Software-Module des Data Connectors. Weitere in der Entwicklung befindliche Sensor- und Konnektivitätspakete (Identifikation, Aktionen, Condition Monitoring usw.) erweitern den Einsatzbereich des Data Connectors stetig. Durch die modulare Ausgestaltung des Systems sowohl in der Hard- als auch in der Software, kann der Mess- und Aktionsumfang des Data Connectors jederzeit erweitert oder verändert werden.
Rollenangepasste Applikationen
Erfasste Daten und Ergebnisse von Analysen müssen der Belegschaft einer Druckgießerei in geeigneter Weise nutzbar gemacht werden, damit die Daten für die Lösung der Kernherausforderungen genutzt werden können. Hierzu müssen sie möglichst am richtigen Ort und für den entsprechenden Mitarbeiter in seiner Funktion bestmöglich nutzbar aufbereitet werden. Dies für alle Produkte und Applikationen zu erreichen, ist eine der wesentlichen Prämissen der Produkt- und Serviceentwicklung des smartfoundry. solutions-Teams. Um dieser Anforderung gerecht zu werden, müssen Daten in der Druckgießerei an verschiedenen Orten visualisiert oder zusätzliche Daten und Informationen eingegeben werden können. Hierzu ist in Betracht zu ziehen, dass unterschiedlichste Umgebungsbedingungen in einer Druckgießerei vorhanden sind, von der rauen Umgebung in der Schmelzerei und der Druckgussproduktion bis hin zu den Büros des Managements. Des Weiteren müssen für die verschiedenen Rollen in der Gießerei (z.B. Maschinenbediener, Einrichter, Schichtleiter, Prozessoptimierer, Gießereileiter, …) angepasste Datenbestände und Informationsgehalte zur Verfügung gestellt werden.
Eine Abbildung dieser Bandbreite von Anforderungen in einem monolithischen Soft- und Hardwaresystem ist nahezu unmöglich und hat verschiedene Nachteile. Das Ziel der smartfoundry.solutions-Lösung ist, eine Vielzahl kleinerer modularer Applikationen für verschiedene Rollen auf Visualisierungs- und Eingabegeräten (Equipment) zur Verfügung zu stellen. Bei den Geräten handelt es sich z.B. um robuste PC-Terminals für den Einsatz in der Shopfloor-Umgebung, verschiedene Statusanzeigen, bis hin zu Softwaresystemen für den Web-Browser im Büro bzw. für Mobilgeräte. In der Zukunft können dies z.B. auch Wearables wie Smartglasses oder Smartwatches sein. Die verschiedenen Geräte sowie die entsprechenden Applikationen sind Teil des Produktportfolios. Neben der getesteten Druckgießereitauglichkeit der Geräte ist eine weitere Besonderheit, dass sowohl die Applikationen als auch die Geräte durch den Kunden einzeln für einen gewissen Zeitraum gemietet bzw. lizensiert werden können. Die Visualisierungs- und Eingabegeräte sowie die Applikationen werden vom smartfoundry.solutions-Team administriert, überwacht und bei Ausfall einer Komponente möglichst rasch ersetzt.
Intuitive Eingabe von Informationen
Neben Maschinen- und Prozessdaten, die von Produktionsmaschinen sowie Messoder Softwaresystemen erfasst und für die Digitalisierung der Druckgießerei zur Verfügung gestellt werden, müssen an vielen Stellen in der Produktion Daten von der Belegschaft erfasst und teilweise archiviert werden. Heute geschieht dies oftmals durch eine Vielzahl von nicht verknüpften Einzellösungen. Daten werden an unterschiedlichen Orten in verschiedene Systeme eingegeben und gespeichert. Eine geringe Effizienz bei der Dateneingabe und Datenverarbeitung sowie unvermeidliche Fehler und Inkonsistenzen zwischen den Systemen sind an der Tagesordnung. Zudem werden einige Daten auch heute noch analog abgelegt und sind für die digitale Nutzung erst nach einer gesonderten Digitalisierung verfügbar.
Für die intuitive und effiziente Eingabe von wichtigen Primärdaten gibt es im smartfoundry.solutions-Produktportfolio sogenannte Entry-Point-Applikationen. Beispiele für Applikationen, die für den Einsatz auf dem Shopfloor entwickelt wurden, sind das Quality Panel, eine Applikation zur intuitiven Erfassung von Qualitätsdaten der Gusserzeugnisse (Bild 5) oder das Event Log, eine Applikation zum Protokollieren von Ereignissen, die während der Produktion auftreten. Mit dem Foundry Information Manager, einer smartfoundry.platform-Applikation, können spezifische Informationen zu den Produktionsanlagen oder den Werkzeugen zentral gespeichert werden, die fortan von Visual Applikationen genutzt werden können. Das Ziel von Entry-Point-Applikationen ist die einmalige, möglichst intuitive Digitalisierung von Eingabedaten und die Übermittlung dieser Daten an die Komponenten des smartfoundry.network.
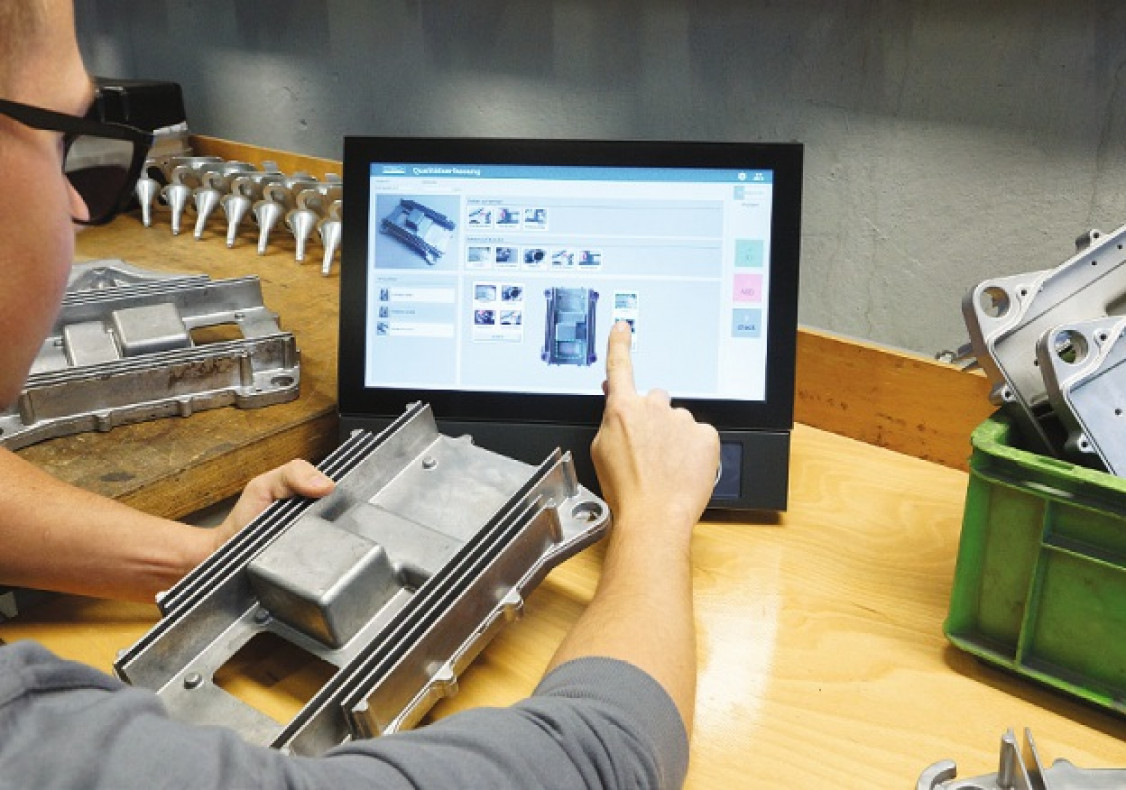
Nutzergerechte Visualisierung von Daten
Bereits heute sind in einer Druckgießerei an vielen Orten unterschiedlichste Daten mit verschiedenster Informationsdichte und Qualität vorhanden. Oftmals stehen in den HMI der Produktionsmaschinen sowie in verschiedensten sonstigen Software-Systemen hochwertige Daten und Informationen zur Verfügung, die jedoch am falschen Ort vorhanden sind, für den Nutzer und dessen Aufgabe nicht aufbereitet vorliegen oder schlichtweg in der Fülle von zur Verfügung stehenden Informationen nicht gefunden oder genutzt werden können. Durch die fortschreitende Digitalisierung und die Erfassung von zusätzlichen Daten kann zu Recht befürchtet werden, dass sich diese Situation noch verschärft. In vielen Fällen können aus den genannten Gründen Daten nicht für die Optimierung von Abläufen und Prozessen in der Gießerei verwendet werden. Der smartfoundry.solutions-Lösungsansatz besteht aus Visual Applikationen, die jeweils eine einzelne Funktion für einen Nutzerkreis, die sogenannte Rolle, realisieren.
- Statusanzeigen für den Shopfloor (Production Transparency Boards): Hier stehen beispielsweise Applikationen zur Verfügung, die den aktuellen Status von Druckgießmaschinen (Foundry Status Board, HPDCM Status Board) oder den Instandhaltungszustand (Maintenance Status Board) visualisieren (Bild 6).
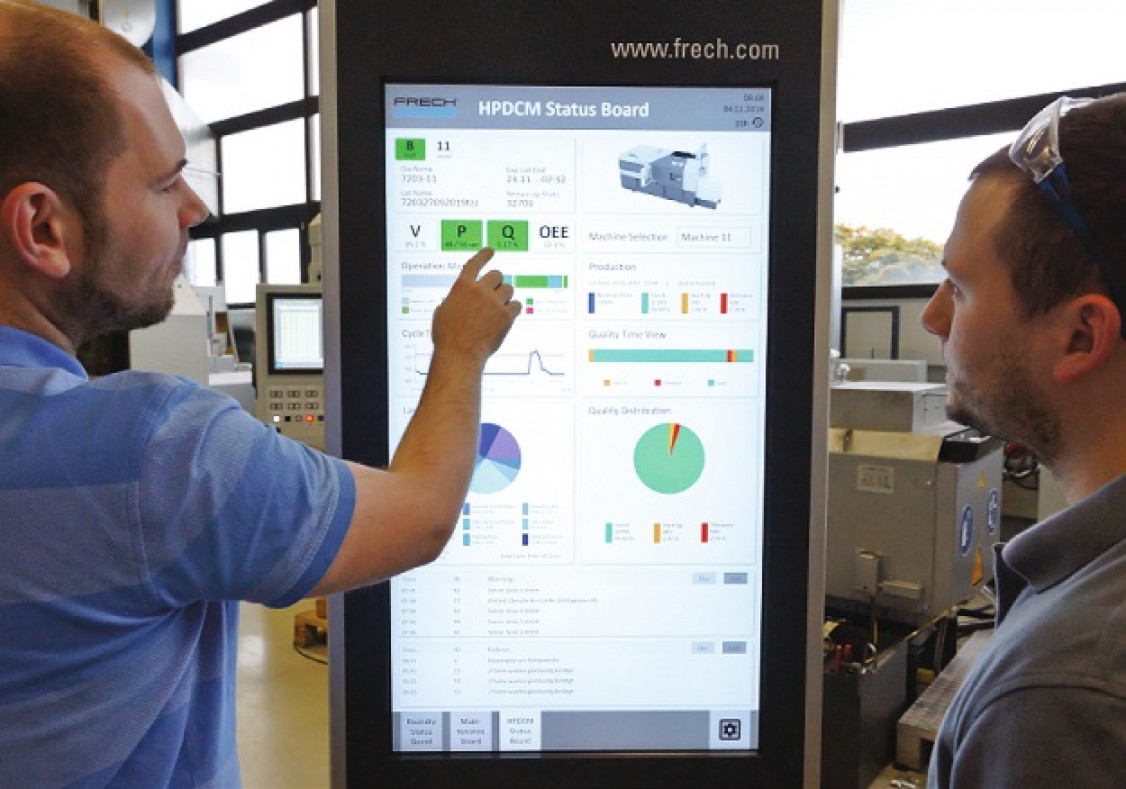
- Smartfoundry.platform: Hier stehen den verschiedenen Nutzern beispielsweise der OEE Agent zur Analyse der OEE der einzelnen angebundenen Maschinen und entsprechender Verlustarten (Verfügbarkeit, Geschwindigkeit und Qualität) zur Verfügung.
- Production Intelligence Board: Dies ist eine BI-ähnliche Applikation zur Betrachtung und Analyse von Betriebszuständen, Fehler- und Warnmeldungen sowie verschiedenster Kennzahlen.
- Production Transparency Tool: Hiermit erhält z.B. der Prozessexperte eine Möglichkeit, Maschinen-, Prozess- und Sensordaten im Detail zu betrachten und zu analysieren.
Das Produktportfolio bietet neben diesen noch weitere Visual Applikationen. Ferner sind Funktionserweiterungen und weitere Applikationen geplant und werden permanent entwickelt. Neben der Fokussierung der einzelnen Applikationen auf eine spezifische Funktion und eine entsprechende Rolle sowie die nutzerorientierte Aufbereitung der Informationen spielt zudem der Transport der Information an den richtigen Ort eine entscheidende Rolle.
Hochverfügbarer Massendatenspeicher
Zur Datenerfassung stehen Data Hubs mit entsprechenden Interfaces zu Produktionsmaschinen, zusätzliche Sensoriken angebunden über Data Connectoren sowie Entry-Point-Applikationen zur Verfügung. Es ist ersichtlich, dass mit entsprechender Ausbaustufe bereits heute größere Datenmengen in kurzer Zeit erfasst werden. Um diese Datenmenge heute und eine wesentlich größere Datenmenge in naher Zukunft mit höchster Verfügbarkeit und Datensicherheit speichern und verarbeiten zu können, ist für einen mittelständigen Betrieb wie eine Druckgießerei eine Speicherung und Verarbeitung der Daten bei einem seriösen und leistungsfähigen Cloud-Dienstleister unumgänglich. Es ist alleine aus wirtschaftlichen Gesichtspunkten kaum möglich, eine ausfallsichere IT-Infrastruktur bei diesen Unternehmen selbst zu realisieren (IT-Hard- und Software, qualifizierter Personalbedarf, Aufbau von mindestens zwei räumlich getrennten Server-Systemen, 24/7-Betrieb von hochverfügbaren Systemen, …).
Da auch der sichere und hochverfügbare Betrieb eines Cloud-Datenspeichers mit gewissem Aufwand und Fachkenntnis verbunden ist, wurde das Cloud Storage in das smartfoundry.solutions-Produktportfolio integriert. Für jeden Kunden wird eine individuelle Cloud Storage Instanz eingerichtet, administriert und betrieben. Es umfasst neben der entsprechenden Cloud-Infrastruktur ein zentrales Datenbanksystem zur Langzeitspeicherung der erfassten Maschinen-, Prozess- und Sensordaten. Die Verbindung zwischen den lokalen Komponenten des smartfoundry. network und den in der Cloud befindlichen Komponenten wird durch einen VPN-Gateway mit verschlüsselten Verbindungen realisiert. Sowohl die einzelnen lokalen als auch die in der Cloud befindlichen Komponenten werden permanent bezüglich der IT-Security sowie der Leistungsfähigkeit und Zuverlässigkeit der Systeme überwacht.
Datenbasierte Entscheidungen
Etwa ein Drittel der Arbeitsplätze und die zugehörigen Rollen einer Druckgießerei befinden sich nicht auf dem Shopfloor. Hierbei handelt es sich um Mitarbeiter/innen, die hauptsächlich in der Büroumgebung der Produktion arbeiten. Viele der Informationen, die diese Mitarbeiter/innen benötigen, entstehen auf dem Shopfloor des Unternehmens, gelangen aber nur stark zeitversetzt und mit hohem Aufwand zu den Arbeitsplätzen im Management, wo oftmals historische Daten für die Arbeitsaufgaben benötigt werden, die im Cloud Storage abgelegt sind. Zudem ist eine Kopplung des Produktions- und des Büronetzwerks aus IT-Security-Gesichtspunkten als hochgradig gefährlich einzustufen. Aus diesen Gründen bieten sich Web-Browser basierte Applikationen für den Einsatz im Bereich der Büros besonders an. Zudem können die Web-Applikationen auf Mobiltelefonen oder Tablets genutzt werden, sodass das Management oder z. B. auch ein Prozessoptimierer, auf Detaildaten an verschiedenen Arbeitsstellen mobil zugreifen kann (Bild 7).
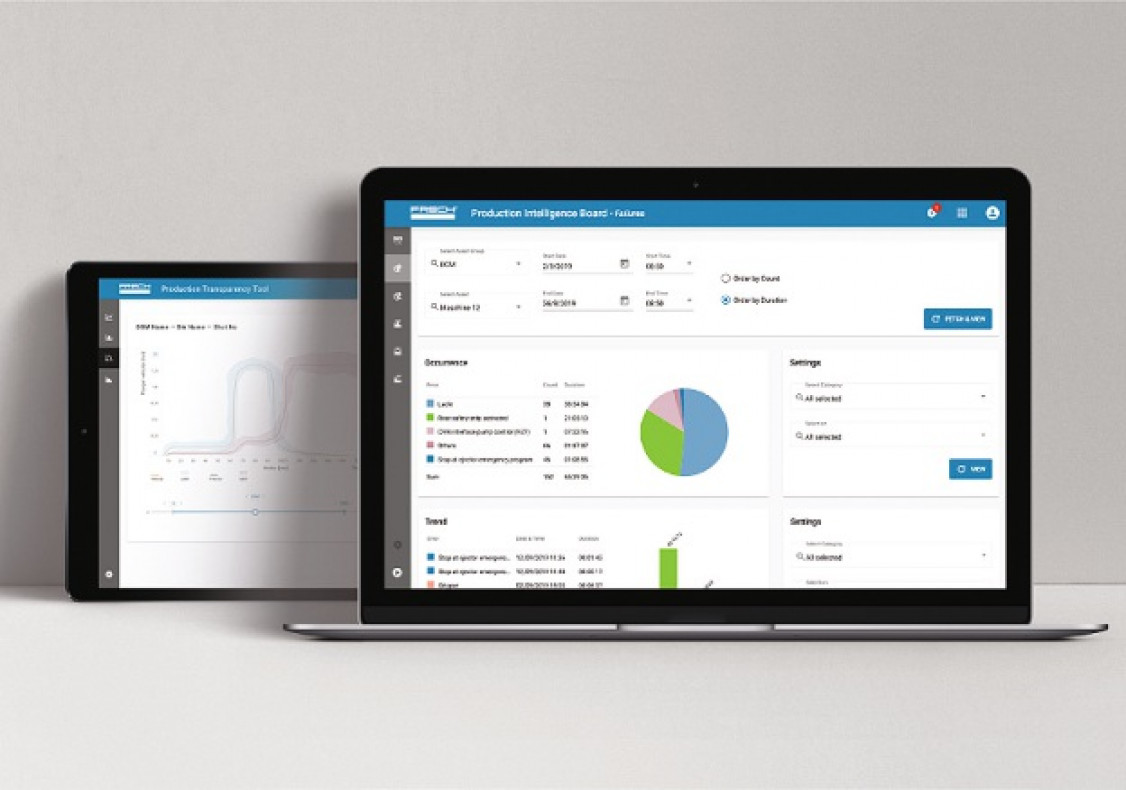
Die smartfoundry.platform stellt eine webbasierte Applikationsumgebung zur Verfügung, die verschiedene Visual und Entry-Point-Applikationen enthält. Der Umfang der Applikationen kann durch zeitliche Lizensierung individuell angepasst werden. Fortwährendes Ziel ist es, Maschinen-, Prozess- und Sensordaten von der Datenerfassung bis zur Visualisierung und Analyse in einer Plattform Applikation vollautomatisch zu verarbeiten. Es ist den Nutzern dann entsprechend möglich, nahezu in Echtzeit auf die Daten vom Shopfloor zuzugreifen, um diese in ihre Entscheidungsprozesse einbeziehen zu können. Dies ist ebenfalls mit historischen Daten möglich, die für die Nutzer mit geringstem Aufwand und in kürzester Ladezeit von der smartfoundry.platform und dem zugehörigen Cloud Storage zur Verfügung gestellt werden.
Gemeinsam Herausforderungen meistern
Die fortwährende Internationalisierung sowie der technologische und strukturelle Wandel in der Automobilindustrie zwingen viele Druckgießereien, die Effizienz des eigenen Unternehmens noch deutlicher zu steigern, um im Wettbewerb konkurrenzfähig zu bleiben. Die Digitalisierung bietet hier ideale Werkzeuge, um dieser und anderen Herausforderungen entgegenzutreten. Einige der Hürden sind nur mit hohem zeitlichem Aufwand oder grundsätzlich nicht von einem einzelnen Unternehmen zu nehmen. Zudem gibt es zeitliche und finanzielle Effekte, die in diesem Zusammenhang in einer Nutzergemeinschaft vorteilhaft sind. Für entsprechende Aufgabenstellungen baut das smartfoundry.solutions-Team derzeit die Basis für die smartfoundry.community als Teil des Dienstleistungs- und Produktportfolios auf. Kernidee ist die gemeinsame Datenerhebung und -nutzung in einer Nutzergemeinschaft. Dabei wird ein Mehrwert (Refund) erarbeitet, wie z.B. eine Technologie oder die Nutzungsmöglichkeit einer Community Applikation. Eine Kernkomponente sind Applikationen, bei deren Nutzung einzelne, explizit ausgewiesene Daten pseudonymisiert einem gemeinsamen Daten-Pool zur Verfügung gestellt werden. Diese Daten werden analysiert und das Ergebnis der Analyse wird den Nutzern der Community-Applikationen als Refund zur Verfügung gestellt. Ein einfaches Beispiel kann eine Benchmarking-Applikation sein, die nicht nur das Benchmarking von Produktionsmaschinen, Werkzeugen oder Technologien innerhalb des Unternehmens erlaubt, sondern ebenfalls im zugehörigen anonymen Daten-Pool der smartfoundry.community.
Komplexere Szenarien sehen zum Beispiel vor, Nutzungsdaten von Komponenten der Druckgießmaschine zu erfassen, die dann zur Entwicklung von Modellen zur Vorhersage der Restlebenszeit dieser Komponenten genutzt werden. So können für strategische Komponenten der Druckgießmaschine wie z.B. das hydraulische Antriebssystem oder Regelventile der Gießachse, hochwertige Condition Monitoring Entwicklungsaufgaben in der Community gelöst werden, die ansonsten schwer oder nicht von einzelnen bewältigt werden können. Entsprechende technologische Herausforderungen wie z.B. die Modellbildung im Bereich des Condition Monitoring oder das Erlangen eines umfassenden Bildes vom Prozessverständnis, können nur gemeinsam für die europäische Produktionsindustrie erarbeitet werden. Hier sind nicht nur Maschinenhersteller und Druckgießer auf eine Zusammenarbeit angewiesen, sondern ebenfalls Druckgießer auf eine Zusammenarbeit untereinander.
Literatur
[1] Productivity Development Team, OEE for Operators, Overall Equipment Effectiveness, Productivity Development Team, Productivity Press, 1999.
[2] Hartmann, D. u.a.: BDG Kompass – Gießerei 4.0. Entwicklungsschritte zur digitalen Produktion, Verband Deutscher Gießerei-Industrie (BDG), Düsseldorf, 2. Überarbeitete Auflage, 2019.
[3] Schuh, G., Anderl, R., Gausemeier J., ten Hompel, M., Wahlster, W. (Hrsg.): Industrie 4.0 Maturity Index. Die digitale Transformation von Unternehmen gestalten (acatech STUDIE), München, Herbert Utz Verlag, 2017.
Den kompletten Artikel finden Sie auch in der GIESSEREI-Ausgabe 12/2019.
Schlagworte
AutomobilindustrieDruckgussEisenFoundryGestaltungGießereiGIFAGussIndustrie 4.0InstandhaltungMesseProduktionSchmelzereiSicherheitSoftwareVerlag