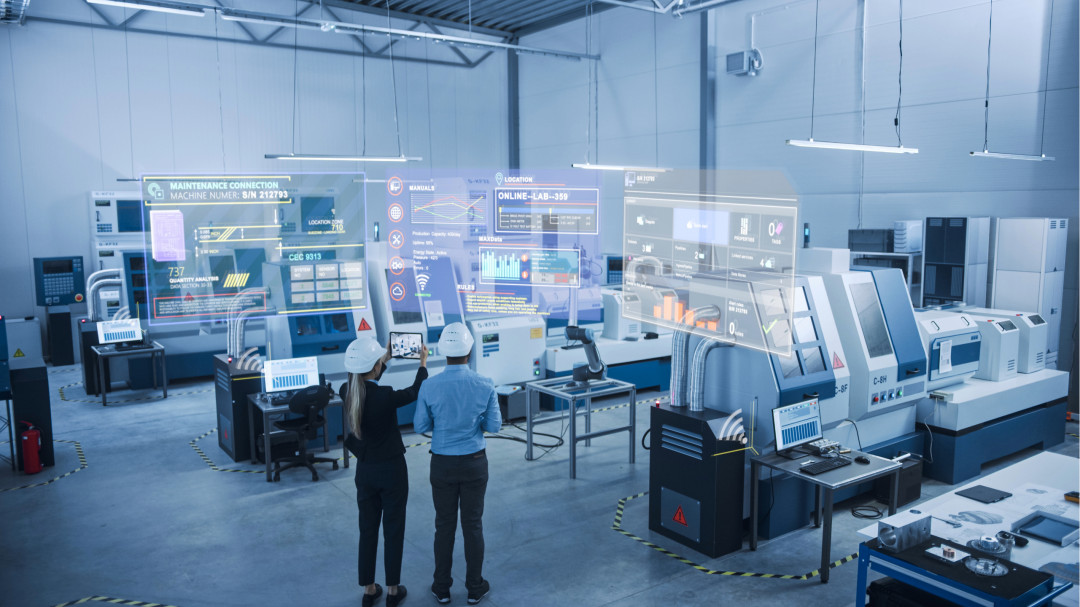
Abstract
Die deutsche Industrie steht vor Herausforderungen: hohe Löhne und Fachkräftemangel. Im Exzellenzcluster "Internet of Production" (IoP) der RWTH Aachen werden Lösungen entwickelt, um diese Probleme zu bewältigen und die industrielle Produktion zu revolutionieren. Durch die virtuelle Abbildung realer Produktionsprozesse und die Vernetzung aller Komponenten wird eine intelligente und effiziente Fertigung angestrebt.
Prof. Christian Brecher und sein Team forschen an Schlüsseltechnologien für die "Industrie 4.0", darunter die Nutzung maschinellen Lernens und die Erstellung eines "Digitalen Schattens", der Produktionsprozesse in Echtzeit darstellt. Diese Ansätze sollen zu besserer Qualität, höherer Produktivität und mehr Nachhaltigkeit führen.
Das IoP integriert interdisziplinär über 35 Lehrstühle und Forschungseinrichtungen und erhält erhebliche Fördermittel. Die Einbindung des Menschen bleibt trotz der fortschreitenden Digitalisierung zentral. Zudem werden ethische Fragen und der Schutz von Mitarbeiterdaten intensiv diskutiert.
Die Forschungen im IoP könnten die Effizienz der deutschen Industrie signifikant steigern und eine Antwort auf steigende Lohnkosten und Fachkräftemangel bieten.
Hohe Löhne, fehlende Arbeitskräfte - wie wird sich der Industriestandort Deutschland angesichts dieser Herausforderungen behaupten können? Im Exzellenzcluster Internet of Production (IoP) der RWTH Aachen wird an Lösungen gearbeitet und bereitet damit den Weg in eine neue industrielle Ära vor: Die reale Produktion wird virtuell abgebildet, alles ist mit allem vernetzt und wird intelligenter. Aber der Mensch bleibt unverzichtbar.
Lohnkosten gehören neben Material- und Energiekosten zu den Schlüsselaufwendungen einer Produktion. Anders als Material- und Energiekosten gebe es bei den Lohnkosten in Deutschland keine Schwankungen, sie zeigten nur in eine Richtung - nach oben, stellt Frank Possel-Dölken fest. Er gehört zur Geschäftsführung des lippischen Unternehmens Phoenix Contact, einem Hersteller von Lösungen für die industrielle Elektro- und Automatisierungstechnik. In dem Unternehmen mit 22.000 Mitarbeitenden verantwortet er die Digitalisierung. „Am Ende muss man sich überlegen: Gibt es Ansätze, damit man sich diese Lohnsteigerungen leisten kann?“ Das Unternehmen ist zwar weltweit aktiv, generiert aber 70 Prozent seiner Wertschöpfung in Deutschland. Man müsse mit Hilfe der Technologie Wege der Effizienz finden, um die Balance zu halten, meint der Digitalchef Possel-Dölken.
Mit solchen Überlegungen steht er nicht alleine da. „Es gibt große Unternehmen, die sagen, ich habe keine Chance, diese Lohnsteigerungen darzustellen“, stellt Universitätsprofessor Christian Brecher, Inhaber des Lehrstuhls für Werkzeugmaschinen am Werkzeugmaschinenlabor WZL der RWTH Aachen fest. Die Lohnkosten in der deutschen Industrie lagen im Jahr 2022 gut 44 Prozent über dem EU-Durchschnitt. Daneben wird sich das Problem des Arbeitskräftemangels weiter verschärfen, wenn die Baby Boomer in den nächsten Jahren in Rente gehen. Daraus ergeben sich Aufgaben für die Wissenschaft. „Wie können wir die Standortbedingungen für die Industrie in Deutschland noch besser gestalten“, fragt der Wissenschaftler. „Wie kann man den Menschen dabei einbinden und versuchen, Schritt für Schritt besser als die anderen zu sein, so dass die Lohnkosten zu rechtfertigen sind?“ Zielsetzung seien beste Qualität, höhere Produktivität und mehr Nachhaltigkeit.
Verbund der Spitzenforschung
Brecher ist Sprecher des Exzellenzclusters IoP. In dem Verbund der Spitzenforschung arbeitet der Maschinenbauer mit über 35 Lehrstühlen und Forschungseinrichtungen in Aachen interdisziplinär zusammen. Sie bereiten den Weg in eine neue industrielle Zukunft. Zielsetzung ist die kontinuierliche Entwicklung eines komplexen Netzwerks aus Maschinen, Software, Datenspeichern und Menschen, die Daten in Echtzeit austauschen und damit intelligent arbeiten können. Das IoP ist eines von bundesweit 57 Exzellenzclustern des Bundes und der Länder, die in Summe jährlich mit 385 Millionen Euro gefördert werden. Mit Beginn der zweiten Förderphase in 2026 soll die jährliche Fördersumme für bis zu 70 Exzellenzcluster auf insgesamt 539 Millionen Euro steigen.
In dem Aachener Forschungsverbund geht es um Schlüsseltechnologien für die Produktion der Zukunft und damit um den Kern der so genannten „Industrie 4.0“, die oft als vierte industrielle Revolution bezeichnet wird. Nach Einführung der Dampfmaschine, der elektrischen Energie und des Computers geht es jetzt um eine neue Dimension der Digitalisierung: Sie soll eine bedarfsgerechte Datenanalyse z. B. durch maschinelles Lernen möglich machen, und zwar ganzheitlich auf alle Aspekte der Produktionstechnik bezogen: Angefangen bei der Produktentwicklung, dem Design und der Materialauswahl, über die Fertigung und Montage bis hin z. B. zu neuen Geschäftsmodellen.
„Wir haben uns schon lange angesehen, was der Mensch macht. Wir haben analysiert, was an der Werkzeugmaschine passiert“, macht der Geschäftsführer des Clusters, Christian Fimmers, die Neuerung deutlich: Wenn der Controller jetzt bei einer Qualitätskontrolle ein Problem feststellt, dann kann er sich die Gesamtheit der Informationen, sowohl von Maschinen als auch von Mitarbeitenden, anschauen und prüfen, wo der Prozess von den Vorgaben abweicht. Die Daten bilden den Produktionsprozess virtuell und in Echtzeit ab, es ist der Digitale Schatten der realen Produktion. Dazu sind alle in die Fertigung eingebundenen Instanzen, also Menschen, Werkstücke und Maschinen mit Hilfe von Informations- und Kommunikationstechnologien intelligent miteinander verknüpft. Alle sollen am Ende direkt miteinander kommunizieren und kooperieren, auch unter Einbeziehung Künstlicher Intelligenz (KI).
„Big Data“ handhabbarer machen
Die Forschenden leisten dazu die Vorarbeit. Maschinen, Sensoren, Maschinensteuerung, aber auch der Mensch selbst selber, liefern bereits heute permanent Unmengen an Daten, die mit dem Begriff „Big Data“ bezeichnet werden. Damit diese „Big Data“ handhabbar werden, haben die Wissenschaftler eine intelligente Aufbereitung entwickelt: „Wir sprechen hierbei von unserem Konzept des Digitalen Schattens“, sagt Brecher und verdeutlicht das Vorgehen an einer projizierten Krawatte. „Im Schatten sehen wir nur die Kontur und nicht mehr die Farbe, erkennen aber dennoch, dass es sich eindeutig um eine Krawatte handelt. Das heißt: Wir specken diese digitale Welt mit höchstmöglicher Effizienz soweit ab, dass ich mit einem möglichst geringeren Datenaufkommen zum Ziel kommen kann.“ Die Forscher haben das mittlerweile so weit optimiert, dass die Berechnungen unglaublich schnell, sprich „in Echtzeit“ erfolgen. Darüber hinaus werden durch „Look ahead Funktionen“ ganz neue Wege der Qualitätsüberwachung möglich.
Wie wichtig das in der Praxis ist, macht Possel-Dölken von Phoenix Contact deutlich: „Es geht darum, sehr gute Informationen auf Knopfdruck verfügbar zu haben – welche Produktivität habe ich gerade, wo gibt es oder entsteht gerade ein Problem.“ Im Problemfall sei die Zeit ein entscheidender Faktor: Es mache den Unterschied, ob man vier Wochen brauche, um die Ursachen zu finden oder nur einen Tag. „Der Unterschied basiert in vielen Fällen auf der Verfügbarkeit der richtigen Information. Wie lange brauche ich, um darauf zugreifen zu können. Das ist einer der Kernfaktoren, um den Ausstoß in der Produktion zu erhöhen, um gute Qualität sicher herstellen zu können. Das ist ein ganz zentraler Aspekt gerade für den Standort Deutschland.“
Für den Digitalen Schatten haben die Forscher eine so genannte konzeptionelle Referenzinfrastruktur entwickelt, also einen Rahmen für die Gestaltung und Umsetzung Digitaler Schatten geschaffen. Der kann individuell angepasst werden. Die Referenz umfasst die Entwicklung von Modellen, Prozessen und Technologien, um Daten zu sammeln, zu speichern und zu verarbeiten. Eine Herausforderung ist dabei die Entwicklung eines gemeinsamen Modells für ganz unterschiedliche Maschinen. „Das ist ambitioniert. Aber das wäre, wenn wir das hinbekommen, ein Riesensatz nach vorne“, sagt Brecher. Zwei Institute erarbeiten das beispielhaft an einer Fräsmaschine und Kunststoffspritzgießmaschine. Beide haben unterschiedliche Steuerungen, Prozesse und Sensoren. Zuerst wurden für jeden Maschinentyp unterschiedliche Modelle erzeugt. „Irgendwann muss man sagen: Wo gibt es denn Gemeinsamkeiten, damit ich das Pferd nicht immer von neuem aufzäumen muss. Was lässt sich verallgemeinern, was lässt sich übertragen. Sonst ist die Technologievielfalt unbeherrschbar“, skizziert Christian Brecher das Vorgehen.
Der Mensch spielt weiter entscheidende Rolle
Und dann ist da der Mensch. Und den beziehen die Aachener in den Prozess von Anfang an mit ein - anders als in den neunziger Jahren bei der Einführung der computergestützten Fertigung. „Damals dachte man, es lässt sich alles automatisieren und hat den Menschen stärker ausgeblendet. Das hat am Ende nicht funktioniert“, sagt Brecher. Darum sind jetzt in dem ansonsten eher technisch orientierten Forschungsverbund auch die Fachrichtungen Psychologie und Arbeitswissenschaft, u. a. mit Professorin Verena Nitsch, vertreten. Nitsch macht deutlich, dass der Mensch bei aller Digitalisierung weiterhin eine entscheidende Rolle spielt und beschreibt die Probleme eines Autobauers. Der habe im Produktionsprozess extrem viel automatisiert und standardisiert. „Trotzdem stellte man überrascht fest, dass Autos aus verschiedenen Standorten sich in der erzeugten Qualität unterscheiden. Wie kann das sein, es ist ja alles standardisiert und automatisiert? Und es ist in beiden Werken exakt gleich. Es konnte also nicht an dem automatisierten Teil der Produktion liegen.“ Die Entwicklungen im IoP sollen daher den Menschen vor allem bei seinen Entscheidungen im Rahmen der Produktionsprozesse unterstützen.
Sie kommt zu einem sensiblen Punkt: Wenn Mensch und Maschine vernetzt werden, wenn von der realen Produktion ein virtuelles Abbild in Echtzeit entstehen soll, dann braucht man Daten auch von den Menschen. Wie weit kann und will man dabei in Deutschland gehen? „Da ist China natürlich proaktiver“, stellt sie fest. Kamerabasierte KI-Systeme sammelten dort Daten. „Zu Recht fragen wir uns alle: Wollen wir das in Deutschland?“ spricht die Arbeitswissenschaftlerin das Spannungsfeld an: „Wir wollen mehr Daten und wir brauchen mehr Daten. Wann gehen wir zu weit? Wann überwiegen die Nachteile gegenüber den Vorteilen?“ Niemand soll auf Schritt und Tritt überwacht werden oder negative Konsequenzen befürchten müssen. Aber auch hier greifen die Forschungsaktivitäten des IoP: Reduzierte, anonymisierte Daten sollen die angestrebte Kommunikation von Unternehmen untereinander ermöglichen. Das würde nach Einschätzung der Forschenden viele Probleme lösen, beispielsweise innerhalb der Lieferkette. An dieser Vision der Kommunikation von Unternehmen mit reduzierten, anonymisierten Daten arbeitet das IoP im Rahmen eines World Wide Labs. Das geschieht auch in Hinblick auf die Symbiose zwischen Mensch und Maschine.
Es gehe darum, Anforderungen und Probleme zu erkennen und Lösungen zu finden – wie bei den Mitarbeitenden, die automatisierte Prozesse überwachen und schnell eingreifen müssten, wenn irgendwas schieflaufe. Mit dieser Fragestellung habe sich auch das Cluster beschäftigt. „Wir haben uns angeschaut, wie können wir physiologische Daten verwenden - also die Herzratenvariabilität zum Beispiel, um eine Vorhersage treffen zu können, wie aufmerksam der Mensch ist.“ Bei nachlassender Aufmerksamkeit könnten Fehler schlechter entdeckt werden. Dadurch drohten Stillstände in der Produktion, schlimmstenfalls sogar Unfälle. Positionsdaten von Mitarbeitenden könnten auch mehr Aufschluss darüber geben, wann Menschen an bestimmten Plätzen sein müssten, damit die Produktion reibungslos laufe. Hier spielten Persönlichkeits- und Mitbestimmungsrecht sowie ethische Fragestellungen eine entscheidende Rolle.
Die Sicherung wertvollen Know-hows
Auf der anderen Seite geht es auch um die Sicherung wertvollen Know-hows erfahrener Mitarbeiter, die in Rente gehen. Klassisches Beispiel: Mit einem prüfenden Blick kommt ein Meister zum Schluss, ob ein Bauteil gut oder schlecht ist. Wie hat der das jetzt gemacht, fragt sich der jüngere Kollege. Das Cluster geht der Frage nach, wie dieses individuelle Fachwissen mit einem digitalen Ansatz beschrieben und damit gesichert werden kann - also möglicherweise mit dem Einsatz von Daten, die von künstlicher Intelligenz analysiert und mit Merkmalen versehen werden. Der Mensch ist sehr gut in der Erkennung von Mustern, erklärt die Arbeitswissenschaftlerin Nitsch den Ansatz: „Und wenn die Maschinen genau darauf trainiert werden, diese Muster zu erkennen, dann kann die Maschine auch lernen, diese Entscheidungen zu bewerten und mögliche Lösungen für den Entscheider vorschlagen. Und die nächste Generation von Mitarbeitenden kann dann wieder von der Maschine lernen.“ Aber am Ende würden immer noch Menschen die Entscheidung treffen müssen.
Die Industrie werde durch die Automatisierung in einigen Bereichen weniger Arbeitskräfte brauchen, die würden dann aber qualifizierter sein, sieht Wissenschaftlerin Nitsch eine Reihe positiver Effekte: „Die verdienen dann besseres Geld, in besseren Jobs, sie bezahlen mehr Steuern, davon profitiert das Land, davon profitieren die Unternehmen.“
In der aktuell angestrebten zweiten Projektphase der Exzellenzstrategie von 2026 an soll es für die Aachener im „Internet of Sustainable Production“ vor allem um den Aspekt der Nachhaltigkeit in der Produktionstechnik in ihren verschiedenen Dimensionen gehen: wirtschaftlich effizient, sozial verträglich und zudem ökologisch tragfähig. Beispielsweise um die Frage: Wieviel Lebensdauer hat ein Produkt oder eine Maschine verbraucht und wie viel Potenzial steckt noch drin. „Ein Auto fahren wir zehn bis zwölf Jahre. Danach ist es für uns weniger interessant, hätte aber das Potenzial, viel länger leben zu können“, macht Brecher deutlich, worum es dann gehen wird. Voraussetzung sei ein komplett anderes Produktdesign: „Es muss reparierbar und upgradefähig sein, so dass ich manche Sachen austausche und sage: Ich kann viele Komponenten weiter nutzen und halte das Produkt trotzdem up to date, indem ich beispielsweise Softwareupdates nutze. Das kann man sich bei vielen Produkten vorstellen.“ Dagegen sei die Frage, wie lange die Komponenten einer Produktionsmaschine halten, noch nicht beantwortet „Da bieten die Daten einer Maschine viel zu wenig Informationsgehalt. Statistisch gesehen bräuchte ich Unmengen an Antrieben, um zu sagen, meine Komponente hält unter den und den Bedingungen vielleicht noch tausend oder 10 000 Stunden“, skizziert Brecher das Problem. An einem Prüfstand müsste man tausende von Stunden Versuche fahren, um ein Ergebnis zu bekommen. Unrealistisch.
Eine Frage von Risiko und Nutzen
Auf der anderen Seite gibt es weltweit Maschinen, die diese Datengrundlage liefern könnten – wenn diese Maschinen vernetzt wären. Das würde auch bei ganz anderen Fragen helfen: Etwa beim Vergleich von Prozessen, die in einem Land zu besseren Ergebnissen führen als in einem anderen. Man könnte voneinander lernen. An der Stelle müssen die Aachener dicke Bretter bohren. Wer gibt schon freiwillig Produktionsdaten preis? Für Brecher ist es eine Frage von Risiko und Nutzen: „Wie überzeugen wir die Unternehmen, dass sie sagen: Der Mehrwert für mich, meine Daten stärker anonymisiert preiszugeben, dieser Nutzen ist mehr wert als das Risiko.“ Dass die Aachener Wissenschaftler mit Teilentwicklungen in Unternehmen gehen und den Nutzen demonstrieren, ist dabei sicher hilfreich.
In dem Cluster gibt es neben einem wissenschaftlichen Beirat auch einen Industriebeirat mit Vertretern deutscher und internationaler Unternehmen, zu dem neben z. B. BMW, MAN, Bosch oder Siemens auch Phoenix Contact gehört. Darüber hinaus sind die Cluster-Forschenden mit industriellen Vereinigungen wie dem Verband Deutscher Werkzeugmaschinenfabriken oder dem Verband der Automobilindustrie verbunden. Bei einem der jährlichen Treffen wurde Brecher mal gefragt, wann man denn das Internet of Production sehen könne. Die Antwort macht die Dimension dieses Projekts deutlich: „Das ist für eine Hochschule und für uns ein zu großes Programm. Wir können ja nicht mal eben Google oder Amazon spielen“, sagt Brecher mit Blick auf die US-amerikanischen Cloud Computing Anbieter.
Es gehe um Grundlagenforschung, Impulse und Transfer. Der Wissenstransfer hat im Cluster durch die Verbindung zur Industrie kurze Wege. Und so boten die Wissenschaftler Unternehmern in dem Zusammenhang an: „Wir checken mal, wie produktiv nutzt Du Deine Maschine.“ Mit den Werkzeugen und Methoden, die sie im Cluster erarbeitet haben, fanden sie dabei deutliche Verbesserungspotenziale heraus – sowohl mit, als auch ohne KI. Das schafft Vertrauen. Trotzdem wird die neue Ära der Produktion Zeit brauchen. Christian Brecher, sieht die Wissenschaft zehn bis 20 Jahre der Zeit voraus. Verena Nitsch unterstreicht, dass auch unerwartete Entwicklungen eine Rolle spielen können - so wie sich das Homeoffice nach Forschungen schon in den achtziger Jahren erst mit der Corona-Pandemie durchgesetzt habe.
Und der Digitalisierungschef von Phoenix Contact macht deutlich, wie viel Ausdauer der Weg ins Internet der Produktion braucht. „Das ist ein kontinuierlicher Prozess, an dem man in Dekaden arbeitet“, erklärt Possel-Dölken. Bei wesentlichen Fragestellungen dauere es etwa fünf Jahre, bis man Ergebnisse sehe und die Früchte einfahren könne. Und danach gebe es immer einen nächsten Schritt. „Es gibt keinen Zustand, in dem man sagt, das ist jetzt komplett.“
Schlagworte
AutomatisierungAutomobilindustrieDesignDigitalisierungFertigungForschungGestaltungIndustrie 4.0KommunikationLieferketteMaschinenbauNachhaltigkeitProduktionSoftware