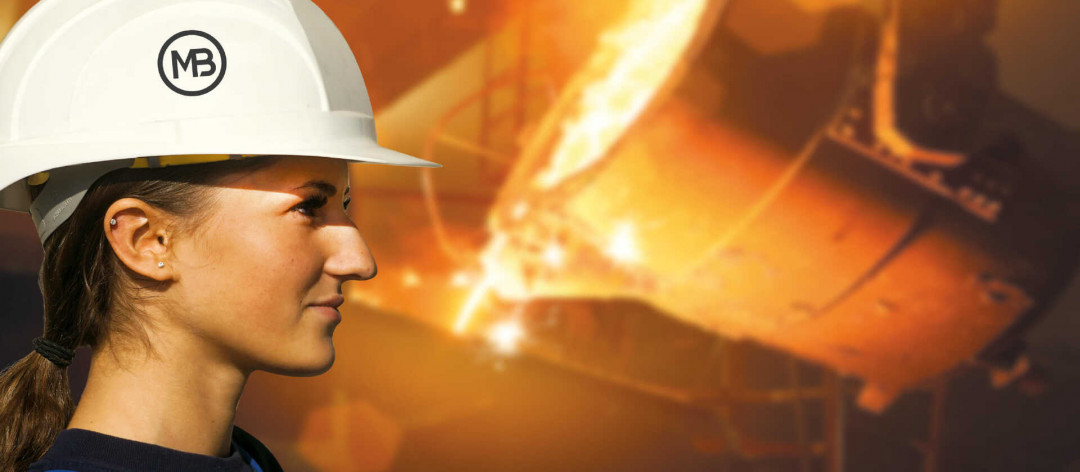
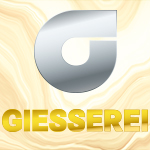
Das Familienunternehmen M. Busch wächst und modernisiert stetig. Neue Hallen, Hightech-Automatisierung und Investitionen in Millionenhöhe sind das Ergebnis einer modernen Unternehmensstrategie. Das Unternehmen fokussiert sich auf einbaufertige und vormontierte Lkw-Teile und baut sein Engagement im Bahnbereich aus. Mit zukunftsorientiertem Mindset und umfassenden Investitionen in Produktionsanlagen und Nachhaltigkeit stellen sich die Sauerländer den aktuellen Herausforderungen und bleiben wettbewerbsfähig.
VON CHRISTIAN THIEME, HAMMINKELN
Nutzfahrzeuge benötigen aufgrund ihres hohen Gewichts besonders leistungsfähige Bremssysteme. Eine schlechte oder defekte Bremsanlage ist hoch gefährlich, denn keine andere Komponente ist so wichtig für die Sicherheit. Wenn ein Lkw eine Vollbremsung macht, müssen mehrere Tonnen Gewicht so schnell wie möglich zum Stillstand gebracht werden. Nur mit hochwertigen Bremskomponenten kann das zuverlässig erreicht werden – denn im Ernstfall kommt es auf jeden Zentimeter an.
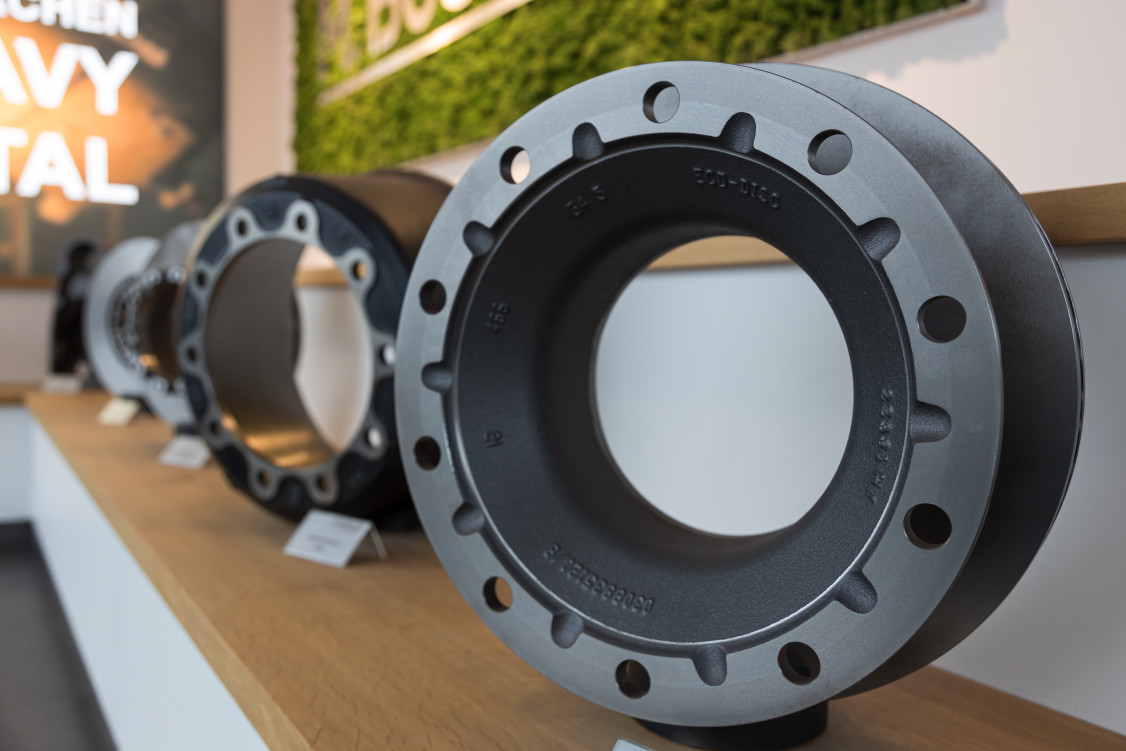
Hier kommt das spezielle Know-how von M. Busch zum Tragen: Das mittelständische Familienunternehmen hat sich als Großseriengießer auf den Lkw-Sektor fokussiert. Gut 80 Prozent macht dieses Geschäftsfeld aus. Dabei liegt der Fokus gleichmäßig auf Zugmaschinen und Anhängern – jeweils 50 Prozent des Portfolios. Hauptsächlich fertigt das Unternehmen Bremsscheiben, Bremstrommeln aber auch Schwungräder für Lkw und stationäre Motoren. Die restlichen 20 Prozent sind Produkte für Bau- und Agrarmaschinen und künftig mit steigendem Anteil auch Bremsscheiben für die Bahn. Andreas Güll, Geschäftsführer der M. Busch GmbH & Co. KG, betont die strategische Entscheidung: „In das Bahngeschäft sind wir vor anderthalb Jahren eingestiegen. Wir haben uns intensiv mit dem Thema beschäftigt und den Schienensektor als Wachstumsmarkt erkannt und entsprechend die Weichen gestellt.“ Derzeit verlassen jährlich 6000 Bremsscheiben für die Bahn das Werk, und die Prognosen zeigen eine deutliche Steigerung auf etwa 100.000 Stück in den nächsten fünf Jahren.
Investitionen für den Wachstumskurs
Schon von weitem ist zu sehen, dass auf dem Firmengelände in Bestwig gebaut wird. Zäune werden errichtet, neue Parkplätze und vor einigen Monaten ist sogar eine neue Halle eingeweiht worden. Direkt am Rande des Firmengeländes verläuft der viel befahrene Ruhrtal-Radweg denn nur wenige hundert Meter entfernt fließt die Ruhr durch das Tal. Die Geschichte des Unternehmens, das heute über zwei Standorte in Bestwig und dem 4,5 km entfernten Meschede-Wehrstapel verfügt und sich zu einem international agierenden Unternehmen der Automotivebranche entwickelt hat, begann 1830 in unmittelbarer Nachbarschaft. Die Zeit ist an diesem Ort aber keineswegs stehengeblieben. Hinter der Hallenfassade dominieren Automatisierung und Hightech.
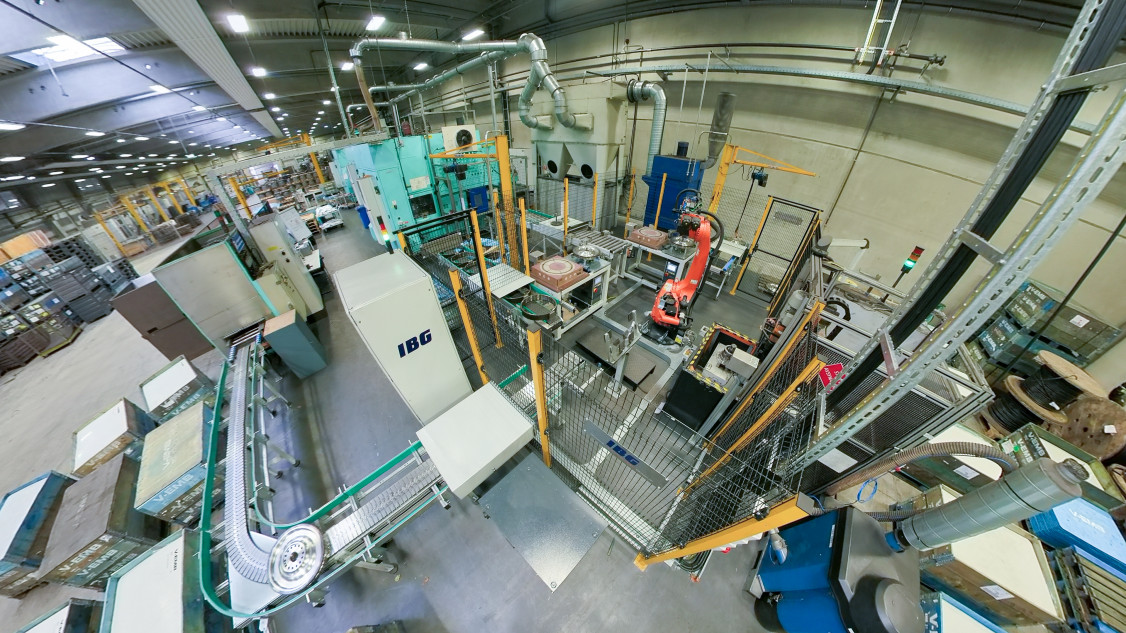
M. Busch setzt auf eine zukunftsorientierte Unternehmensstrategie, die sich als tragfähiges Fundament für den derzeitigen Unternehmenserfolg erweist. Güll unterstreicht die Bedeutung dieses Ansatzes: „Früher wurde nur eine einfache Jahresplanung durchgeführt. Diese haben wir abgeschafft und durch ein mehrjähriges Planungsmodell ersetzt“. Vor fünf Jahren initiierte das sauerländische Unternehmen die wegweisende Fünf-Jahres-Strategie „MB 2022“, deren Erfolg nun die Basis für den nächsten Strategiezyklus „MB 5.0 Next Level“ bildet, der bis 2027 angesetzt ist. Dieser umfasst 34 Projekte, die sich über alle Unternehmensbereiche erstrecken. Die neue Strategie ermöglicht es M. Busch, flexibler und gezielter auf Entwicklungen im Lkw-Sektor zu reagieren. Für das Unternehmen bedeutet strategische Planung jedoch mehr als nur Investitionsplanung. Sie beinhaltet ebenso die Festlegung von Visionen, Zielen und Werten, wobei ein besonderes Augenmerk auf der Transparenz gegenüber den Mitarbeitern liegt. „Bei den Mitarbeitern kommt das gut an, da sie eine Zukunftsperspektive erkennen. Es entstehen Ziele, an denen sich alle orientieren können“, konstatiert Güll.
Hinter den Strategiezyklen verbergen sich hohe Investitionskosten. In den vergangenen fünf Jahren hat das Unternehmen fast 30 Millionen Euro in seine Infrastruktur investiert. „Das ist für ein Unternehmen unserer Größe schon enorm“, betont Güll. Am Standort Bestwig wurden drei zusätzliche Bearbeitungslinien sowie eine neue Halle errichtet. Diese Expansion machte die Errichtung einer weiteren Logistikhalle notwendig, die neben einer neuen Verladehalle kürzlich in Betrieb genommen wurde. In der neuen Logistikhalle bietet sich nun Platz für die Zwischenlagerung von 2300 Paletten mit fertigen Produkten. Des Weiteren sind drei Kommissionierplätze entstanden, die zur Vorbereitung der Lkw-Beladungen dienen. In der neu eingerichteten Verladehalle können drei Lkw gleichzeitig beladen werden, was sowohl die Wartezeiten verkürzt als auch die Flexibilität des Unternehmens erhöht. Insgesamt sind auf diese Weise 4865 m² zusätzliche Hallenfläche entstanden, die zukunftsorientiert auch als Fertigungsfläche nutzbar sind.
Im Zuge der laufenden Erweiterungs- und Modernisierungsarbeiten erfährt auch das umliegende Betriebsgelände eine umfassende Neugestaltung. Die wartenden Lkw werden auf einen neuen Wartebereich verlegt, wodurch sich eine Blockierung des angrenzenden Ruhrtalradwegs zukünftig vermeiden lässt. Zusätzlich entstehen neue Parkplätze und auch in die Sicherheit wird massiv investiert. Hierzu wird das gesamte Areal eingezäunt und der Zutritt über spezielle Systeme gesichert, auch als Voraussetzung für die TISAX-Zertifizierung.
„Die neue Fertigungslinie ist Teil unserer Strategie“, konstatiert Güll. „Wir möchten die Wertschöpfung weiter ausbauen, d. h. wir wollen nicht nur gießen, sondern immer mehr Teile einbaufertig bearbeiten und vormontieren“. Diese Ausrichtung zielt darauf ab, die Fertigungstiefe zu erhöhen und damit die Abhängigkeit von reinen Gussaufträgen zu verringern. Güll betont, dass bei einem einfachen Rohteil die Gefahr besteht, dass Aufträge leichter verlagert werden können. Dieses Risiko minimiert sich jedoch, wenn das Unternehmen in die Bearbeitung und Vormontage investiert und fertig bearbeitete Gussteile liefert. Im Fall der Fertigungslinie hat M. Busch einen Zehn-Jahres-Vertrag mit Volvo abgeschlossen. Für das Fertigungswerk in Bestwig ist es ein Zusatzauftrag, das Rohteil hingegen wird schon seit Jahren in der Gießerei in Meschede hergestellt. Beide Werke profitieren vom Vertrag, denn das Rohteil wird weitere zehn Jahre im Sauerland gegossen. „Die Fertigungslinie stellt aber nicht nur eine Kapazitätserweiterung dar, sondern gleichzeitig den neuen Benchmark in Sachen Produktivität, Automatisierung, Energieeffizienz und Qualität für diese Produktfamilie, fügt Güll hinzu. Der hohe Grad an Automatisierung basiert nicht nur auf standardisierten Fertigungsprozessen, sondern auch auf einem individuellen Konzept, das Roboter sowie Überwachungs- und Kamerasysteme umfasst. Güll erklärt weiter: „Ein Mitarbeiter pro Schicht fertigt auf dieser Anlage ohne manuelle Tätigkeit im 3-Schichtbetrieb 360.000 Lkw-Bremsscheiben, einbaufertig bearbeitet, vormontiert, kontrolliert und versandfertig verpackt – das schafft bislang niemand außer uns“.
M. Busch sieht sich in Bezug auf die zunehmende Verbreitung der Elektromobilität gut positioniert. „Wir haben einen Anteil von etwa zehn Prozent an unserem Umsatz, der künftig von der E-Mobilität betroffen sein wird“, so Güll. Trotz der fortschreitenden Entwicklung in der Elektromobilität, liegt der Schwerpunkt des Unternehmens weiterhin auf der Produktion von Bremstrommeln und Bremsscheiben. Diese Komponenten sind auch für Elektrofahrzeuge unerlässlich, da sie trotz der Rekuperation nach wie vor benötigt werden.
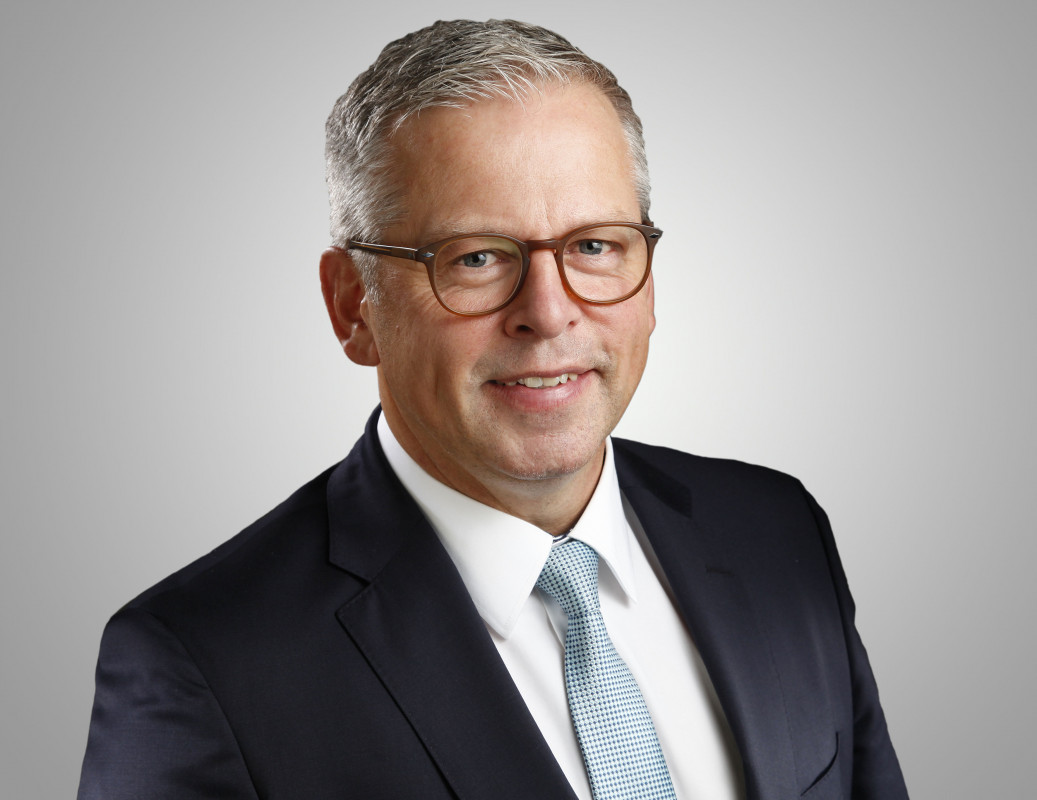
Wertschöpfungtiefe als Schlüssel zum Erfolg
Besonders stolz ist Güll auf den hohen Anteil der Wertschöpfung, was seiner Meinung nach eine „absolute Besonderheit“ auf dem Markt ist und Zukunftssicherheit für die Gießerei bedeutet. „Nach den Investitionen der letzten fünf Jahre im Werk Bestwig, produzieren wir jetzt 82 Prozent unseres Gusses komplett einbaufertig und teilweise vormontiert.“ Diesen Anteil will das Unternehmen noch weiter steigern. Hierzu entsteht derzeit eine Schwungradlinie. Viele Truck-Hersteller bearbeiten noch selbst Gussteile. Sobald jedoch Fläche oder Investment benötigt wird, besteht für Unternehmen wie M. Busch die Chance in die Bearbeitung und Montage einzusteigen.
Auch am Standort in Wehrstapel hat das Unternehmen investiert – in den letzten zehn Jahren waren es 56,6 Millionen Euro. Der Fokus der aktuellen Investitionen liegt auf Automatisierung, der Steigerung der Produktivität sowie auf Nachhaltigkeitsaspekten. „An einer Fertigungslinie, an der früher Bremsscheiben von Mitarbeitern abgepackt, palettiert und umreift wurden, ist der Bereich inzwischen komplett mannlos automatisiert“, so Güll. Diese Entwicklung zeigt, wie das Unternehmen Technologie einsetzt, um Effizienz und Modernisierung in seinen Betriebsabläufen zu steigern.
Nach der Fertigstellung der neuen Hallen am Standort Bestwig gehen die Arbeiten auf den Dächern weiter. 1,2 Millionen Euro kostet die neue Photovoltaik-Anlage die auf drei Hallendächern installiert wird. Auf einer Fläche von 6800 m² wird später eine Leistung von 1122 kWp erreicht. Güll: „Das klingt enorm, macht aber für das Werk in Bestwig umgerechnet gerade mal 13 Prozent des Energiebedarfs aus. Für das Gesamtunternehmen sind es gerade mal 0,8 Prozent.“ In einem Gedankenspiel macht Güll deutlich, dass für eine vollständige Stromversorgung des gesamten Unternehmens rund um die Uhr an sechs Tagen in der Woche sieben Windräder mit einer Gesamtleistung von 6 Megawatt bei kontinuierlichem Wind erforderlich wären.
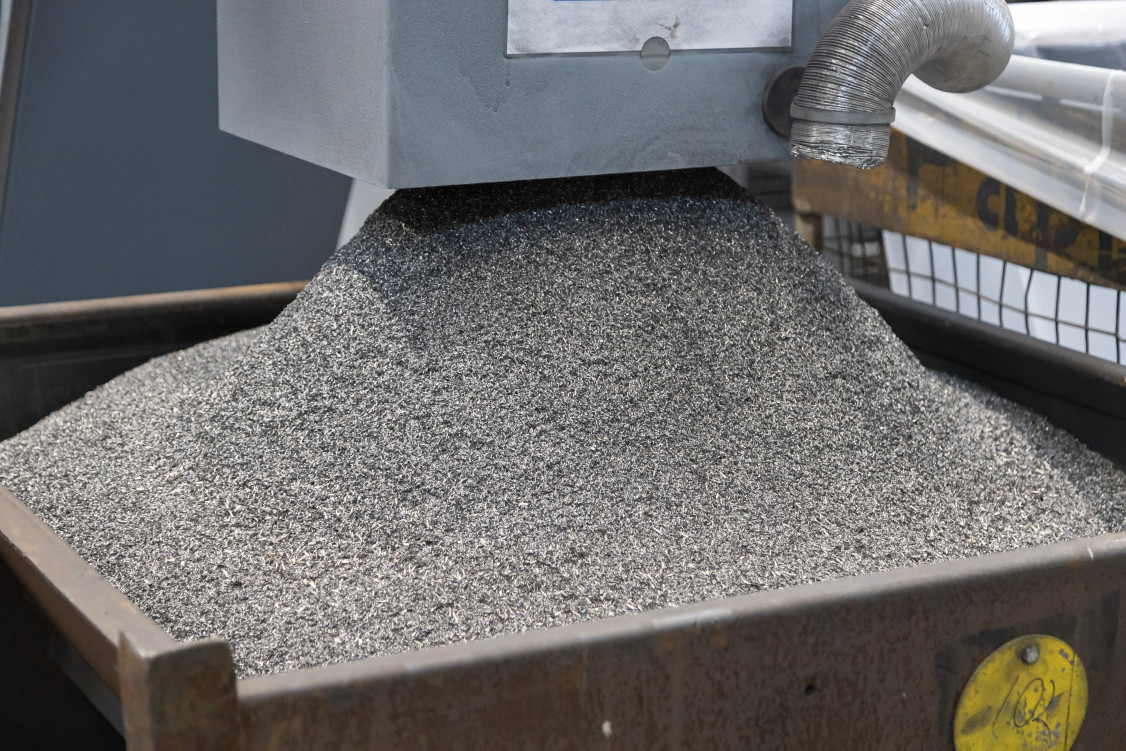
Die Energieversorgung spielt auch für M. Busch eine zentrale Rolle im zukünftigen Wettbewerb. Derzeit setzt das Unternehmen einen Kupolofen als Hauptschmelzaggregat ein, zukünftig könnten aber weitere Induktionsöfen den Prozess komplett übernehmen. Glücklicherweise verzeichnet das Unternehmen keine Engpässe beim Netzanschluss – ein Vorteil gegenüber einigen anderen Regionen Deutschlands. „Die Strompreise sowie die Netzentgelte sind ein erhebliches Problem“, bringt es Güll auf den Punkt. 16 Millionen Euro gibt das Unternehmen aktuell per anno für Energie aus, vor zwei Jahren waren es noch rund zehn Millionen Euro. Das Einsparpotenzial sieht M. Busch hauptsächlich in den Prozessen, die vor und nach dem eigentlichen Schmelzvorgang liegen. „Das nutzen wir natürlich, das ist Tagesgeschäft in energieintensiven Unternehmen. Damit kommt man ein Stück vom Energieverbrauch herunter, aber eben nur ein kleines Stück“. Im Wettbewerb sieht sich das Unternehmen hauptsächlich mit Polen und der Türkei, da die Energiepreise dort nur halb so hoch sind wie in Deutschland. Dies könnte, so Güll, insbesondere bei der Aushandlung neuer Verträge zu einem Problem für das Unternehmen werden.
„Der Energiepreis muss auf ein international wettbewerbsfähiges Niveau kommen, wodurch auch immer, und das langfristig und planbar“, fasst Güll zusammen. „Das kürzlich beschlossene „Strompreispaket“ ist leider wieder nur eine Luftblase für den energieintensiven Mittelstand, für uns bedeutet es keine Entlastung, sondern durch den Anstieg der Netzentgelte eine weitere Erhöhung der Stromkosten um einen hohen sechsstelligen Betrag. Wir hoffen und benötigen eine deutliche Nachregulierung, um die De-Industrialisierung durch künstlich erzeugte, nicht konkurrenzfähige Strompreise aufzuhalten.“ Trotz dieser Lage blickt M. Busch zuversichtlich in die Zukunft und trifft personelle Vorkehrungen, um den bevorstehenden Herausforderungen gerecht zu werden.
Attraktivität schaffen
Auf den Lkw-Planen des Unternehmens prangt der Slogan „Wir machen Heavy Metal“ und er ist Teil der Nachwuchskampagne von M. Busch. In puncto Mitarbeiter sieht sich das Unternehmen derzeit zwar gut aufgestellt, arbeitet aber strategisch daran, dass dies so bleibt. „Wir genießen einen guten Ruf in der Region“, so Güll. „Letztes Jahr hatten wir erstmals einen Tag der offenen Tür in Bestwig. Unter den über 1000 Besuchern waren auch viele aus anderen Bereichen der Umgebung. Als diese unsere Fertigung sahen, waren viele vom Automatisierungsgrad begeistert. Das alles macht Werbung für uns.“ Die Kombination aus attraktiver Bezahlung und positiver Mundpropaganda hat sich für M. Busch ausgezahlt. Alle zwölf Ausbildungsplätze für das Jahr 2023 wurden besetzt. Allerdings bedeutet es für M. Busch auch einen hohen Aufwand. Das Unternehmen hat in die Schaffung einer neuen Stelle investiert, die sich speziell um soziale Medien und die Außendarstellung kümmert. Zusätzlich wurden zwei hauptamtliche Ausbildungskoordinatoren eingestellt, die „die Sprache der Auszubildenden sprechen“. Der Einsatz von auffälligen Messeständen, Giveaways und neuen iPads für die Auszubildenden ergänzt das Engagement des Unternehmens. M. Busch nutzt soziale Medien gezielt für die Unternehmenskommunikation, wobei Facebook und Instagram für das Azubi-Marketing und LinkedIn speziell für den B2B-Bereich und die Ansprache von Führungskräften eingesetzt werden.
Große Personalfluktuationen gibt es bei M. Busch nicht. „Die meisten Auszubildenden bleiben hier“, erklärt Güll. „Der zweitgrößte Anteil geht in die Weiterbildung.“ Gleichzeitig betont Güll die Bedeutung des Leistungsprinzips im Unternehmen: „Es gibt auch Auszubildende, die bei uns nur eine zeitlich begrenzte Verlängerung oder keine Verlängerung bekommen. Wer aber Leistung bringt, kann sich hier im Unternehmen entwickeln.“ Das System scheint zu funktionieren, denn es kommen auch ehemalige Arbeitnehmer wieder, die woanders in der Branche Erfahrungen gesammelt haben. „Für uns sind das natürlich die besten Kommunikatoren“, freut sich Güll.
Nachhaltigkeit
Ein Blick in die Fertigungshallen zeigt, dass M. Busch auch in puncto Automatisierungstechnik weit fortgeschritten ist. Mitarbeiter sind nur wenige zwischen den gekapselten Fertigungsinseln zu sehen. In diesen Zellen läuft alles komplett automatisiert ab, teilweise unsichtbar. Selbst Tätigkeiten wie Staplerfahrten werden hier durch computergestützte Systeme erleichtert. Funkchips unter dem Hallenboden definieren Lagerplätze und Abstellflächen. Ermöglicht wird dies durch ein ausgeklügeltes Fertigungssteuerungssystem (Manufacturing Execution System, MES). Insgesamt über 80 Maschinen verschiedener Hersteller sowie mit unterschiedlichen Steuerungen haben die Sauerländer zusammengeführt. „Mit diesem System können wir genau in die Produktion schauen und erhalten wertvolle Informationen“, erklärt Güll.
In der Eisengießerei von M. Busch werden jährlich 130 000 Tonnen Eisen verarbeitet, wobei das Unternehmen eine Kombination aus Kupol- und Induktionsofen einsetzt. Ein Vergleich mit anderen Eisengießereien in Nordrhein-Westfalen zeigt, dass M. Busch einen bemerkenswert niedrigeren CO2-Ausstoß pro Tonne erzielt. Güll erklärt: „Das resultiert aus einer Mischung aus Technik, Prozessen, die wir um die Technik herum geschaffen haben und letztendlich auch durch unsere Führungskräfte und Mitarbeiter.“ Das Unternehmen hat das Potenzial zur Energieeinsparung früh erkannt und neben internen Maßnahmen auch am Projekt InnoGuss (s. Infokasten) des BDG teilgenommen. „Ein wichtiger Faktor ist unsere geringe Ausschussquote, die zu einem deutlich geringeren Energiebedarf führt“, ergänzt Güll. Hinzu kommen Maßnahmen wie eine Wärmerückgewinnung am Kupolofen für die Warmwasserbereitung und die Trockenöfen. Momentan sieht sich die Gießerei gut mit dem Kupolofen aufgestellt. „Ein reiner E-Schmelzbetrieb hat nicht nur Vorteile für uns, denn wir bräuchten deutlich mehr Energie im Gesamtprozess, da die Wärme-Rückgewinnung mit den neuen Öfen deutlich geringer ausfallen würde.“ Aktuell wird die anfallende Prozesswärme nur innerbetrieblich genutzt. Theoretisch könnte ein Teil der Restwärme extern genutzt werden, um die Effizienz weiter zu steigern. Obwohl es derzeit keine Gespräche mit der Stadt gibt, ist sich Güll sicher, dass solche Themen bald im Rahmen der kommunalen Wärmeplanung diskutiert werden. Allerdings könnte es dann bereits zu spät sein, da schon ein Konzept zur Umstellung auf den E-Schmelzbetrieb vorliegt, das zeigt, dass dann keine Wärme mehr für andere Abnehmer zur Verfügung stünde.
Das Bewusstsein für Umweltthemen, insbesondere für den CO2-Fußabdruck, spielt eine wesentliche Rolle für Unternehmen in der Automobilgussbranche, wie M. Busch. Um seinen CO2-Fußabdruck effektiver zu managen, hat sich das Unternehmen in das Projekt FRED (Footprint Reduction Tool, s. Infokasten) eingebracht. Güll erläutert die Bedeutung dieses Schritts: „Der Vorteil ist, dass das System Allgemeingültigkeit besitzt. Wir hatten vorher begonnen den CO2-Footprint selbst zu ermitteln, aber das ist ein komplexes Thema. Mit FRED ist nun Vergleichbarkeit gewährleistet, ein absoluter Vorteil“. Güll ist überzeugt davon, dass die Ermittlung des CO2-Fußabdrucks bald für alle Unternehmen in der Branche zum Standard werden wird. Er betont jedoch, dass die Verfügbarkeit aller relevanten Daten aus den Betriebsbereichen eine Herausforderung darstellt, insbesondere für kleinere Gießereien, da die Struktur zur Datenerhebung erst entwickelt werden muss.
Das Engagement von M. Busch in verschiedenen Bereichen, einschließlich der nachhaltigen Unternehmensführung, hat zu positivem Feedback geführt und bestätigt den eingeschlagenen Kurs des Unternehmens. In Bestwig blickt man optimistisch in die Zukunft und ist bereit, sich neuen Herausforderungen zu stellen. Dies unterstreicht die Notwendigkeit für Unternehmen, sich kontinuierlich weiterzuentwickeln und an Veränderungen anzupassen.
InnoGuss
Mit dem Projekt „InnoGuss“ sollen innovative Transformationspfade speziell für Gießereien in NRW entwickelt und die dafür relevanten technischen, wirtschaftlichen und politischen Randbedingungen abgeleitet werden. Die Projektkoordination erfolgt durch den Bundesverband der Deutschen Gießerei-Industrie (BDG), unterstützt durch die BDG-Service GmbH und das VDEh-Betriebsforschungsinstitut (BFI).
www.guss.de/innoguss
FRED
FRED steht für Footprint Reduction Tool, mit ihm können Gießereien den Carbon Footprint ihrer Produkte und ihres Unternehmens ermitteln – und so auch eine Dekarbonisierungsstrategie für ihren Betrieb entwickeln. Die Software ist regelkonform zum Rulebook der OEM-Plattform Catena-X und zertifiziert nach Gutcert und DIN EN ISO 14067. Mit FRED können auch prozess- und standortspezifische CO2- Minderungspotenziale identifiziert und als Grundlage für die Dekarbonisierungsstrategien eines Unternehmens genutzt werden. Ein absolutes Alleinstellungsmerkmal des CO2-Kalkulationstools ist außerdem eine Referenzdatenbank mit industriellen Echtdaten zu Energie- und Materialverbräuchen www.fred-footprint.de
Schlagworte
AutomatisierungEisenEnergieeffizienzFertigungForschungGestaltungGussGussteileKommunikationLogistikMarketingMesseNachhaltigkeitPlanungProduktionSicherheitSoftwareVerlag